6-axis stages are often used in high-precision alignment applications including optics, photonics and semiconductor related applications. PI provides a broad range of 6-axis motorized stages based on parallel kinematic designs, mixed serial and parallel designs as well as 6-axis piezo nanopositioning stages, driven by piezo stacks with motion amplifiers and flexure guide mechanisms. The other models are based on crossed-roller bearings and piezo motors, providing longer travel ranges.
Piezo stack/flexure stages are completely free of friction, wear and maintenance and provide very fast response, settling and resolution without backlash and reversal play. Speed and performance are typically optimized for motion ranges of a few 100 microns. Much larger travel ranges are available with Hexapod 6-axis stages based on motorized screw drives or linear motors -they can handle large loads, as well. Five-axis and six-axis air bearing stages for 24/7 automation applications are also available from PI.
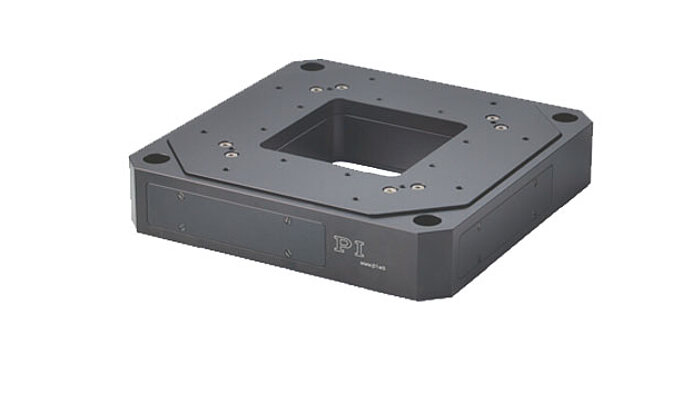
P-562 6-Axis Piezo Stage
High End Performance, 200µm
- 200µm linear motion (X, Y, Z)
- 1mrad rotation (pitch, yaw, roll)
- Sub-nanometer resolution
- Parallel kinematics/metrology
- PICMA® long-life piezo drives
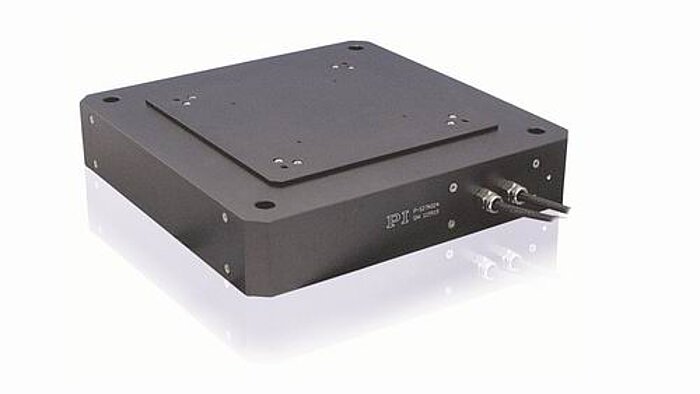
P-587 6-Axis Piezo Nanopositioner
Long-Travel, Parallel Metrology
- 800x800x200µm linear motion
- 1 mrad rotation (pitch, yaw, roll)
- For 6-axis scanning and positioning
- Precision trajectory control
- Direct capacitive feedback
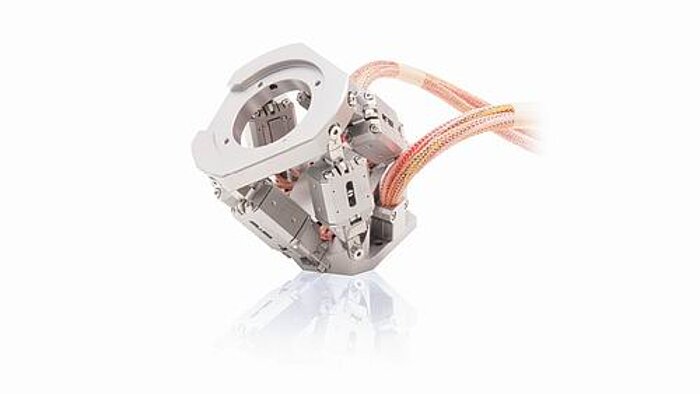
6-Axis UHV Hexapod
Technology Demonstrator
- 3x3x3mm XYZ travel
- 2x2x2° rotary travel
- UHV-compatible to 10-9 hPa
- Ø100mm base, 90mm height
- Piezo motor, non magnetic
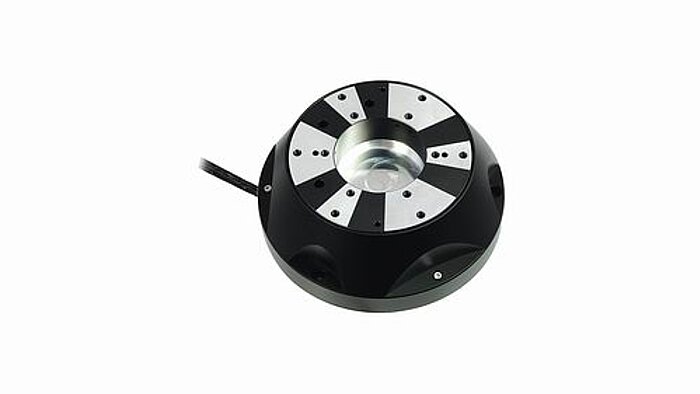
P-915 Piezo Hexapod
6-Axis, Highest Dynamics
- 70µm XYZ motion
- 1.4mrad rotation (pitch, yaw, roll)
- For 6-axis error correction
- Sub-nm repeatability
- Direct capacitive feedback
These 6 axis robot positioning stages are also called hexapod robots. They are based on a parallel-kinematic arrangement of 6 actuators to provide highly precise motion in all 6 degrees of freedom. Different types of motors, struts and linear motor designs are available to drive hexapod 6-axis precision robotic stages.
