How to Integrate Laser Control and Motion Control to Achieve More with Less
Better solutions for system integrators to design and build advanced laser processing systems
Introduction
Ultrafast lasers are becoming increasingly accessible to researchers, system integrators, and OEM tool builders. As the cost of picosecond and femtosecond lasers come down - adoption, techniques, and material processes continue to expand. New features, higher power, efficient second and third harmonic generation are pushing the bounds of next gen use cases. PI is meeting these advances on the laser side with equally innovative motion control solutions to make disruptive next gen processes.
Advantages of Ultrafast Micromachining over Traditional Machining
As a non-contact localized micromachining method, lasers bypass conventional machining limitations that come with resolution and wear limitations. Additionally, ultrafast lasers are proving effective in processing flexible, brittle, and composite materials that have been historically difficult to machine precisely using conventional methods. Lasers can also be used to process below the surface of a material using tightly focused beams - useful in flexible displays and other technologies with transparent media including glass and sapphire.
Dynamic Impact of Mode-locked Laser Process Performance
Material specific laser process parameters running at a fixed pulse repetition frequencies (PRF) are typically optimized with consistent pulse overlap and constant average power. When operated at a fixed rep rate, the consistency of pulse overlap becomes of a function of motion system dynamics potentially in multiple dimensions:
Fig. 1a/b Laser pulse placement under constant velocity motion at fixed rep rate. Here, pulse overlap uniformity is correlated to motion system performance. Shown above is achievable single axis scanning performance using PI V-551 Stages on High Performance A-81x Series Motion Controller with PILOT Tech.
Fig. 1c/d Laser pulse placement during acceleration/deceleration on a single axis using fixed rep rate. Here, the pulse overlap uniformity would result in potentially undesirable material effect related to non-uniform power. To address constant pulse overlap on variable dynamics, a Laser Control Interface is used with Fixed Distance triggering to compensate for inconsistent motion.
Fig. 1e/f/g Laser pulse placement during multi-axis corner rounding motion using fixed rep rate. Here, the pulse overlap uniformity would result in potentially undesirable material effect especially related to potential HAZ in areas with punched pulses. There are two approaches to address this - essentially using fixed distance pulse picking through dedicated Laser Control Interface, or the advanced trajectory algorithms to run constant vector velocity.
Disruptive Technology and Next Gen Laser System Performance
The simple examples shown above have deceptively clever disruptive technology embedded in them. In the recent past, to implement such features in integrated motion systems for laser tool builders, these types of features imposed many constraints on system configuration, cost, stage selection, longer system startup, while also adding complexity and ultimately limiting top-end performance.
New Higher-performance, Lower Cost, and User-friendly Laser Tools
In these last-gen approaches, the high-speed motion synchronized laser trigger had to be pre-determined and delivered embedded in a high cost drive module. That module was also practically limited to incremental encoder protocols more typical to lower performance motion systems, namely square wave (A Quad B) signals. This approach also drastically reduced achievable trigger resolution using higher performance sin/cos encoders, while simultaneously restricting use of user-friendly absolute encoders, virtual axis for best use of gantries and lower cost, open-loop, stepper motor stage solutions.
Fig. 2 PI motion synchronized laser triggering can use the highest-resolution linear encoders. In previous approaches such an encoder would either be restricted to trigger on zero crossings or use an external interpolator that would restrict performance and potentially speed. More information on ultra-high-resolution encoders
More Flexible Laser Tools
In previous approaches, the motion system had to be pre-configured with higher cost drive technology which had to also potentially be re-configured if application requirements changed. The newer more disruptive approach makes it possible to add fast laser triggering to almost any system before or after delivery using a variety of drive technologies. The new approach is a more flexible and powerful solution for linking a laser to multi-axis positioning. The capability of synchronizing motion with external events are often described as position event generation (PEG) or position synchronized output (PSO).
