Test Results: Voice-Coil Nanopositioning Stages for Two-Photon Polymerization
High precision motion control / software support for 3D maskless direct laser writing technology
Laser light has been vilified by Hollywood in many a classical movie, usually as a powerful source of destruction. In 1964, just four years after Theodore Maiman operated the first laser at the Hughes Research Laboratory in California, the James Bond movie Goldfinger already anticipated laser cutting, however not for the betterment of mankind. Later, high-powered light sources made another appearance on the silver screen, as the Dark Side tried to pulverize the Force for good with light sabers and laser cannons.
Having been predicted by physicists in the early 20th century, it wasn’t until the turn of the 21st century that the laser became a standard tool for material scientists and engineers – from cell phone screen cutting and semiconductor wafer dicing, to improving the surface properties of metals. Still, most of these laser applications revolve around separating, melting or removing materials. What if you could use a laser to literally construct objects?
Enter Two-Photon Polymerization
Putting laser beams to work for the creation of 3D objects is no longer science fiction – it is made possible through a process called laser lithography or two-photon polymerization, and it is gaining traction quickly, especially when extremely fine structures and low quantities are required.
Two-photon polymerization (TPP) is based on two-photon absorption (TPA), a third-order nonlinear optical phenomena whereby simultaneous absorption of two photons excites a molecule to a higher energy state – a process that can be exploited to selectively change the material properties of a monomer gel. While TPA was first described in the early 1930’s, it took three more decades to prove the phenomenon with the invention of the laser.
Today, TPA is often employed for micro-fabrication purposes, using highly focused coherent light to fabricate sub-diffraction limited structures via laser direct write methods. In practical applications, the advantage of two-photon absorption over one photon absorption is the third-order process, reducing the absorption cross section significantly and allowing for the production of much smaller feature sizes. Due to the high resolution of the TPP process, features as minute as 100 nanometers, and in some cases even below, can be created. This capability allows the design of extremely lightweight, yet strong structures and objects with high aspect ratios.
Micro manufacturing systems using laser lithography have become quite popular in recent years, due to the flexibility of the maskless 3D lithography method to create true 3D structures and the rise of demand in photonics, bio-technology, micro-optics, and micro-mechanics.
In 3D-TPP micro-fabrication, a photocurable resin is exposed to a highly-focused, 3D-scanned laser beam creating polymerized voxels. At the focal point, the two-photon polymerization process occurs with high spatial confinement while not affecting adjacent volumetric space, leaving structures in the cured volume while adjacent spaces are easily removed, leaving a solid 3D object.
The laser beam can either be steered by mirrors, or the resin can be mounted on a multi-axis precision positioning stage and moved relative to the stationary beam. A combination of both methods is also possible.
In either technique, the uniformity of the resulting micro-structure is dependent on spatial positioning tolerances. Because of the nonlinear nature of the photopolymerization process and the very slow scan speeds required for TPP, the precision at which the velocity can be controlled to deliver uniform dose is especially critical. Since we are looking at a 3D process, this also means coordinating motion between multiple nanopositioning stages (or scanner axes) very precisely to deliver the required multi-axis trajectories.
Controlling Motion and Velocity in the Nanometer Range
In this article, we are looking at the motion performance of a compact, voice-coil-driven nanopositioning stage and a software package that allows users to quickly transfer 3D data into a multi-axis motion path for two-photon polymerization laser lithograpy.
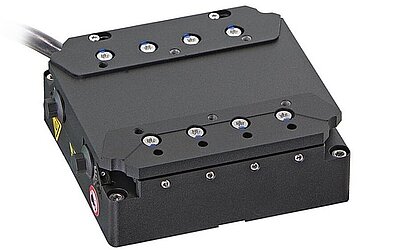
Given the high requirements on positional resolution, we first determined the steady stage position noise of the XY stage. The stage was controlled with A-814 Series 4-Axis Motion Controller, using ACS UDMnt Drives, and mounted using three point supports on a honeycomb TMC breadboard placed on an a desk in an office/lab environment on first floor with an adjacent roadway and a standard A/C running.
