Tilt Stages, Tip-Tilt Stages, High Precision - Motorized and Piezo-Driven
High Performance and High-Speed Tilt Stages and Tip-Tilt Platforms for Alignment and Stabilization
PI provides a large selection of high precision and high-speed tilt and tip tilt stages with a variety of different drive concepts. Air bearings tilt stages provide high speed motion, large travel ranges, support high loads, and are completely wear-free and maintenance free. Piezo flexure amplified tilt and tip tilt platforms can be used for fast laser beam steering, image stabilization, and improvement of laser welding applications. Their high resolution down to the nanoradian and fast response in the millisecond range makes them ideal for free space optical communication and error compensation in beam delivery applications, e.g. in the semiconductor industry.
Voice coil tip / tilt platforms provide larger angular travel than piezo flexure units, but at slightly lower resolution.
Applications of PI tilt stages and Z-tip/tilt platforms and goniometric rotation stages are found in alignment, laser beam steering, optics, and wafer test and inspection.
The A-523 high performance Z-tip-tilt stage is based on fast linear motors and frictionless air bearing guiding systems. It provides nanometer resolution, high speed, and a high load capacity of 8kg. The A-651 spherical air bearing achieves tip and tilt motion up to +/-45 degrees and 360 degrees rotation around Z. The A-60x add-on stage for rotary stages provides manual tip/tilt motion along with a fine adjustment range X and Y for high precision alignment tasks.
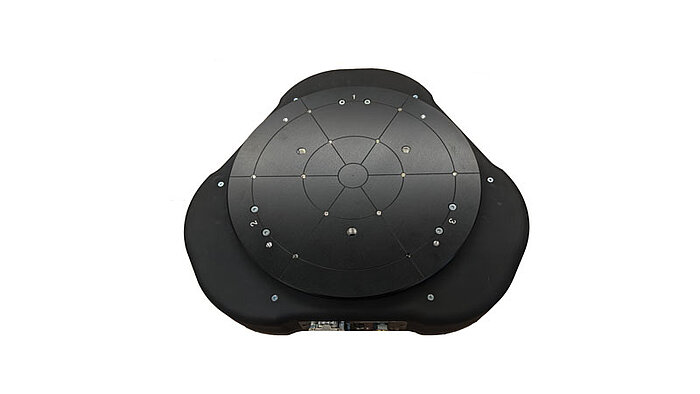
A-523 Z-Tip-Tilt Air Bearing Stage
Low Profile
- ⌀250mm table
- 8 kg load capacity
- 5mm Z-stroke, to 2° tip/tilt
- 10nm/0.06µrad incremental motion
- 1nm sensor resolution
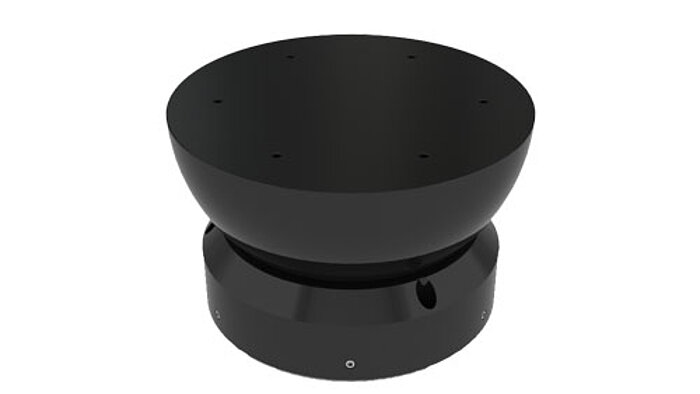
A-651 - A-657 Spherical Air Bearings
3 Degrees of Freedom
- Ideal for zero gravity simulation
- 2/3/4/6/8/10/12” sphere diameter
- 15 to 635kg load
- ±45 degrees rotation range
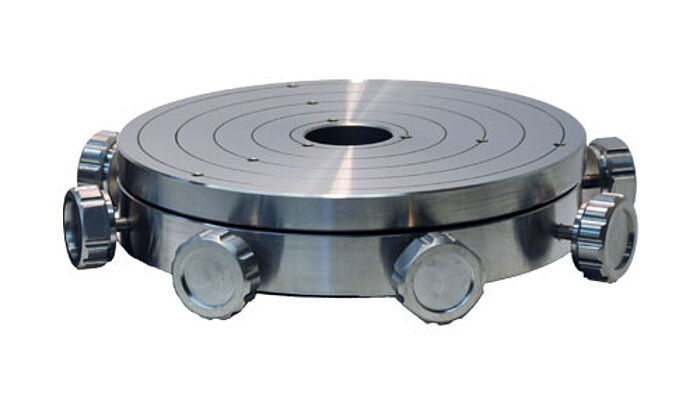
A-60x.MTT Manual X-Y-Tilt Platform
Add-On For Rotary Stage
- Ideal for optics testing
- 4 degrees of freedom: X, Y, θX, θY
- Manual operation
- Travel to ±3mm, ±1.25°
- 3/4/6/8/10” table diameter
- Direct mount on A-60x / A-62x
These closed-loop nanopositioning Z and tip-tilt stages provide nanoradian and sub-nanometer resolution with very fast response for high performance alignment, scanning, and steering applications. Based on extremely precise, friction and maintenance-free flexure guides, they are driven by piezoelectric elements and provided with position feedback sensors for high performance motion control.
