Genome sequencing is pivotal in personalized medicine, offering crucial insights into an individual's genetic composition. Targeted genome sequencing, in particular, has transformed cancer research. Modern genome sequencing instruments employ various successful techniques to achieve their goals. A prominent approach known as the "sequencing-by-synthesis" method relies on fluorescent microscopy. Over time, significant advancements have been made in this technique, resulting in substantial improvements in speed and precision, which have increased by several orders of magnitude. Simultaneously, the costs associated with this method have significantly decreased. The progress can also be attributed to the advancements in precision motion control and positioning techniques utilized in the microscope systems designed for this specific purpose.
The performance of a "sequencing-by-synthesis" genome sequencer depends on many individual parts including lasers, optics, sensors, nanopositioning stages and advanced motion controllers. Nanopositioning stages are used in the Z-focusing mechanism as well as the XY positioning system moving the sample along.
There are two distinct motion techniques that have been used. The first is a step & settle process, involving incremental indexing steps, with a reading taken at each step. The other one can be less time consuming, with a continuous scan approach, where readings are taken continuously as the motion progresses. Both methods usually incorporate an X-Y motion element, responsible for moving the sample of interest, and a Z motion element, which moves an optic or sensor responsible for focusing during the operation.
Parameters Relating to Cycle Time
Frequency Response: Determines how a system responds to inputs and includes mechanical properties such as resonant frequency and closed-loop behavior and stability. Higher bandwidth usually means a more stable system that allows shorter cycle times. |
Step & Settle Time: The time from when a step command was given until the mechanical system has reached the commanded position and has stopped moving or oscillating |
Settling Band: The smaller the allowed settling band, the longer it takes for a mechanical system to reach the target. Example: it takes longer to reach stability within a position window of +/-10 nanometers than a much more relaxed requirement of +/-1 micrometer. |
Parameters Relating to Geometric Accuracy
Flatness of Travel: Describes the vertical deviation from motion in an ideal flat line |
Straightness of Travel: Describes the lateral deviation from motion in an ideal straight line |
Orthogonality: For XY motion systems, describes the deviation from the ideal 90-degree alignment between the two axes. |
Parameters Relating to Position Accuracy
Following Error: Describes the dynamic position error (difference between the expected position and the actual measured position) during a move. |
Velocity Constancy: Describes the positioning stage’s smoothness of motion or variation of velocity compared to the programmed, commanded velocity. |
Error Mapping: Describesa process that provides the controller with a compensation table based on interferometric position measurements during the initial factory test that can dynamically eliminate encoder pitch errors and cyclical interpolation errors. |
The "sequencing-by-synthesis" method involves the gradual incorporation of nucleotides with fluorescent markers, into a single-strand DNA (nucleic acid chain) using flow cells. A flow cell is a key component of certain sequencing technologies, usually a specially designed glass or silica slide with tiny channels or wells that hold the DNA fragments. This process is considered as 'synthesis'. When there is a recombination of the base pair, it generates a distinct fluorescent color signal within the visual spectrum for each of the four different base pair combinations: blue, green, yellow, and red. These signals can be detected using microscopic techniques. Due to the weak and short-lived nature of these signals, the detection and imaging process must be extremely rapid. To achieve this, two coordinated positioning processes are essential.
The first crucial step involves the precise positioning of the flow cell under the microscope objective. To achieve this, high-precision XY positioning stages are employed. The flow cell's size and geometric shape determine the analysis area, requiring a travel range of often more than 100mm. This positioning process must be executed swiftly, yet with exceptional accuracy to ensure the detection of all signals.
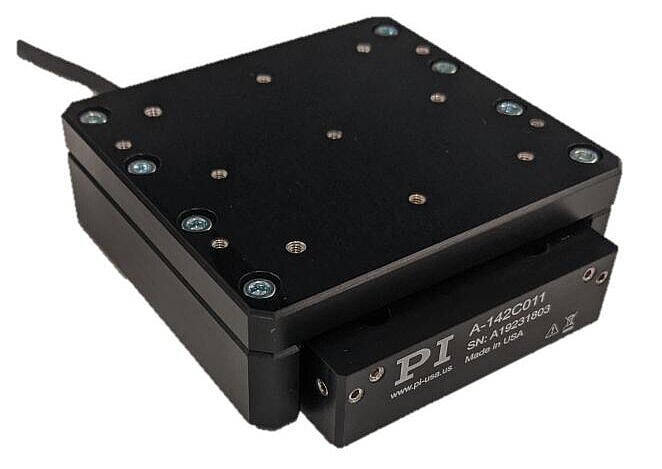
Furthermore, precise alignment of the objective along the optical axis within the lens's depth of field is essential. The depth of field can be in the range of a few hundred nanometers, depending on the lens's magnification factor. Achieving the necessary precision, speed, and dynamics is critical in this regard. This is because the occurrence of the fluorescence signal cannot be predicted precisely, and any potential tolerances of the flow cell, as well as slight pitch/yaw errors from the XY positioning stages, must be compensated for by the motion.
