Considering Different Technologies & Options for Multi-Axis Positioning Stages / Multi-Axis Positioning Systems
Multi-Axis Positioning Systems are essential for test, metrology, and manufacturing in many high-tech industries. PI designs and manufactures multi-axis positioners based on 3-phase linear motors, torque motors, piezo motors, voice-coil motors, servo and stepper stages in both serial-kinematics and parallel kinematics (Stewart platform) configurations. Serial kinematics multi-axis positioning systems consist of a combination of individual linear slides, XY-stages, rotary tables, and goniometric stages, while parallel kinematics positioners are integrated and cannot be separated into individual axes.
The following is an overview of standard and custom multi-axis positioners available from PI.
There are many ways to achieve multi-axis motion - let’s start with the example below. Shown are two fundamentally different 6-axis micro-positioning systems with travel ranges up to 100mm and sub-micrometer resolution that can achieve similar performance: the one on the left is a 6-DOF Stewart Platform (often called Hexapod). With hexapods – due to the parallel-kinematic principle – all 6 actuators are always involved in every move, no matter if it concerns just one single axis or all 6 axes. In contrast, the system on the right is based on a stack of individual single-axis stages (serial kinematics) that can all be operated independently of one another. While both systems can provide similar motion performance, the Hexapod design has a number of advantages, such as large central aperture, higher stiffness, lower mass, no need for complex cable management and a user-programmable pivot point. On the other hand, the stacked, modular approach provides greater flexibility, for example by swapping out a 100mm motion linear stage for a unit with 200mm or 300mm to extend the planar or vertical travel range. Also, a traditional rotation stage can provide a larger rotary travel range in theta Z, compared to the parallel kinematic design. More examples on serial kinematics are shown further below. More infomraiton on parallel-kinematic motion systems is available in this Hexapod FAQ article.
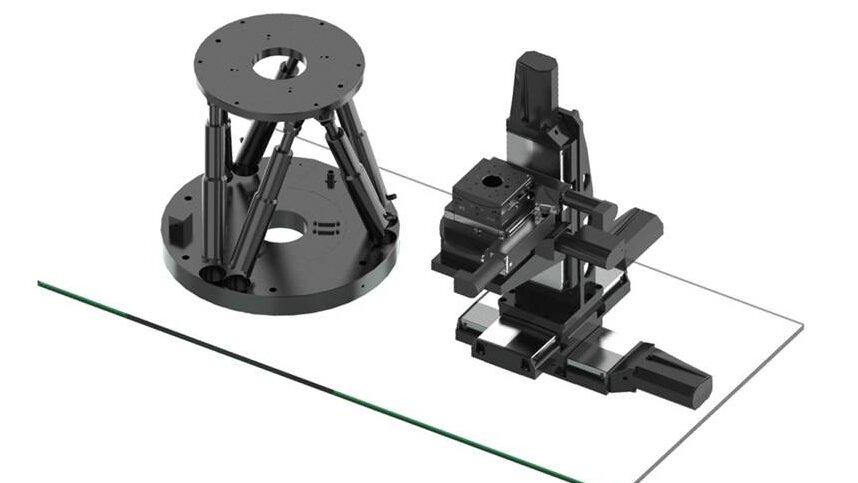
Custom-tuned multi-axis positioning systems provide significantly higher performance compared to simply stacking individual axes without performing metrology tests, error corrections, and specific servo controller tuning procedures.
Learn more about Custom-Tuned XY and XYZ Multi-Axis Positioning Systems
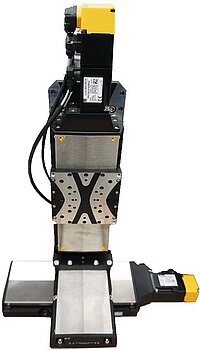
These integrated multi-axis positioners are available with a granite base for extra high precision and stability. These XYZ positioners are designed for industrial motion control applications with high demands on dynamics and precision. Easily configurable, they come with an ACS-based high-performance multi-axis motion controller with EtherCat® connectivity.
Learn more about the X-417 Integrated, Configurable, Multi-Axis Granite Positioning System
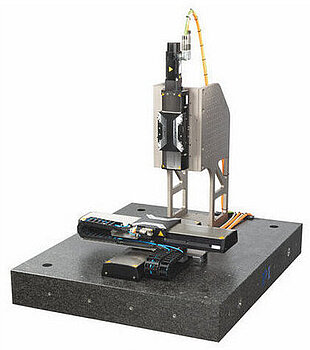
Gantry multi-axis positioning systems (gantry stages) combine several linear axes to provide XY and XYZ-motion. Gantry positioning systems are also called linear robots. Gantry systems are often used for pick-and-place applications, laser machining or even 3D-additive manufacturing. PI designs multi-axis gantry systems, with high-speed direct drive linear motors, available with both mechanical bearings and air bearings.
