Highly accurate motion stages and controllers are at the core of most high-end metrology applications:
- CMM (Coordinate Measuring Machines)
- Optical metrology
- Semiconductor metrology
- Optical measurement systems
- Sensor test
Metrology encompasses all methodologies for acquiring measurements. Industrial metrology, a specialized branch, focuses on applications within the manufacturing sector. In industry, metrology primarily verifies dimensional accuracy, serving as a crucial method for quality control assurance. There are non-contact metrology instruments (mostly optical or capacitive) and contacting methods.
PI specializes a variety of ultra-high precision motion technologies ideal for metrology applications in optics, semiconductor, and photonics applications.
Technologies include air-bearing-based stages with or without integrated motors, granite-based motion systems with non-contact 3-phase motors, and piezo-driven stages. Air bearings are well-known for their smooth, frictionless motion and excellent geometric performance (flatness, straightness, pitch, yaw, roll, eccentricity, wobble, runout, etc.). Leading coordinate measuring machines utilize the extreme precision of air bearings.
Motorized air bearing rotary stages allow for precise control of speed and position with resolution down to the nanoradian range. The frictionless motion of the air bearing enables extremely tight tolerances in velocity control with minimum deviations.
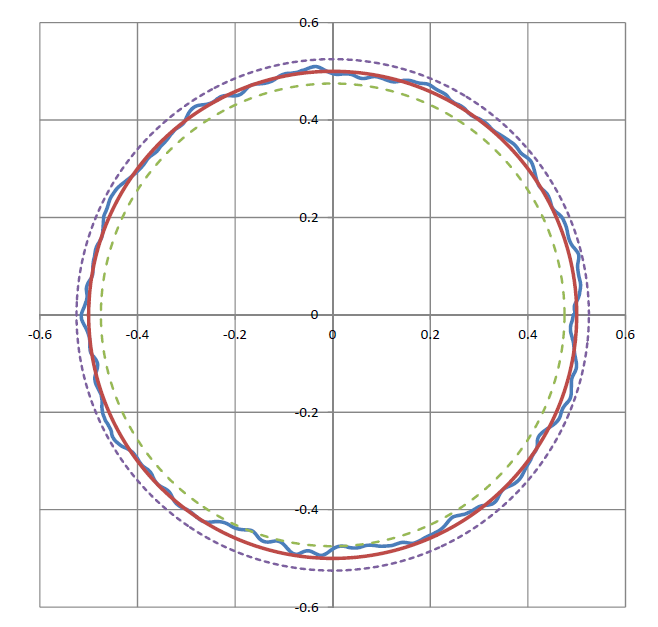
The preloaded motorized air-bearing rotary tables of the A-621 - A-627 family are designed to operate in any orientation with significant side loads of up to 1200N for the largest models. The low-profile rotary table family, A-635/A-637, is designed for horizontal use. All PI motorized air-bearing rotary stages feature high-performance, low-cogging, frameless, and slotless torque motors, with closed-loop optical incremental or absolute encoders.
Various options can be combined to create an ideal solution for point-to-point indexing or constant velocity scanning. Applications include optical alignment, metrology, inspection, calibration, and scanning. These precision rotation stages offer superior performance with minimized runout and wobble and excellent flatness. Being completely frictionless, they exhibit no breakaway "stiction" or drag friction during operation. They are ideal for use in cleanrooms, require no maintenance or lubrication, and have virtually unlimited lifetime. These air bearing stages can be operated by our A-811, single-axis controller or the A-814, multi-axis controller.
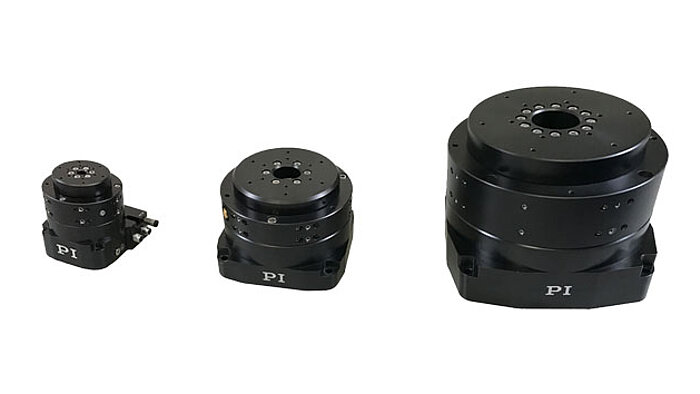
A-621 - A-627 Air Bearing Rotary Stages
Direct Drive, High Load
- 2/4/6/8/12” table diameter
- 13 to 420kg load
- 0.008µrad max. resolution
- 40 to 100nm flatness
- 500 to 2500 RPM max.