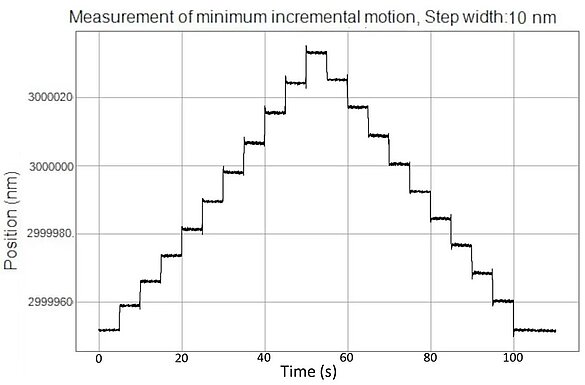
Depending on the design, images can be captured while the sample is in motion or in a static position, after a step and settle process. With step and settle, the exact location is known when the controller provides the information that the desired position has been reached. With the continuous motion method, the relevant position can either be calculated based on time, which means the following error and velocity constancy of a motion system are very critical, or by setting up triggers that are based on encoder signals and thus real-time position of the motion stage. In both cases, the stage accuracy, i.e., the deviation from the assumed position including encoder errors, servo bandwidth limitations and geometric errors have an influence on the quality of the imaging process.
Advanced system architecture and control algorithms, such as those on the ACS controller platform employed by PI motion systems, allow extremely tight velocity regulation and very fast step and settle times. Access to encoder signals is also made available with microsecond level precision. Using real-time encoder signals is the better method – it allows triggering of the camera at the right time, in the right position and improves the imaging quality.
On the stage side, the best performance in velocity control is enabled by using ironless, non-cogging linear motors — such as integrated in PI’s compact V-508 nanopositioning stage family or A-143 air bearing stage — or voice coil motors — such as used in the V-308 vertical nano-focusing stage. When maximum force in a compact package is required, iron-core motors are available. The undesired cogging behavior of iron-core motors can be significantly reduced with the anti-cogging control algorithms available on PI’s ACS-based motion controllers, resulting in a drastic improvement in velocity constancy.
For XY stage applications, geometric accuracy is very critical for system performance. Straightness, flatness, pitch, yaw, and roll errors contribute to the overall position uncertainty or sphere of confusion. Flatness deviations lead to vertical position fluctuations that need to be compensated by the vertical focusing mechanism. So, there is a commercial trade-off between dynamic requirements of the Z-focusing stage and the vertical ripple of the XY stage. Typically, 100nm flatness and straightness per millimeter of horizontal motion should not be exceeded. The higher the horizontal desired speed, the higher the Z-focusing stage dynamics requirements to deal with the higher frequency of the vertical fluctuations. If the Z-focusing stage is the limiting factor, a better XY-stage design with improved flatness is needed. The highest Z-focusing performance is typically available from piezo-flexure drives, such as PI’s P-725 PIFOC nano-focusing stages as these provide travel ranges up to 800µm. When even longer Z-travel ranges are needed, the V-308 voice-coil focus stage provides 7mm, a great alternative, also with nanoscale precision. Here, the PIone ultra-high precision encoder with 2µm pitch and 1nm resolution is employed. Gravity forces to 1kg can be compensated by the integrated, adjustable magnetic counterbalance. The counterbalance improves the motor performance by keeping it cooler, not having to work against gravity all the time. The net result is a cooler-running, higher dynamic system with a nice safety feature as a side-effect: in a power loss situation, the expensive optics on the stage will not crash into the sample.