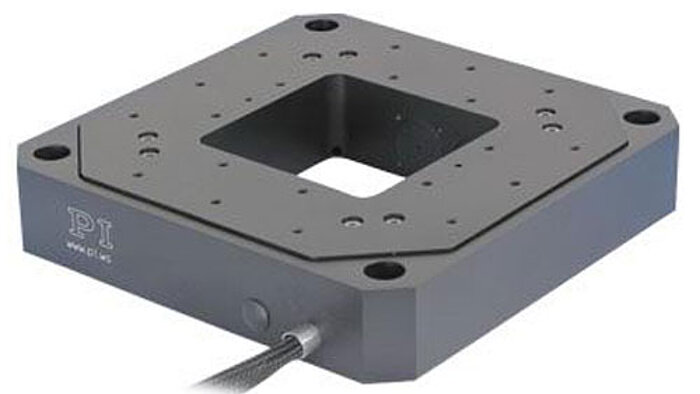
P-528 Piezo-Z & Z/Tip/Tilt Stages
Parallel Metrology
- 50, 100, 200µm Z-motion
- Up to 4 milliradian Z/tip/tilt
- Precision trajectory control
- Sub-nanometer resolution
- Parallel capacitive metrology
These tip-tilt platforms are designed for laser beam steering, fast scanning, image stabilization or free space optical communication. Bandwidth of more than 1kHz are feasible. In addition to high speed, they also provide very high stability and repeatability down to the nanoradian range. In addition to these standard units, custom tip-tilt mirror platforms for image stabilization in astronomical telescopes are also available from PI.
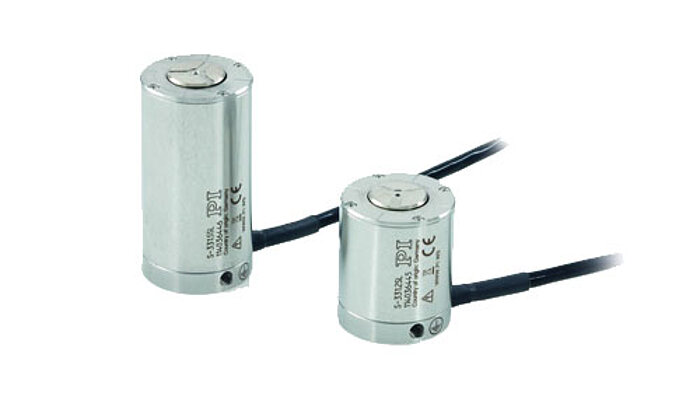
S-331 Tip/Tilt Mirror Platform
High Dynamics, for ½” Mirrors
- 10mrad optical deflection
- High dynamics: 0.8msec rise time
- PKM: single pivot point
- Closed-loop for high linearity
- Up to 50nrad resolution
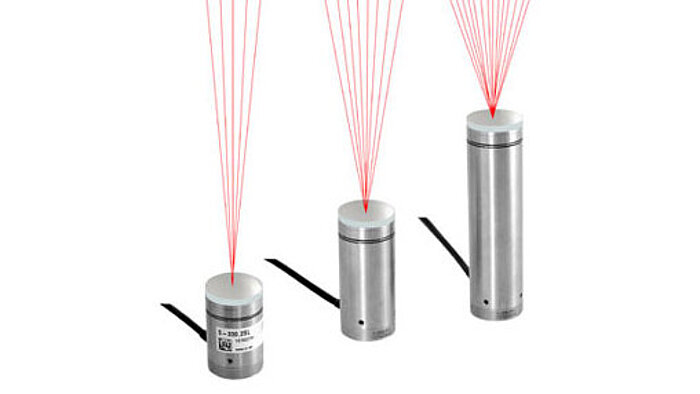
S-330 Fast Tip/Tilt Steering Mirror
Mirrors up to 50mm
- Fixed orthogonal axes with a common pivot point
- To 20mrad optical beam deflection
- Up to 20nrad resolution
- Closed-loop for high linearity
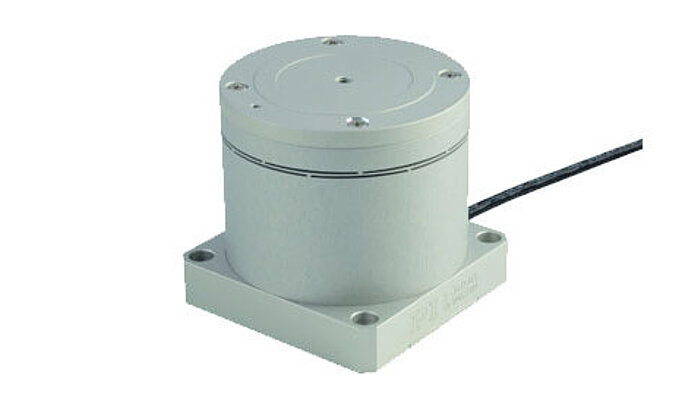