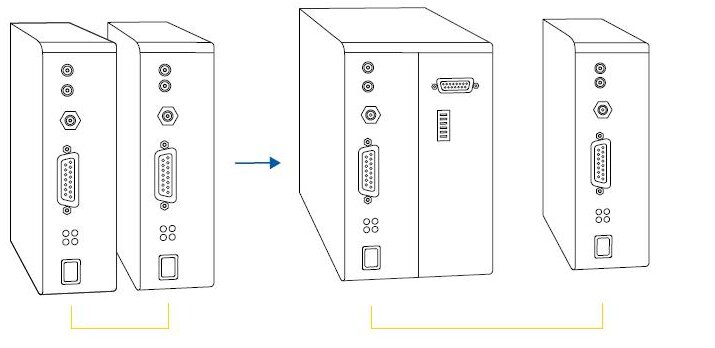
Fig. 4a (left) Now, system configurations are optimized to the application requirements without imposed limitations of a specific encoder feedback or drive. If high performance laser triggering is required, it’s merely an add-on module (LCM, shown right) that is configured for the system in minutes.
Fig. 4b (right) PI’s modular ACS Laser Control Module. The LCM laser control interface can achieve a max pulse frequency of 10 MHz and multi-axis position-based triggering with sub-micrometer laser pulse accuracy. It provides features such as: Fixed Distance & Array Based Pulse Firing, Dynamic Power Control by Digital Pulse Modulation, Axis Range Windowing, Array Based Gating, Tickle for Maintaining Laser Ready, Delay Compensation, and Combined Modes.
Higher Top-end Performance, Better Performance at Lower Cost, and More User-friendly Systems
With constraints on stages, drives, and encoder technologies removed, systems can now be configured to address the application requirements without detrimental cost or performance compromises.
This includes the use of high-performance (sin/cos) linear encoders without extra hardware, taking full advantage of state-of-the-art dynamic performance. With high speed synchronized laser control, the dominant error mode becomes trajectory following error - with both state-of-the art trajectory building, and following algorithms - this performance is unique at PI.
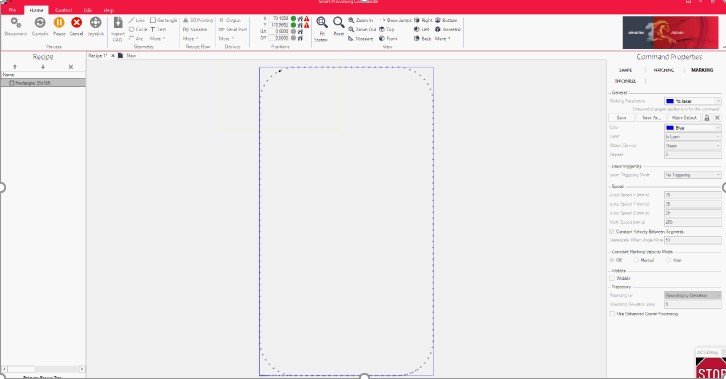
Fig. 5b/c Controller and stage performance: Here we see the performance of two compact, highly dynamic V-508 series linear motor stages in X-Y configuration, tracing a rounded rectangle in a laser cutting application.
Left: with PILOT algorithms
Right: without PILOT servo control
The green trace in both plots is the trajectory following error.
An advantage for motion stages in materials processing in general and especially for gantry systems, is the new ability to use more user-friendly, contamination resistant, and safe absolute linear encoders based on industry standard protocols (BiSS and EnDat). Each leg of a dual motor/dual encoder gantry axis is combined to form a virtual linear axis with a dual-theta loop using proprietary advanced gantry control. This disruptive approach can now use the virtual axis for laser triggering/pulse picking. This improves accuracy by not triggering from either side of the gantry but on the yaw-compensated virtual center axis while also removing a potential collision causing homing move.