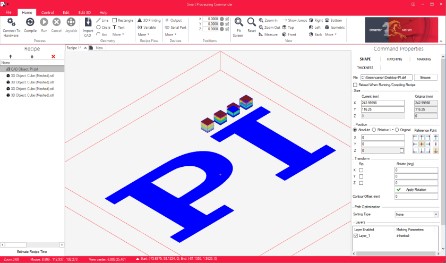
The baseline in-position stability data were sampled at 100 Hz over 5 seconds, using the integrated high precision PIone linear encoders on both axes (~30 picometer resolution limit).
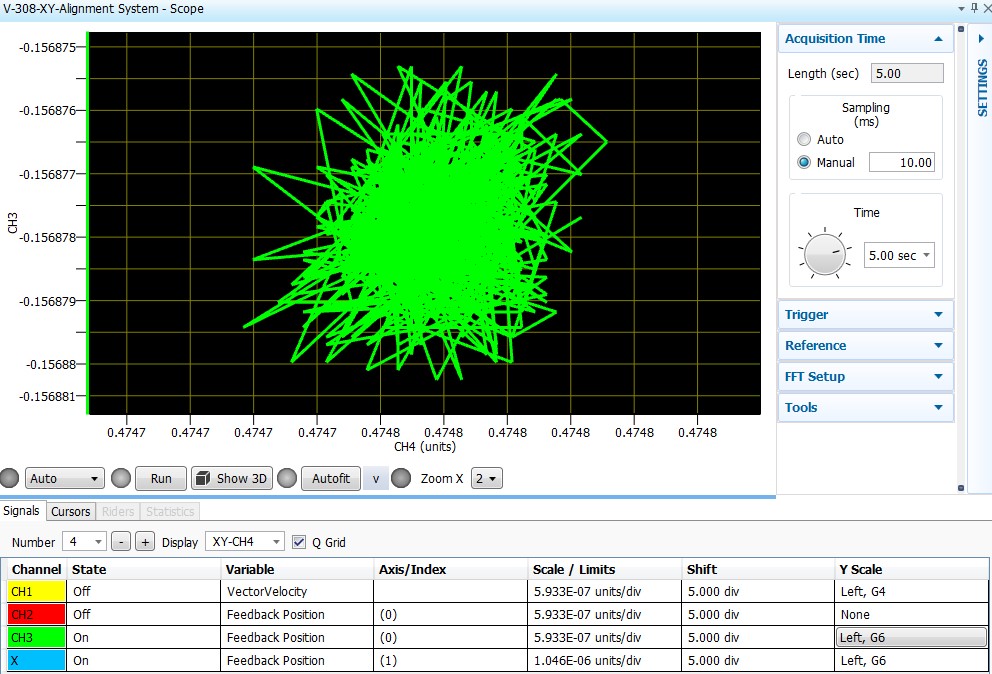
Dynamic Performance, Velocity Stability, and Position Error on XY Coordinated Motion for TPP Processes
A) 5µm rectangular polymerization process path
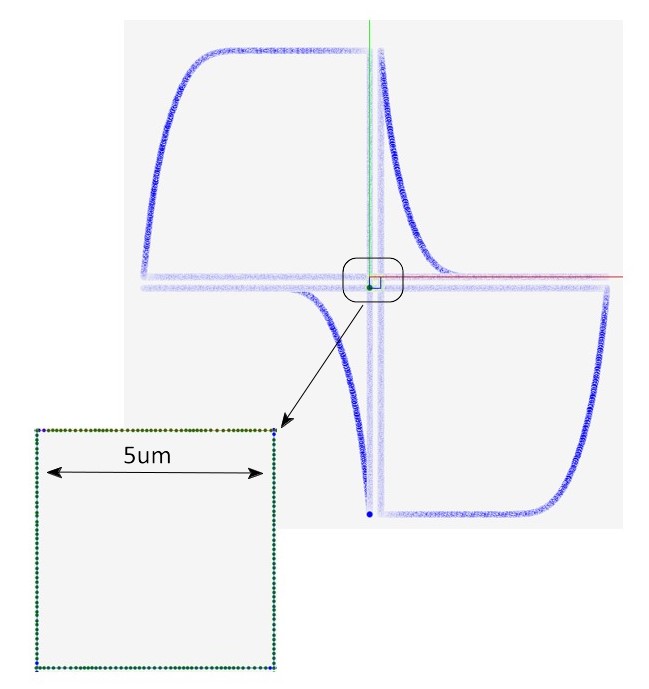
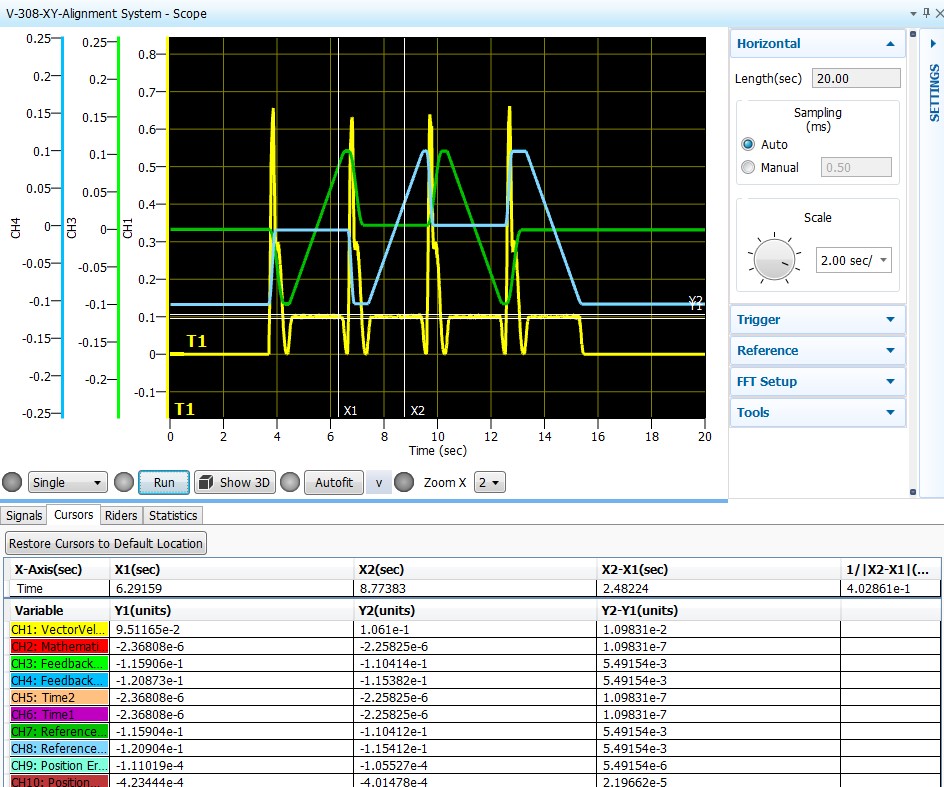
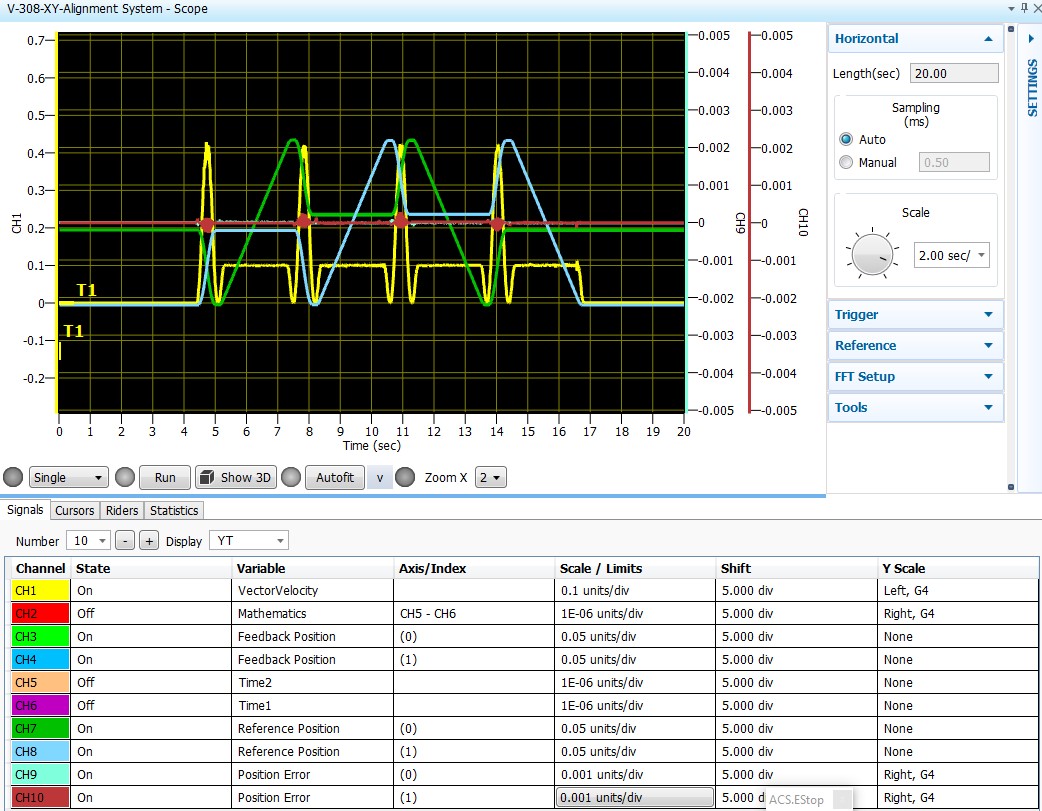
Just as with the 5µm rectangle, the position error was measured to be ~±35nm for both the X and Y axis. The velocity rate variation was observed at ~100 µm/s ±4%.