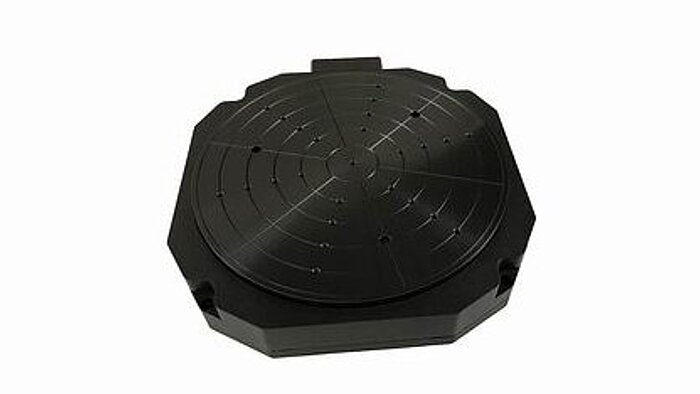
A-634 – A-638 Air Bearing Rotary Stages
Low Profile, Large Diameter
- 6/8/14” table diameter
- 20/32/60/120kg load capacity
- 0.03µrad max. resolution
- <100nm eccentricity & flatness
- 500 RPM max.
- Self-locking option at rest
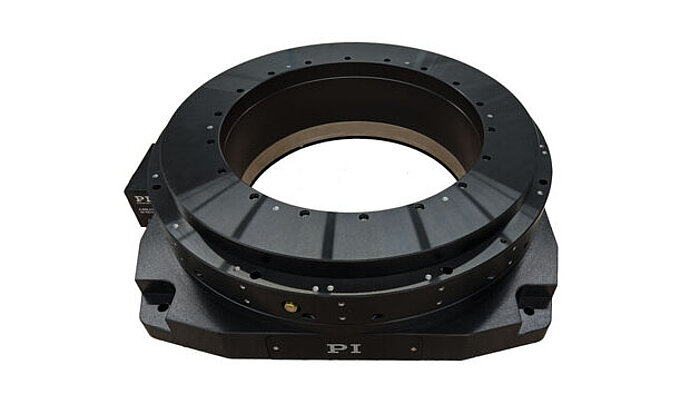
A-688 Air Bearing Rotary Stage
Large Clear Aperture
- ⌀260mm clear aperture
- 77kg load capacity
- 0.0015µrad max. resolution
- 500 RPM max.
- Flatness/Eccentricity <175/300nm
- Wobble: < 1µrad
- Direct drive
These single-axis rotary air bearings and 3-axis spherical rotary air bearings shown above come without motor but can be customized and encoder options are available for the single axis bearings. A manual X-Z-Tip-Tilt platform is available to help with the alignment of measured parts.
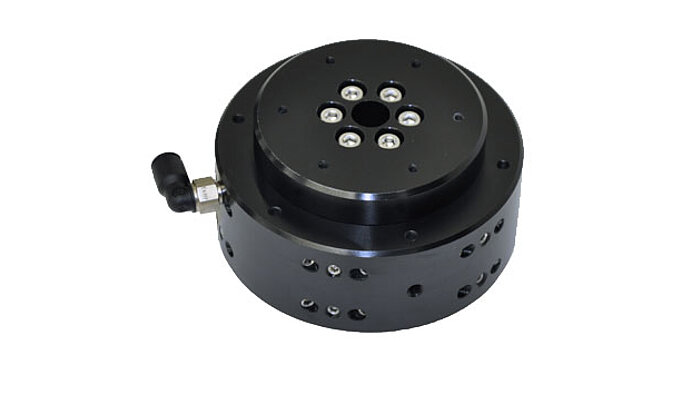
A-601 – A-607 Rotary Air Bearings
Non Motorized, Encoder Options
- Ideal for optics testing
- 2/3/4/6/8/12” table diameter
- 13 to 420kg axial load
- 5 to 270kg radial load
- 75 to 300nm eccentricity
- Optional high resolution encoder
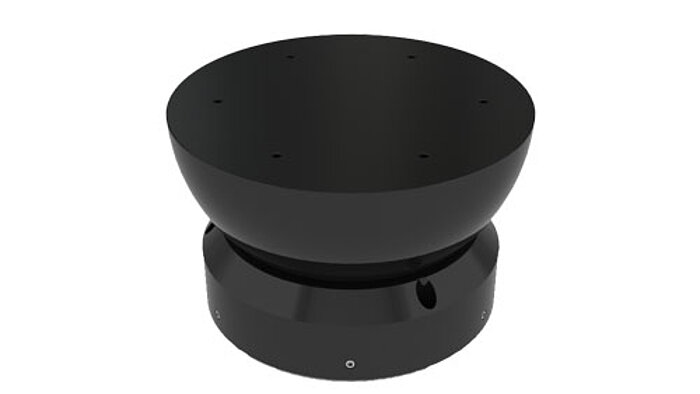
A-651 - A-657 Spherical Air Bearings
3 Degrees of Freedom
- Ideal for zero gravity simulation
- 2/3/4/6/8/10/12” sphere diameter
- 15 to 635kg load
- ±45 degrees rotation range
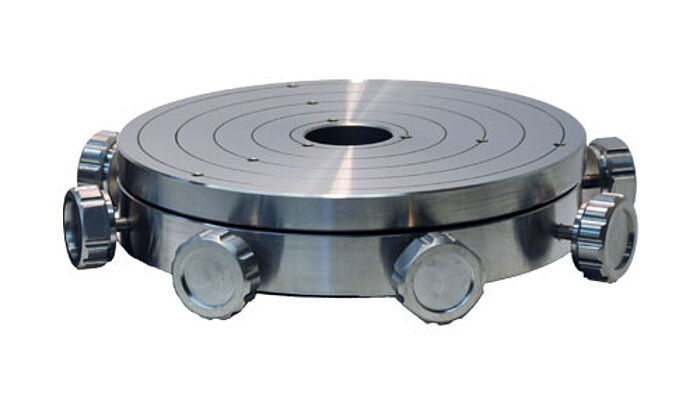
A-60x.MTT Manual X-Y-Tilt Platform
Add-On For Rotary Stage
- Ideal for optics testing
- 4 degrees of freedom: X, Y, θX, θY
- Manual operation
- Travel to ±3mm, ±1.25°
- 3/4/6/8/10” table diameter
- Direct mount on A-60x / A-62x
Air bearing XY stages and XY-theta stages provide a significant advantage over mechanical bearing metrology stages: they use the same reference plane for all degrees of freedom. With mechanical bearing stages, the Y-axis rides on top of the X-axis, regardless of whether you are looking at a stack of single-axis stages or an integrated XY stage. This stacked design means that the geometric errors of both X and Y add up. With a true planar air bearing stage (there is no such thing as a planar mechanical bearing XY stage), all axes ride on the same base plate with no accumulation of geometric errors. In addition to that advantage, the surface averaging effect of an air bearing itself provides great benefits over a mechanical bearing. Due to the single common base for the X and Y axes, torque and bending moments are eliminated and cannot influence the geometric performance (straightness, flatness) of the XY linear motion.
The A-322 three-motor XY-linear air bearing stage incorporates active yaw control using three (and optional four) motors and a flexural coupling element. In addition to linear motions in the X and Y axis, a small amount of rotational motion in theta Z is available for alignment or error correction of samples. The A-361 XY-Theta stage is a very compact design, again with one common base for all three degrees of freedom, providing a travel range of 5mm x 5mm x 2°. Of course, single axis linear stages are also available, as are Z-stages and custom multi-axis granite systems.