S-340 Fast Tip/Tilt Steering Mirror
Mirrors up to 100mm
- Fixed orthogonal axes with a common pivot point
- 4mrad optical beam deflection
- Sub-microrad resolution
- Closed-loop for high linearity
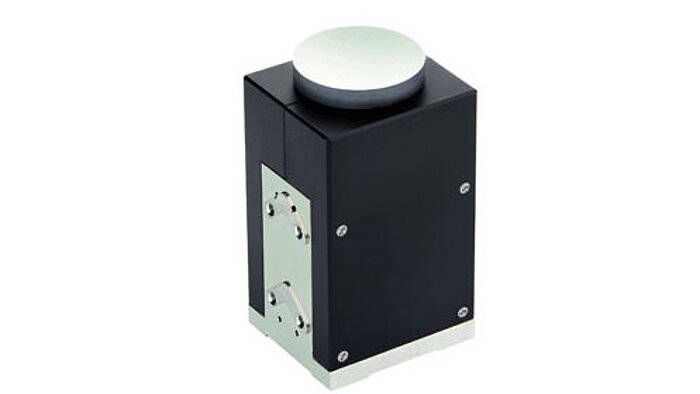
S-335 Tip/Tilt Mirror Platform
Long Travel, Mirrors up 1”
- 70mrad optical beam deflection
- Up to 100nrad resolution
- Closed-loop for high linearity
- PKM = Equal dynamics for both axes
- ID chip for auto calibrate
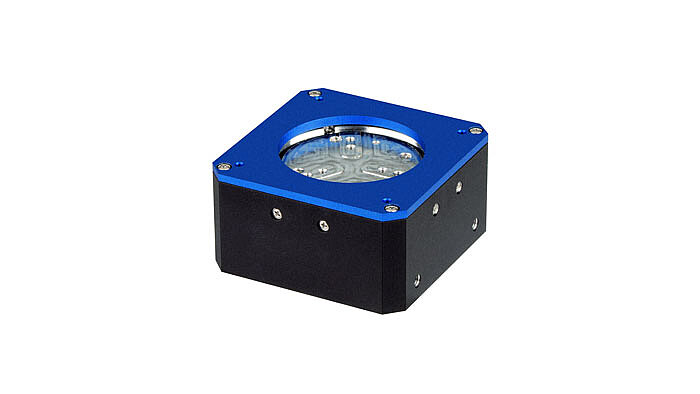
V-931 Fast Steering Mirror Platform
Voice-Coil Driven, Mirrors to 1”
- 140mrad (8°) optical deflection
- <1 µrad resolution
- Closed-loop voice coil drives
- PKM = Equal dynamics for both axes
- 20msec step response
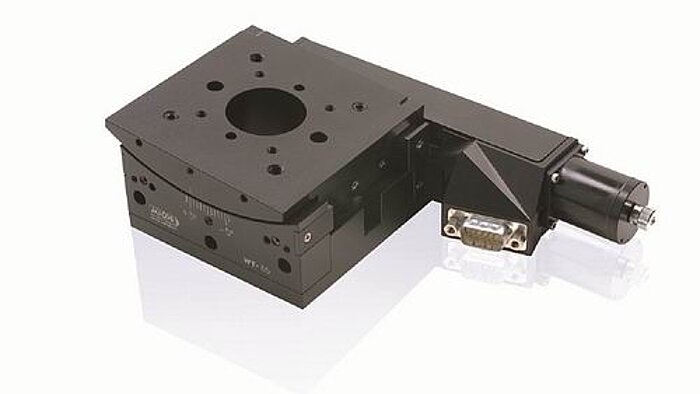
WT-85 Motorized Precision Goniometer
Aperture, Servo / Stepper
- 10° rotation range
- 2 - 17.5µrad min. inc. motion
- 7 - 15°/sec max. velocity
- 2kg load
- 30mm aperture
- Direct encoder option
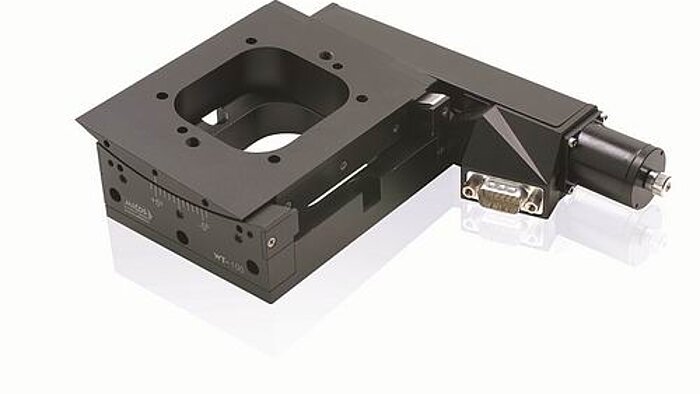
WT-100 Motorized Precision Goniometer
Aperture, Servo / Stepper
- 10° rotation range
- 8.7 - 17µrad min. inc. motion
- 7-15°/sec max. velocity
- 2kg load
- 50mm aperture
- Direct encoder option