C) 100µm rectangular polymerization process path and curvilinear coordinated polymerization process path
Lastly, tests with a 100µm rectangle and a curvilinear path were conducted.
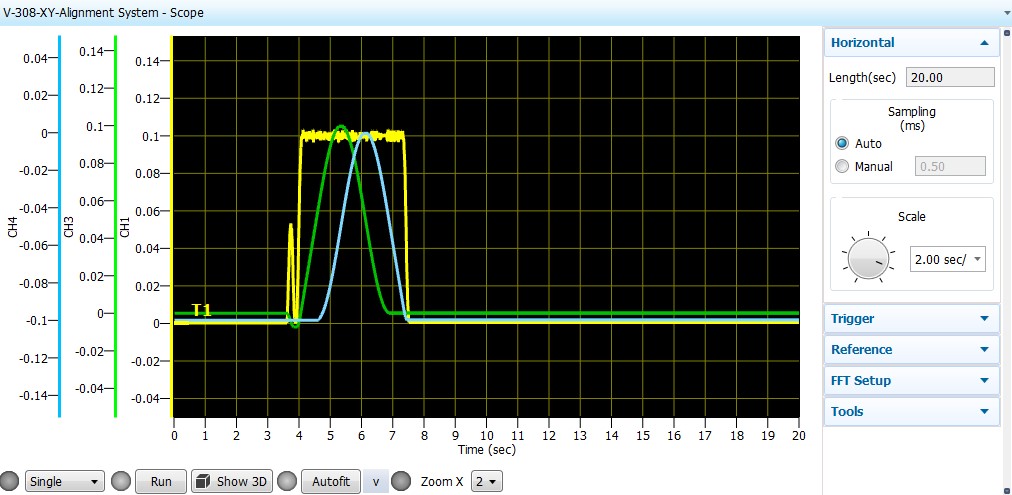
Summary – Synchronized Low Speed Performance of Voice-Coil Nanopositioning Scanners for 2PP
The goal of this test was to verify if the very low constant path speeds required for high quality results in two-photon polymerization could be achieved by the V-308 voice-coil-driven linear stage. As shown above, the results indicate excellent motion performance with constant vector velocity across all tested paths.
Position errors during active scanning were observed at sub-100 nanometer levels, significantly surpassing the requirements for good TPP results, despite the operating environment and mounting surface for the XY-scanning stage were less than ideal, limiting achievable performance (a lapped granite interface was not available at time of test).
The high motion performance was contributed in part to the employed PIOne encoder technology, providing sub-nm interpolated resolution.
Additional steps could be taken to further improve the results, if so desired
a) PI’s PILOT algorithm has shown to enhance performance in other critical nanopositioning applications.
b) Running NanoPWM drivers can reduce noise
c) As mentioned above, mounting the stages on a lapped granite interface will also have a positive effect on precision.
