Micropositioning refers to the precise control and movement of objects over extremely small distances — typically in the micrometer (µm) or nanometer (nm) range. Micropositioning is essential many high-tech industrial manufacturing, alignment, validation, test & metrology processes and requires hihgly precise motorized positioning stages. PI offers the broadest and deepest portfolio of precision motion technologies for micrometer level and nanometer level precision applications. Our engineers work with our customers to find the best drive and bearing technology for each individual application. Having access to multiple drive and positioning technologies allows an open discussion with a better outcome for the customer.
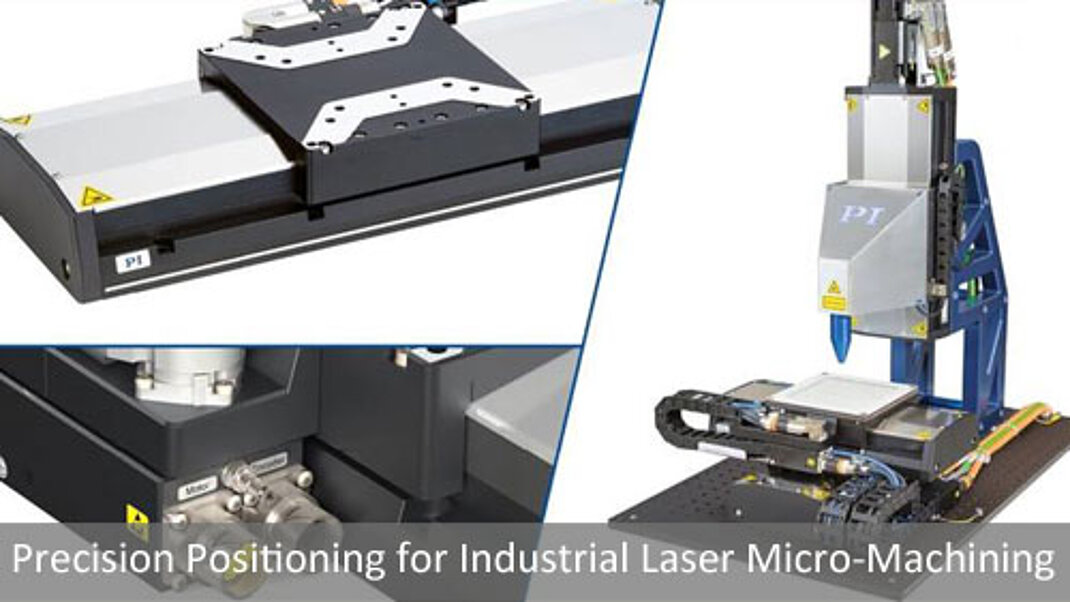
Micropositioning Terms and Choices
Precision Motor/Screw Drives with Mechanical Bearings
PI‘s range of traditional precision motorized stages covers travel ranges from 5mm to 1000mm. Stages with servo and stepper motors guided by ball bearings and cross roller bearings for higher precision are offered.
High Precision Linear Motor / Torque Motor Direct Drives with Mechanical Bearings
For higher precision requirements and fast precision automation applications, frictionless 3-phase direct-drive linear and torque rotary motors are used. Integrated optical scale encoders provide sub-nanometer resolution. Linear motors are non-contact and can provide extreme lifetime with fast acceleration and high velocities. Our highest performance motorized linear translation stages can achieve sub-nanometer resolution.
Ultra-High Precision Stage Applications: Air Bearing Stages
Air bearing stages with linear motors are completely free of friction and wear. They provide the highest performance with extremely good repeatability, straightness, and flatness. These frictionless positioners are used in metrology and positioning applications with the highest demands on lifetime and accuracy.
6-Axis Parallel Kinematics Stages (Hexapods)
As the world leader in parallel kinematics six-axis hexapod precision positioning systems, our engineers can find the appropriate technology for almost any complex motion and positioning application for industrial, OEM, and scientific applications.
Engineered Motion Sub-Systems
Multi-axis positioning systems with controller and software
Piezo Motor Drives
In addition to traditional electromagnetic motors, PI also offers a number of piezo motor drive systems for special applications. Piezo motors are intrinsically self-clamping, non-magnetic, very compact, and provide nanometer resolution along with very fast response.
Vacuum Environments
Our new line of motorized linear stages with ball bearings and crossed roller bearings is also available for vacuum and UHV environments and can be customized for beam line integration.
Benefits of Working with PI
Access to the most advanced motion technologies: choice of drives (several types of self-clamping piezo linear motors); magnetic linear motors; electro-magnetic linear motors; hybrid linear drives; DC-servo and steppers
World Class Industrial Motion Controllers
From compact single axis units to advanced multi-axis ACS controllers with Ethercat® interface
Applications where high precision micropositioning stages are essential for:
- Semiconductor Test and Manufacturing: For the accurate placement of wafers and components during processes like lithography, inspection, and assembly.
- Optics and Photonics: For the alignment and positioning of optical fibers, components, lenses, mirrors, and detectors in test and manufacturing.
- Laser Processing: For precise control of laser beams and samples in applications such as cutting, engraving, welding, and micromachining.
- Microscopy: For high-resolution imaging and precise sample positioning in techniques such as super-resolution microscopy, confocal microscopy, and atomic force microscopy.
- Metrology: For accurate measurement and inspection of components and surfaces in coordinate measuring machines (CMMs) and other precision instruments.
- Medical and Biotech: For precise manipulation and positioning of samples, cells, and tissues in applications such as cell sorting, DNA sequencing, and automated drug testing.
- Aerospace and Defense: For the accurate assembly and inspection of components, as well as for simulation and testing of optical and electronic systems.
- Nanotechnology: For the manipulation and positioning of nanomaterials and devices in research and manufacturing.
- Automated Test Equipment (ATE): For precise positioning of probes and test heads in the testing of electronic devices and circuits.
- Robotics: For accurate movement and placement of robotic arms and end effectors in industrial automation and research applications.
Precision positioning stages provide the accuracy, repeatability, and stability needed for these and other high-precision applications.