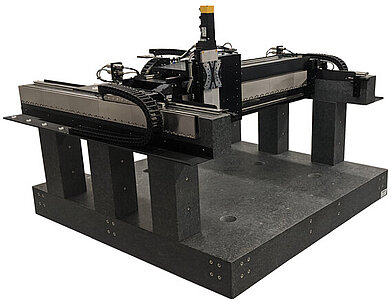
Split-bridge multi-axis positioners are usually less complex than a traditional gantry system because synchronization of the two lower linear axes (as in a gantry system) is not required. Either an XY stage is used on the bottom with a Z stage mounted on a fixed bridge, or the X and Y positioners can be split, with the Y axis on the bottom and the X-axis mounted on the fixed bridge. A vertical Z-axis stage can also be added to the X-axis for 3-axis motion.
Learn more about Granite Split-Bridge Multi-Axis Positioning Systems
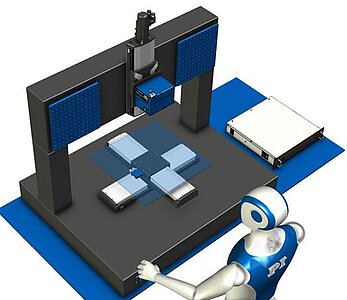
Motorized XY-tables are very common for laser machining, semiconductor wafer positioning, and test and metrology applications. PI manufactures a large variety of high precision 2-axis positioning systems, from miniature XY-tables to large, granite-based air bearing XY-tables.
Learn more about Granite Split-Bridge Multi-Axis Positioning Systems
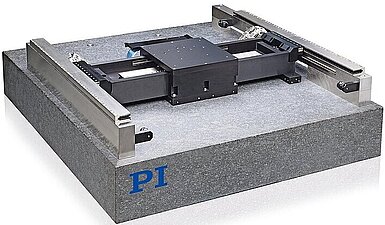
The majority of our motorized linear stages, rotary stages, and vertical linear stages can be configured and assembled into flexible XY, XYZ, and XYZ-Theta multi-axis motion systems. Vertical motion can either be achieved by vertical lift stages, providing 360 degree accessibility, or by mounting a linear stage with a bracket in a vertical orientation.
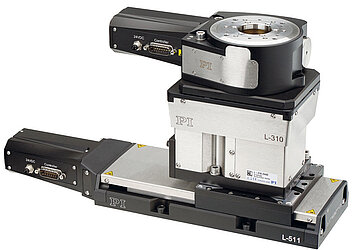
PI designs and manufactures a large selection of miniature linear stages and miniature rotary tables that can be combined into miniature multi-axis precision positioners for high precision motion applications where space is limited. The L-505 high precision miniature XYZ linear stage can also be combined with a high-speed XYZ miniature piezo scanner, ideal for photonics alignment applications.
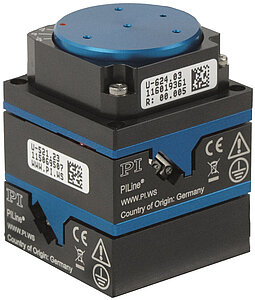
Hexapods (Stewart Platforms) provide 6-axis motion based on a parallel kinematics arrangement of 6 actuators mounted between a fixed base plate and moving top platform. Hexapod multi-axis positioners provide several advantages over serial kinematics stacked multi-axis stages, including lower inertia, improved dynamics, smaller package size, and higher stiffness. PI hexapod multi-axis stages come in many different sizes and load capacities for applications including photonics alignment, optical metrology, robotics, assembly, and astronomy.
Learn more about Stewart Platform Multi-Axis Positioning Stages
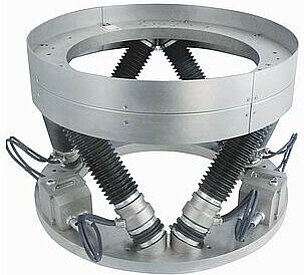
Piezoelectric positioning systems provide ultra-high precision with sub-nanometer resolution and accuracy. Piezoelectric positioners are available in single-axis stage, dual-axis, and 3-axis stage configurations, but 6-axis nano positioning stages are also available.
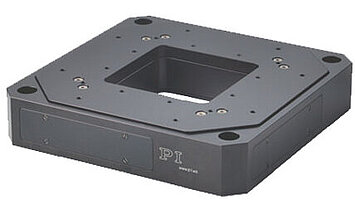
PI provides customized, engineered multi-axis precision positioning systems for high-performance and high precision automation applications. These custom positioning systems are based on our in-house engineered linear stages and rotary positioning tables and paired with our ACS-based high-performance multi-axis motion controllers to provide the best possible “motion engines” for positioning and automation applications in our customers’ OEM solutions or production processes.
Learn more about Custom Engineered Multi-Axis Positioning Systems

High-performance multi-axis motion controllers are a key requirement for achieving the maximum performance from a multi-axis positioner. PI’s new generation of ACS-based multi-axis motor controllers is available with up to 8-axis, in standard configuration, and EtherCat® connectivity makes it easy to extend the capacity up to 64 axes.
Learn more about Multi-Axis Motion Controllers with EtherCat® Connectivity
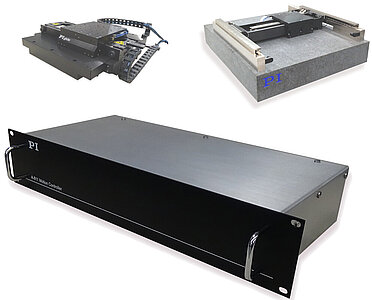