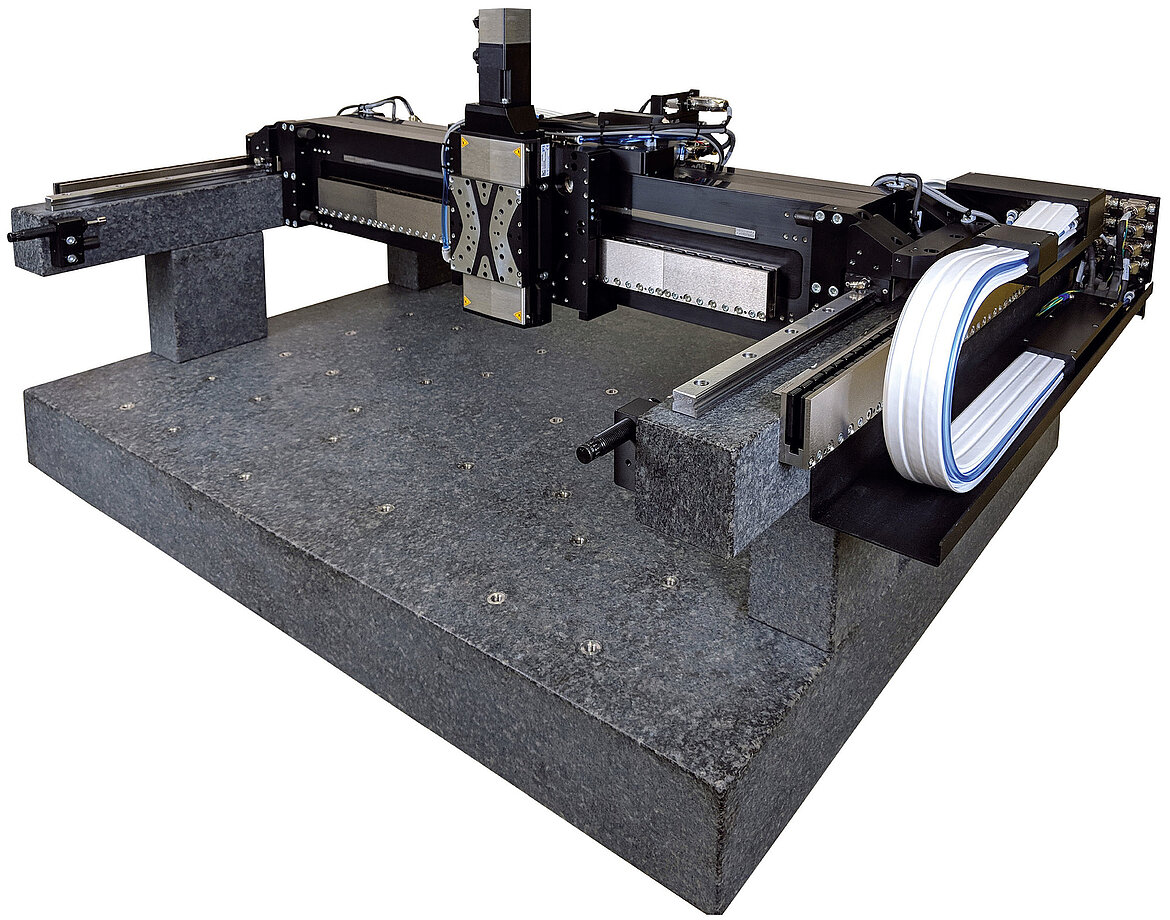
This new disruptive approach also allows advanced laser triggering without encoder feedback. Now, systems can be configured with lower cost stepper motors without encoders without sacrificing laser triggering capability.
Fig. 7a/b Not all laser processing applications require large positioning stages. The M-111 miniature XY stage, on the left, provides 15x15mm travel, 50nm incremental motion, and is available with stepper and servo motors. The F-408 XYZ stage (right) provides 25x25x25mm travel and 20nm incremental motion. It is equipped with linear motors and an air spring counterbalance on the vertical axis. Both systems can now be combined with High-Performance Motion Synchronized Laser Triggering.
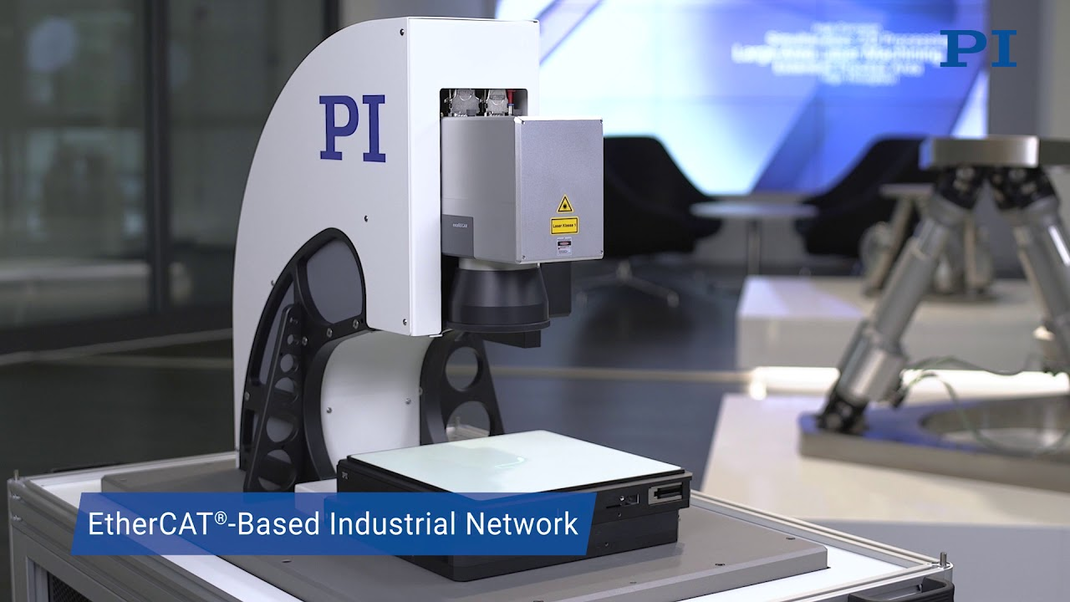
An important aspect of automation systems supporting laser materials processing tool builds is the ability to work optimally and flexibly with motion synchronized pulsed laser control and triggering (as well as CW), Flexible Galvo integration, G-Code compatibility, software supporting direct import of industry standard CAD file formats (DXF and STL) with direct to process in both 2D and 3D with flexible layering and infill settings.