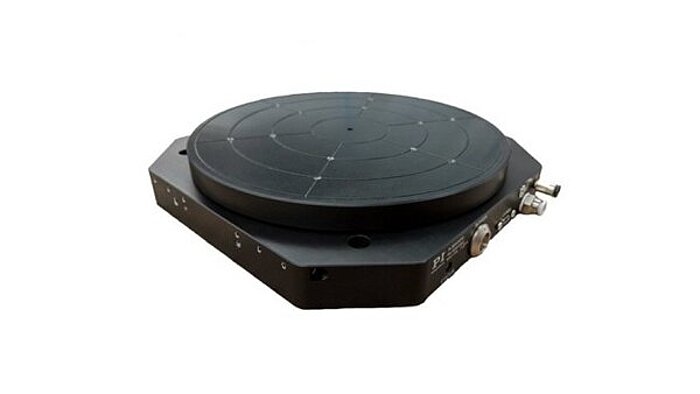
A-361 X-Y-θ Air Bearing Alignment Stage
Voice Coil Driven, Low Profile
- 5mm x 5mm x 2° Travel
- 40mm height, ø200mm
- Air Bearings & Voice Coils
- Parallel Kinematics
- Lock-down Capable
- 6-DOF Option
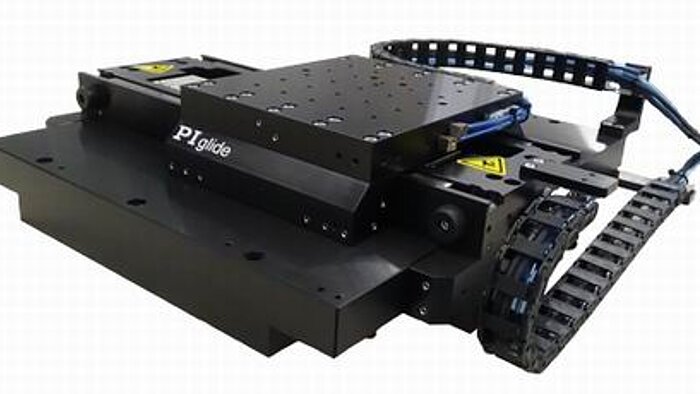
A-311 Planar Air Bearing Stage
Compact, Affordable, Al Base
- 50x50mm to 300x400mm travel
- 15kg load
- 1nm resolution
- Light weight, AL base
- Dynamic error mapping
- 2m/sec / 2.7g max. acceleration
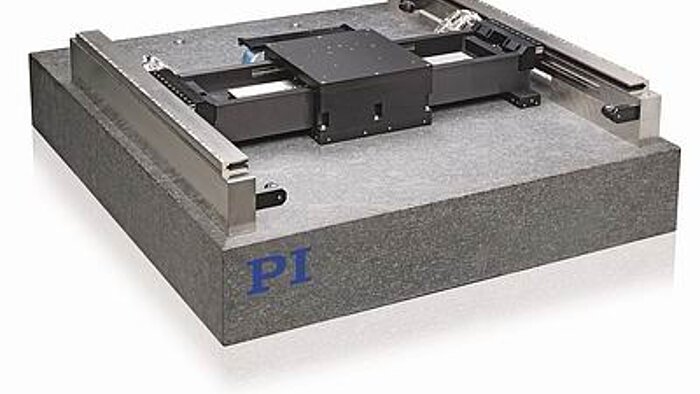
A-322 Planar Air Bearing Stage
3&4-Motor Designs, Granite Base
- 3 Models: Base, Plus, Ultra
- 500x1000mm max. travel
- 15kg load
- 1nm resolution
- Active yaw control flex coupling
- Dynamic error mapping
- 1m/sec / 2g max. acceleration
Manual Override of Air Bearings
All motorized air bearing stages can be positioned manually. All that’s required is to turn the servo off and keep the air flowing. Additionally, there is an option to turn the air off at any specified position and lock the stage into place.
Zero-Friction, Perfectly Silent, Zero Wear
Air bearings and air bearing stages are perfectly silent. Since the whole operation is frictionless – there are no gears, drive-screws, and mechanical bearings – there is also no wear. Eliminating wear means consistent performance and accuracy, year in year out.
High Speed
Because all our motorized air bearing motion systems use direct-drive linear or torque motors, they can move at very high velocities (up to 2 m/s and 2500 RPM, respectively). The high velocity and quick acceleration of these systems help save precious time and improve throughput without sacrificing quality.
For optical surface metrology, highly precise scanning systems are required. It is possible to either scan an optic or the complete sample. White-light interferometry is a widely used method in surface metrology. Here, sub-nanometer precise stages with extremely smooth motion of constant velocity are required. Piezo flexure-guided nanopositioning devices are well suited to meet all the requirements.