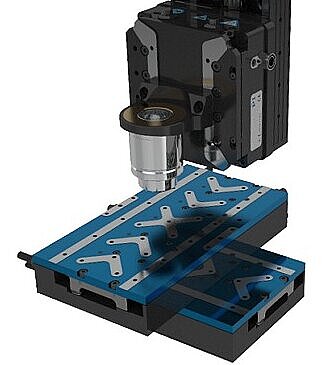
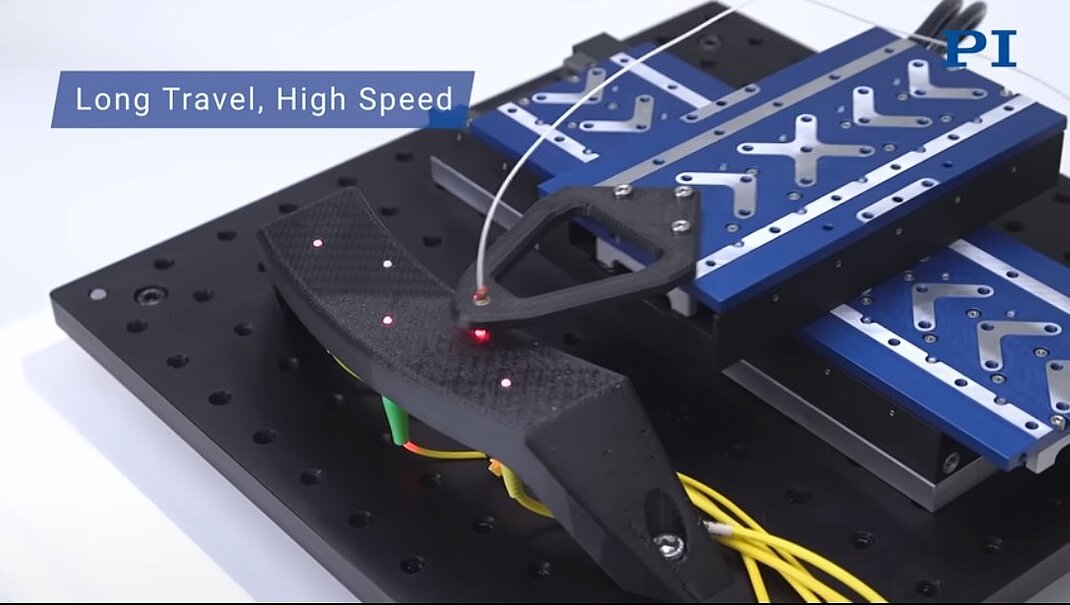
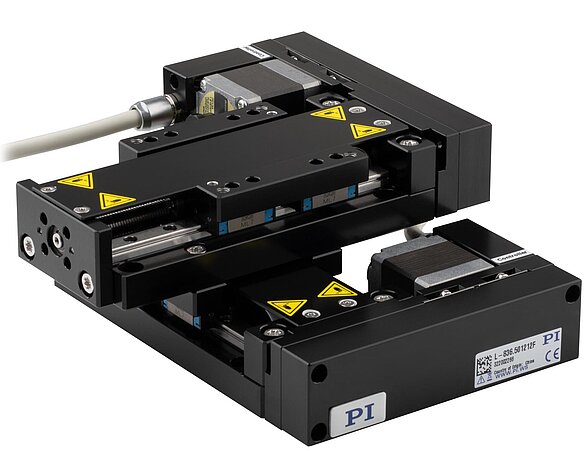
Step and settle motion is generally a slower process than continuous scanning, similar to stop and go traffic vs. free flowing traffic. This process involves acceleration, deceleration, and waiting until a stable position has been reached before an image can be captured. The higher the mechanical resonant frequency (equivalent to the stiffness of the system), the shorter the settling time. To ensure excellent in-position stability, optics-based systems often utilize a stepper motor / lead screw combination as the driving mechanism. If the stepper motor is dimensioned correctly, it can be operated in open-loop, preventing servo jitter issues that may arise in closed-loop systems. However, to verify position accuracy, a linear encoder can also be added. The combination of stepper motor and fine pitch lead screw is obviously slower than a continuous-scan, linear motor-based approach. However, this may not matter, if the majority of the cycle time is dictated by other processes.
If the motion system is the limiting factor, an ironless linear motor stage is the logical consequence. The linear motor solution allows for significantly higher acceleration and speeds of 1000mm/sec and more are feasible. Modern encoders provide resolutions below 1 nanometer, essential to achieve the required level of stability. Besides the higher motion performance of the linear motor, the absence of friction and wear as opposed to leadscrew-drives is a significant plus, also when it comes to maintenance and lifetime.
Precision motion control and automation play pivotal roles in democratizing DNA sequencing by driving down the costs. When looking for the right partner, assess the experience and expertise of each vendor. PI has a proven track record of delivering high-quality standard and custom motion systems for genome sequencing applications. Supported by the largest portfolio of precision motion technologies, customers have the choice of piezoelectric, voice-coil, and 3-phase motor drive systems and can select from a variety of guiding systems including flexures, cross-roller bearings, air bearings, and magnetic-bearings. Drawing from five+ decades of nanopositioning experience with customers in the most demanding industries, including semiconductor and super-resolution microscopy manufacturers, we have honed our expertise to deliver cutting-edge solutions that meet the highest standards of precision, reliability, and performance.
If you would like more information about our full product range for genome sequencing, simply contact a member of the PI team directly.
Blog Categories
- Aero-Space
- Air Bearing Stages, Components, Systems
- Astronomy
- Automation, Nano-Automation
- Beamline Instrumentation
- Bio-Medical
- Hexapods
- Imaging & Microscopy
- Laser Machining, Processing
- Linear Actuators
- Linear Motor, Positioning System
- Metrology
- Microscopy
- Motorized Precision Positioners
- Multi-Axis Motion
- Nanopositioning
- Photonics
- Piezo Actuators, Motors
- Piezo Mechanics
- Piezo Transducers / Sensors
- Precision Machining
- Semicon
- Software Tools
- UHV Positioning Stage
- Voice Coil Linear Actuator
- X-Ray Spectroscopy