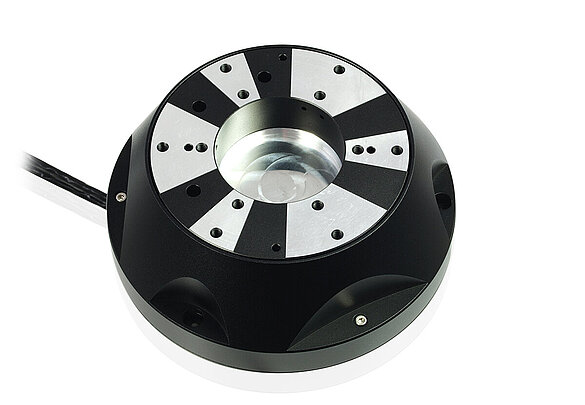
Small motion often has a great effect. For example, inaccurate motion resulting from guiding errors, machining processes etc. can interfere with precision machines during production to such an extent that the result becomes unusable.
The constantly increasing requirements on quality and performance of the product make it necessary to avoid these types of problems. If the motion is not compensated, production tolerances can go out of control and in the worst case, faulty products could be produced.
What Must a Compensation be Capable of?
The requirements on the systems necessary for motion compensation are high. Precise, repeatable motion with the same dynamics and accuracy on all linear and rotary axes is therefore necessary. At the same time, this involves running high-precision trajectories with the corresponding dynamics. Therefore, multi-axis, precise, and dynamic positioning systems are necessary.
Dynamic Hexapods with Piezo Drives
Thanks to their parallel kinematic design, hexapods provide the best conditions for this purpose. Their advantages compared with serial, i.e. stacked systems, are that they have much better path accuracy, repeatability, and flatness. In addition, the moved mass is lower, enabling better dynamic performance, which is the same for all motion axes. Moreover, cable management is no longer an issue, because cables are not moved, and, last but not least, the system features a much more compact design. For high-precision and dynamic compensation of predefined motion, PI offers hexapod systems that operate with repeatability in the nanometer range, thanks to piezo-based drives. Resonant frequencies of 1 kHz ensure fast position control. The space-saving, parallel-kinematic design allows a low overall height. This means that the hexapod can be integrated into machines where it is intended to compensate their guiding errors or proper motion. The piezo drives are free of wear and also operate under strong magnetic fields or in a high vacuum.