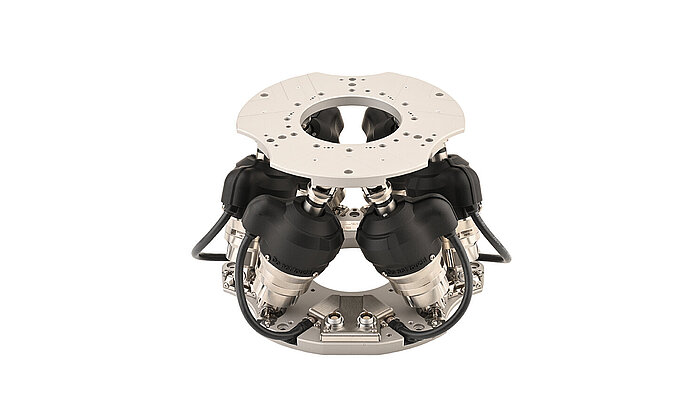
H-815 Rugged Hexapod
Brakes & Absolute Encoders
- 40x40x20mm XYZ travel
- 18x18x32° rotary travel
- 10kg load
- 100nm incremental motion
- 20mm/sec max. velocity
- Ø222mm base, 151mm height
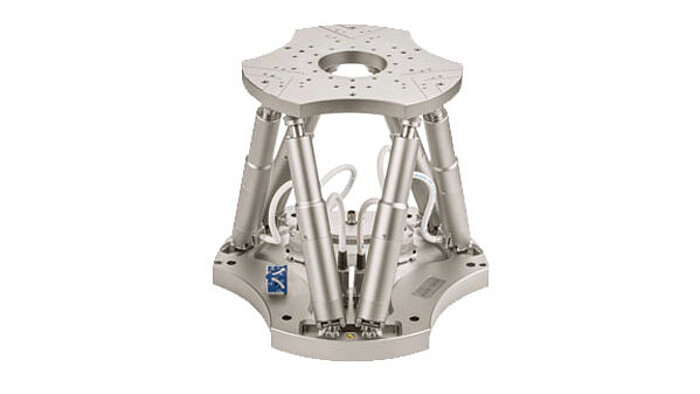
H-840 Hexapod w/Absolute Encoders
High Dynamics, Brushless Motors
- 100x100x50mm XYZ travel
- 30x30x60° rotary travel
- 30kg & 10kg load
- 8nm & 250nm actuator resolution
- 2mm/sec & 60mm/sec max. velocity
- Ø348mm base, 328mm height
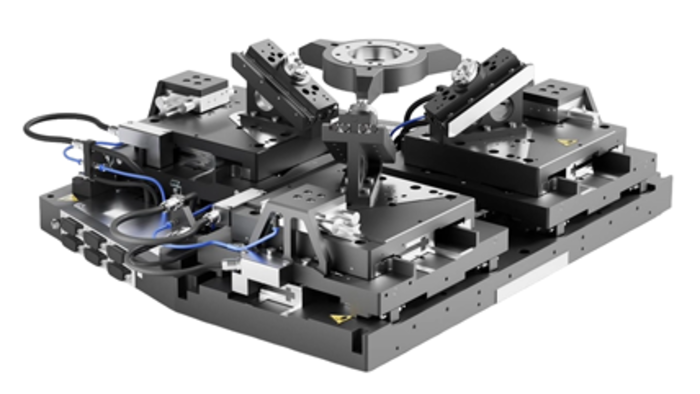
Fast 6-Axis Motion Platform
Hybrid Kinematics, Direct Drive
- 50x50x25mm XYZ travel
- 15x15x30° rotary travel
- 2kg load
- 1nm sensor resolution
- 500mm/s speed .5g acc.
- Linear motors, air brakes
With the use of flexures mechanisms, the motion of a piezo stack can be multiplied many times to achieve up to one millimeter travel (or more in extreme cases). Flexures can be designed to also double as guiding and preloading mechanisms. Flexure motion is based on the elastic deformation (flexing) of a solid material. Friction and stiction are entirely eliminated, and flexures exhibit high stiffness, load capacity, and resistance to shock and vibration. Flexures are maintenance free and not subject to wear. They are vacuum compatible, operate over a wide temperature range, and require neither lubricants nor compressed air for operation.