“Micropositioning” – Classical Precision Positioning Technologies still Going Strong
Striking the right balance between affordability, accuracy, and reliability
Traditional linear and rotary “micropositioning” stages are based on servo and stepper motor-driven leadcrews and ballscrews and mechanical bearings. They are classical components for precision motion control applications, spanning from lab-automation to industrial assembly and inspection. “Micropositioning” got its name from precision levels in the micrometer realm – but yesterday’s micropositioners can provide resolution down to the 0.01 micrometer range today. Precision gains are increasingly important for positioning of measuring tools, processing tools, cameras or objects to be processed.
The products high-lighted here were developed to move loads of 10kg to 50kg (22lb to 110lb) over distances up to 300mm. Rotation stages provide rotation angles of 360 degrees. Achieving accuracy in the micron and sub-micron realm is not a trivial matter – and while not being known as exotic in terms of technologies used, these types of products are far from being classified as commodities.
When you consider the precision demands on the individual components from bearings to position feedback sensors, along with the skill and precision required during assembly and testing, it becomes an ambitious undertaking to keep the costs in check.
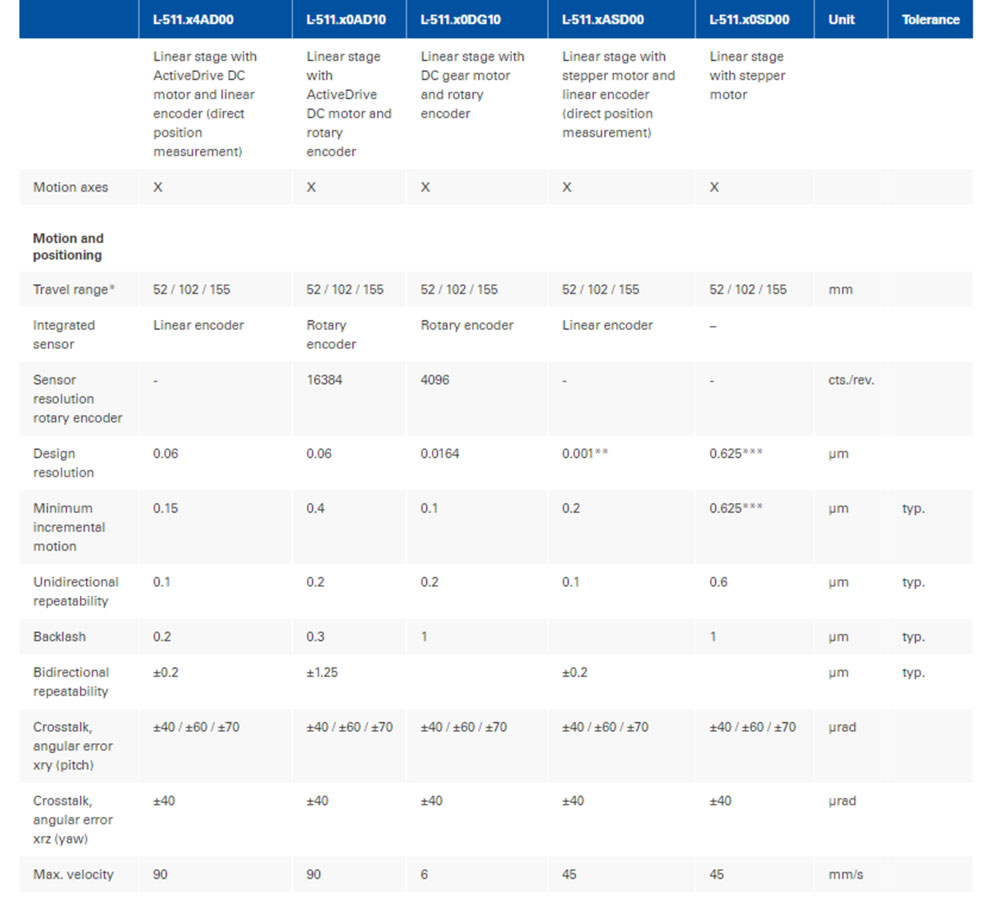
The balance of all components is important – the weakest component limits the precision. If the contact surface of the guides is not level, the most expensive positioning sensor will not live up to its rated accuracy. If the preload between the nut and the drive screw is not set right, backlash may increase or wear will become an issue over time.
Over the last 4 decades, engineers at PI have mastered to balance cost, precision and reliability of their micropositioning product lines. Depending on the application and requirements, engineers pick from recirculating ball bearings, crossed roller guides, and linear bearings to ensure high load capacity and positioning accuracy. Direct metrology encoders monitoring the moving platform provide higher accuracy, while motor shaft mounted encoders are more cost efficient. PI engineers have access to encoders providing resolutions of 1 nanometer and below, along with sub-micrometer absolute accuracy when used with controller-based error mapping algorithms.
Micropositioning and Nanopositioning Technologies
To achieve real nanopositioning precision, a different approach is required. Here, friction has to be eliminated first. There are several ways to achieve this. Frictionless flexure guides with piezoelectric direct drives, or air bearings to replace mechanical bearings, linear motors or voice coils to replace mechanical screw drives take the system precision to a new level – especially when it comes to dynamic performance. Without friction wear is significantly reduced, as is particle generation, noise and other side effects of mechanical bearings and drive train components.
Then there are solutions that reside in the middle, such as PI’s Q-motion piezo-inertia driven positioning stages. Here, a drive system with intrinsically unlimited resolution is combined with traditional mechanical bearings. Advantages are an excellent cost to performance ratio, miniaturized size, high resolution in the nanometer range along with travel ranges similar to traditional motorized positioners.
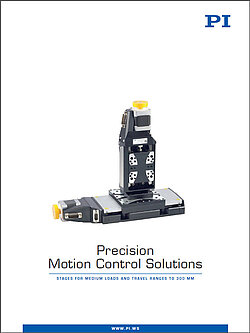
Blog Categories
- Aero-Space
- Air Bearing Stages, Components, Systems
- Astronomy
- Automation, Nano-Automation
- Beamline Instrumentation
- Bio-Medical
- Hexapods
- Imaging & Microscopy
- Laser Machining, Processing
- Linear Actuators
- Linear Motor, Positioning System
- Metrology
- Microscopy
- Motorized Precision Positioners
- Multi-Axis Motion
- Nanopositioning
- Photonics
- Piezo Actuators, Motors
- Piezo Mechanics
- Piezo Transducers / Sensors
- Precision Machining
- Semicon
- Software Tools
- UHV Positioning Stage
- Voice Coil Linear Actuator
- X-Ray Spectroscopy