Parallel kinematic machines (hexapods) with sub-micrometer precision and six degrees of freedom (6-DoF) are gaining traction in photonics, micro-optics, and wafer-level alignment. To meet industrial demands for reliability, precision, and high dynamics, PI developed a compact, direct-drive 6-DoF hexapod using lever-based actuators to reduce complexity, improve performance, and minimize wear. This article outlines the system design and evaluates its precision and dynamic capabilities for industrial-scale use.
PI started developing high-precision hexapod parallel kinematic machines (PKMs) in the early 1990s for the astronomy community. Later, these 6-axis micropositioning systems quickly found new applications in the photonics, semiconductors, life sciences, and optics industries.
As industrial precision alignment and multi-axis scanning demand grows, the need for compact, robust, and dynamic 6-DoF PKMs is rising[1].
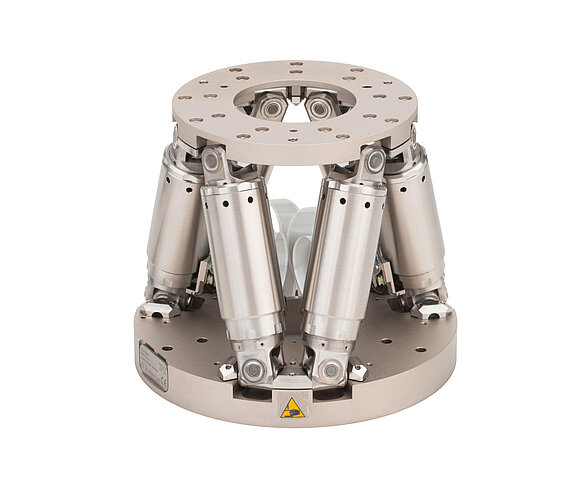
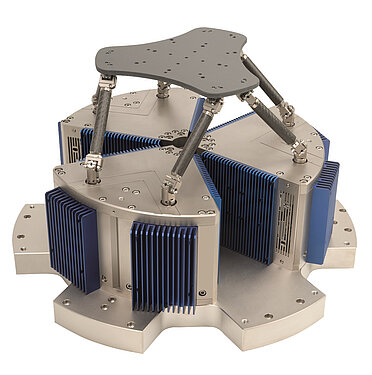
However, traditional compact, screw-driven 6-DoF PKMs are limited in performing high-frequency, high-amplitude motion. As shown by Rudolf et al.[2], these systems can also be subject to accelerated wear during small-amplitude, high-frequency operation, requiring special design solutions, such as implemented in the H-815 ruggedized hexapod to run them in 24/7 demanding industrial applications. In contrast, direct-drive PKMs offer higher accelerations and velocities with reduced mechanical wear, thanks to their simplified design.
While flexure-based systems like PI’s H-860[2] or the T-Flex hexapod[3] offer excellent precision, their size and workspace limitations make them less suitable for industrial production lines. To address this, PI has developed a compact, direct-drive 6-DoF PKM comparable in size to existing screw-driven hexapods, combining high dynamics with precision to support increased throughput and reduced downtime in industrial environments.
Lever Hexapod Design
The newly developed lever-actuated 6‑DoF positioning system (see Figure 3) employs a parallel-kinematic design[4]. It comprises six identical actuators arranged between a fixed base platform and a movable top platform. This configuration enables the top platform to perform precise lateral and rotational motions along all six axes: X, Y, Z, pitch, roll, and yaw.
The system’s actuators are integrated into the base platform and consist of brushless DC (BLDC) motors with ceramic bearings, each fitted with a lever attached to the motor shaft. This design eliminates moving sensor- or power cables, preventing parasitic forces from degrading system performance. Each lever connects to the top platform via passive struts offering five degrees of freedom — enabled by two universal joints and one rotational joint. Rotating a lever moves the strut’s lower endpoint along a circular path, thereby driving the motion of the top platform. Lever position is measured using a scale mounted opposite the lever (Figures 4a & 4b).