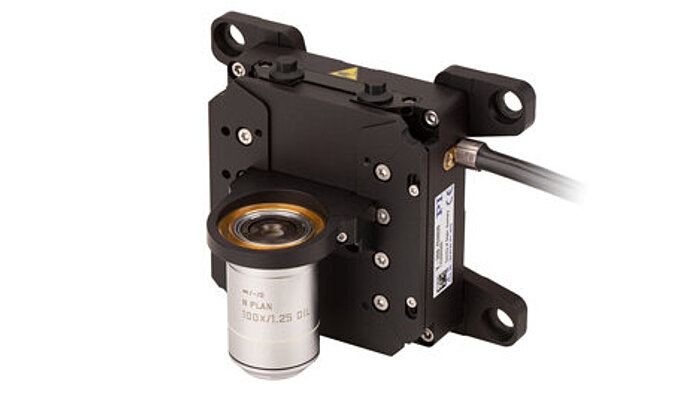
V-308 Fast Nano Focus
Voice Coil Scanner, 7mm
- 7mm motion
- Voice coil linear motor
- Adjustable Z-counterbalance
- Millisecond settling time
- 1nm sensor resolution
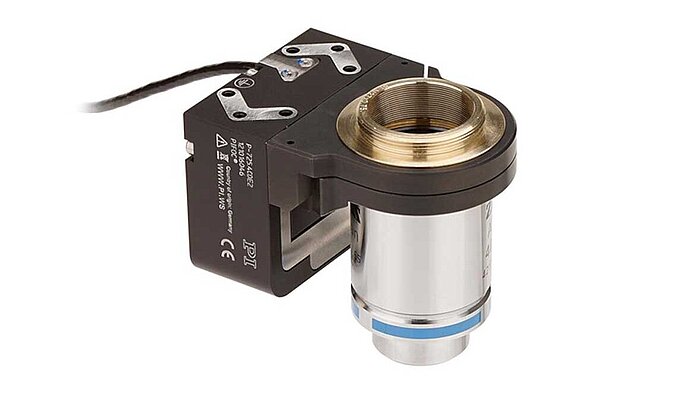
P-725 High Performance Piezo Focus Scanner
Up to 800µm, Sub-Nanometer Precision
- 100, 400, 800µm motion
- Combines higher dynamics & longer travel
- Millisecond responsiveness
- Ideal for autofocus, metrology, pathology
- New high performance controller
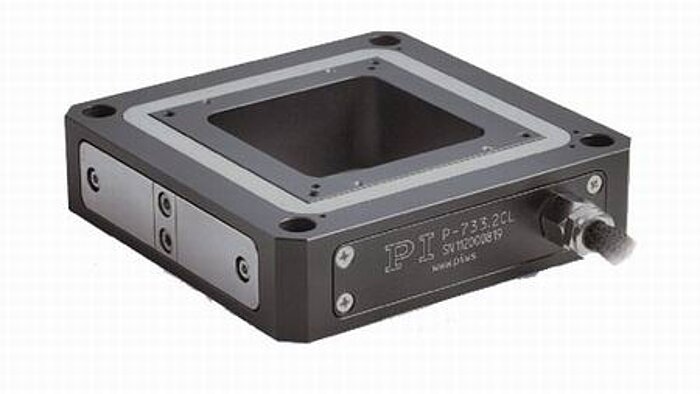
P-733 XYZ Piezo Scanning Stages
Parallel Metrology, 100µm
- 100x100x10µm motion
- <0.3 nanometer resolution
- Capacitive feedback
- 50x50mm aperture
- Frictionless precision flexure guides
To achieve precise control over focus in fast XY scanning applications, a highly dynamic Z-axis motion device is essential. Two established methods include voice-coil and piezoelectric drives, each offering distinct advantages: voice-coils provide longer travel ranges, while piezo-based systems offer superior resolution and dynamics. Both designs significantly outperform traditional stepper motor and leadscrew focus adjustment methods, which are occasionally used in less demanding surface metrology and microscopy applications.
Some metrology applications, such as the testing of aspheric optics, can benefit from 6D motion systems like hexapod parallel-kinematic mechanisms.
Hexapods provide precision motion in 6 degrees of freedom and a allow the user to freely program the center of rotation (pivot point). Hexapods have been successfully used in metrology tools for aspheric lenses. PI designs and manufactures a broad selection of standard and custom hexapod motion and positioning systems for handling of miniature optics and fiber optics all the way to heavy loads of 1000lbs and above.