Overall, the tests prove the V-308 voice-coil-driven XY-table combination is a very capable, low cost solution to TPP over short travel ranges.
When Higher Precision and Longer Travel is Required
Planar air bearing XY-tables provide the highest performance when it comes to smootheness of motion, velocity constancy, straightness, flatness, and yaw control. An example, the compact A-311 XY-table is shown below. Detailed performance data is available in this article.
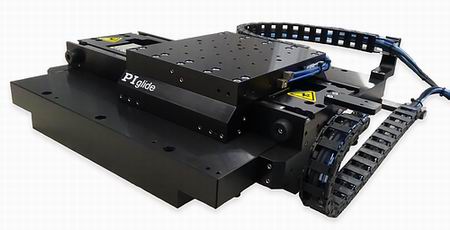
Integrated Flexure Guide Piezo XY and XYZ Tables
For short travel ranges below 1mm, piezoelectric XY and XYZ flexure tables are available. These types of ultra-precision nanopositioning stages provide the highest dynamics with planarity in the single digit nanometer range.
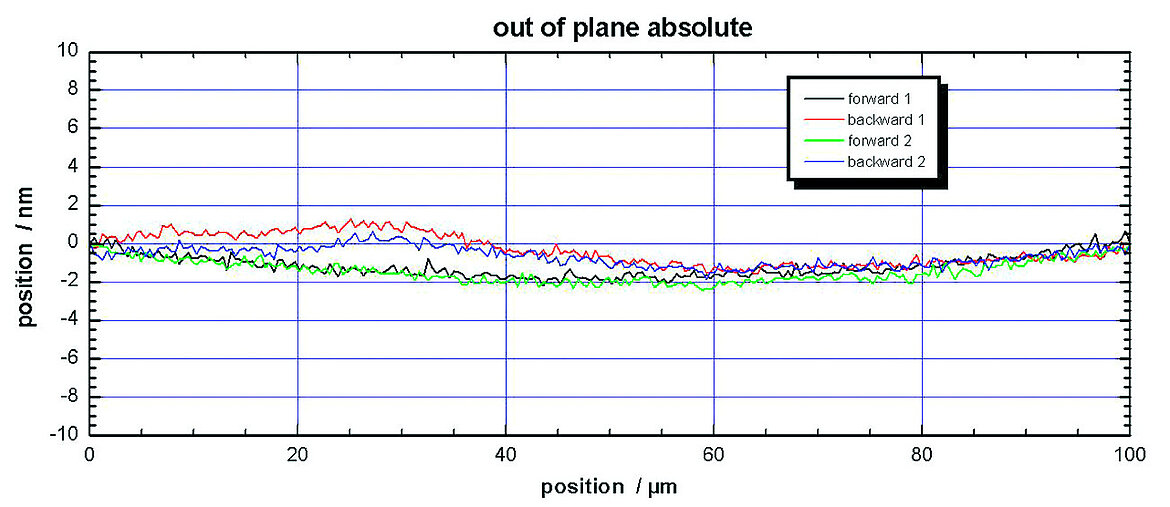
A very compact piezo nanopositioning XYZ stage, model P-611.3SF, featuring 100x100x100µm travel and 0.2nm resolution, has also been employed in Two-Photon Photopolymerization for the Fabrication of Complex-Shaped Particles and Structures in research at the University of Colorado.
Blog Categories
- Aero-Space
- Air Bearing Stages, Components, Systems
- Astronomy
- Automation, Nano-Automation
- Beamline Instrumentation
- Bio-Medical
- Hexapods
- Imaging & Microscopy
- Laser Machining, Processing
- Linear Actuators
- Linear Motor, Positioning System
- Metrology
- Microscopy
- Motorized Precision Positioners
- Multi-Axis Motion
- Nanopositioning
- Photonics
- Piezo Actuators, Motors
- Piezo Mechanics
- Piezo Transducers / Sensors
- Precision Machining
- Semicon
- Software Tools
- UHV Positioning Stage
- Voice Coil Linear Actuator
- X-Ray Spectroscopy