To counteract the weight of the top platform and struts in the neutral position, counterweights are mounted on the levers. The universal joints were newly developed for this model. They must be compact, lightweight, backlash-free, and capable of large angular travel. While ball joints allow high angular motion in a compact form, their friction and hysteresis make them unsuitable for precision applications. Flexure joints, though free of hysteresis, offer limited angular range. To overcome these trade-offs, a sub-compact cardanic joint with crossed axes and four ball bearings was developed (Figure 4), providing backlash-free performance and large angular motion. In addition to the universal joints, each passive strut includes a high-precision rotational bearing, allowing rotation about its longitudinal axis.
Lever Hexapod Specifications
The passive strut and lever lengths were carefully selected to match the workspace of PI’s screw-driven H‑811 hexapod. As shown in Table 1, the functional model delivers slightly reduced X/Y travel, increased Z travel, identical rotations around X/Y, but approximately half the Z-axis rotation. Despite a lower payload due to the absence of drive-screws, it supports many photonics alignment tasks, achieving peak speeds of ~65 mm/s with counterweights — more than 3 times faster than the H‑811’s 20 mm/s. A summary of system specifications is provided in Table 1.
The hexapod’s theoretical resolution depends on the lever position (with pure Z-motion extremes detailed in Table 1); however, along the sensor scale it consistently achieves about 20 nm precision.
Performance Measurements
Resolution (defined here as the minimal incremental motion (MIM) reliably executed in closed-loop operation) was determined using a ten-step sequence of varying step widths around the starting position. The worst-case resolution occurs near the initial position. Figure 5 illustrates 50 nm steps in the Z-direction, measured via interferometry; similar tests showed comparable behavior in X and Y. The steps are clearly visible, although sensor or control-loop noise in this prototype are present when idle. Overall, the system achieves a MIM of <100 nm in all directions.
A frequency analysis was conducted to compare the new direct-drive hexapod with PI’s compact ball-screw H‑811 standard model (an ultra-high resolution H-811 variant has achieved 3nm position stability in interferometer tests). Figure 6 displays amplitude error and phase offset for various amplitudes (1–20 µm) and frequencies (5–30 Hz). The direct-drive model (left) exhibits significantly lower amplitude error and phase offset than the H‑811 (right).
Conclusion & Outlook
The lever hexapod 6‑DoF PKM prototype demonstrates impressive performance in fast, small-amplitude motions — ideal for alignment tasks. Future work will include lifetime testing to verify robustness and implementing MIMO control to fully exploit the system’s potential.
References
[1] Sander C et al. 2018 Development of High-Precision Parallel Kinematics for Industrial Automation and Silicon Photonics, Proceedings of the 18th International conference of the European Society for Precision Engineering and Nanotechnology (euspen).
[2] Rudolf C et al. 2015 Direct Driven Hexapods for Highly Dynamic 6DoF Applications, Proceedings of the 15th International conference of the European Society for Precision Engineering and Nanotechnology (euspen).
[3] Naves M et al. 2020 T-Flex: A large range of motion fully flexurebased 6-DOF hexapod, Proceedings of the 20th International conference of the European Society for Precision Engineering and Nanotechnology (euspen).
[4] Volz T. et al. 2024 Compact lever actuated direct driven 6-DoF parallel kinematic positioning system. Proceedings of the 24th International conference of the European Society for Precision Engineering and Nanotechnology (euspen).
Blog Categories
- Aero-Space
- Air Bearing Stages, Components, Systems
- Astronomy
- Automation, Nano-Automation
- Beamline Instrumentation
- Bio-Medical
- Hexapods
- Imaging & Microscopy
- Laser Machining, Processing
- Linear Actuators
- Linear Motor, Positioning System
- Metrology
- Microscopy
- Motorized Precision Positioners
- Multi-Axis Motion
- Nanopositioning
- Photonics
- Piezo Actuators, Motors
- Piezo Mechanics
- Piezo Transducers / Sensors
- Precision Machining
- Semicon
- Software Tools
- UHV Positioning Stage
- Voice Coil Linear Actuator
- X-Ray Spectroscopy