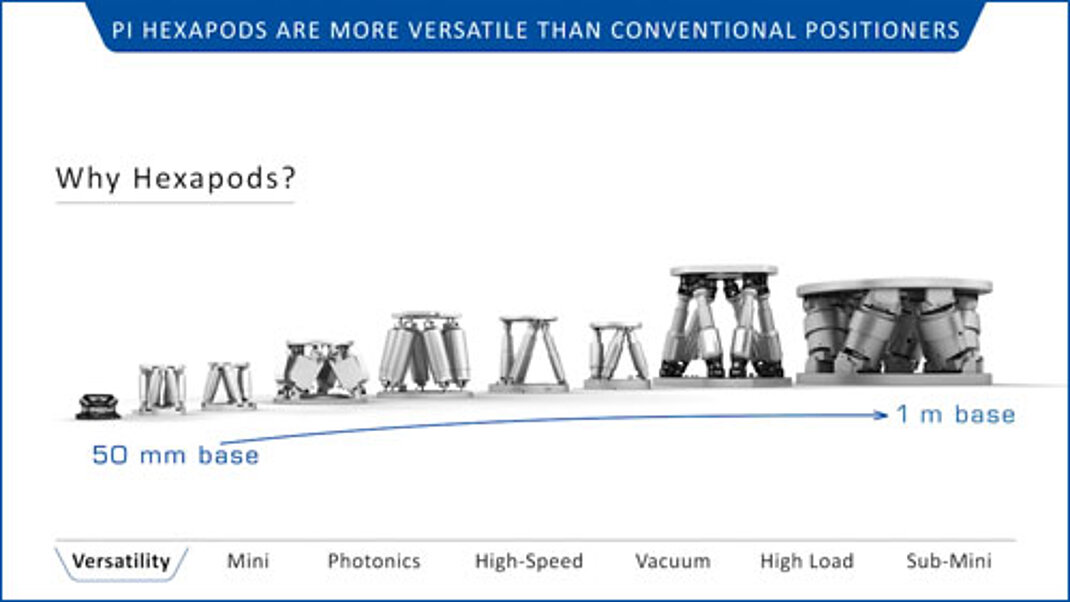
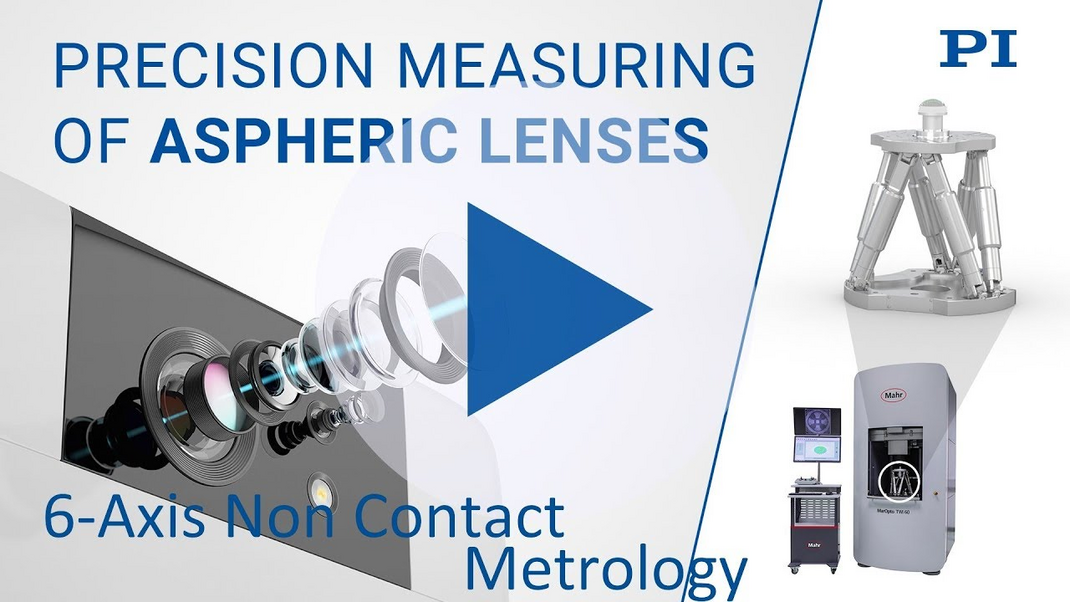
Wafer Stages for Thin Film Metrology and Glass Substrate Inspection
New 4DOF Piezo Nanopositioning Stage for Wafer Metrology
PDF: METROLOGY SYSTEMS USED AT PI TO DESIGN AND TEST HIGH PRECISION MOTION / POSITIONING SYSTEMS
PDF: FAST FOCUS CONTROL IN MICROSCOPY, LASER PROCESSING, SEMICONDUCTOR METROLOGY
PDF: Handbook of Optical Dimensional Metrology