In an approach with fixed optics, direct laser control can be done with multiple high-performance triggering and laser control modes and in a galvo or combined options - it’s possible to work flexibly with preferred galvo manufacturer, model and optical configuration.
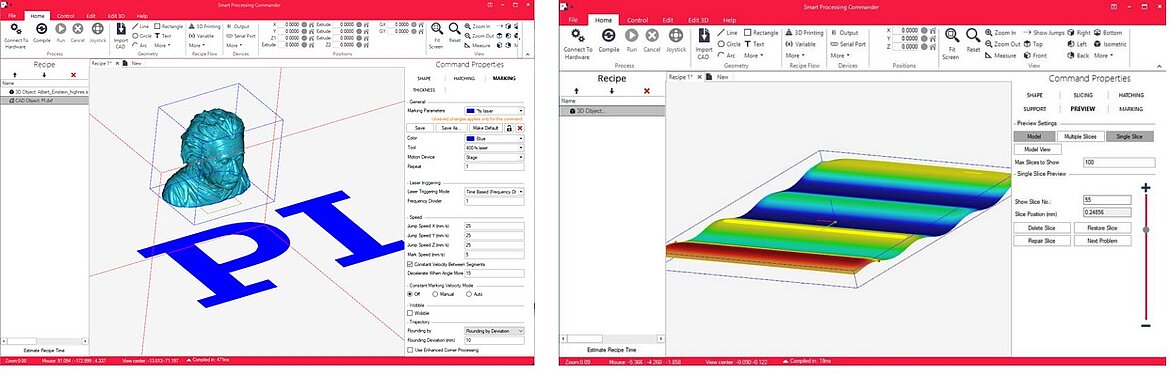
Summary
High performance ultrashort laser sources are now available at a reasonable cost, opening up many opportunities for machine builders and system integrators to replace less performant traditional machining methods. Advantages of laser processing are higher throughput, precision, and the ability to process ever smaller features. Typical processing applications require motion control (stages, gantries, controllers, and software). Recent advances in linking laser control and motion control allow better and more flexible synchronization between firing the laser and the exact location on the motion path. Expensive solutions with special controllers and closed system architectures have been available in the past, but now the industry is moving towards networks, such as EtherCAT, that make it far simpler to add functions and upgrade a system. The significant advantages for system integrators and machine builders now available through this level of connectivity allow them to choose the appropriate drivers, motion amplifiers, and controls for the motion system and the right interfacing for the laser, giving them simple, fast, accurate, and flexible control of their laser processing applications.
Please don’t hesitate to contact our engineers for more information and support with your motion system.
Blog Categories
- Aero-Space
- Air Bearing Stages, Components, Systems
- Astronomy
- Automation, Nano-Automation
- Beamline Instrumentation
- Bio-Medical
- Hexapods
- Imaging & Microscopy
- Laser Machining, Processing
- Linear Actuators
- Linear Motor, Positioning System
- Metrology
- Microscopy
- Motorized Precision Positioners
- Multi-Axis Motion
- Nanopositioning
- Photonics
- Piezo Actuators, Motors
- Piezo Mechanics
- Piezo Transducers / Sensors
- Precision Machining
- Semicon
- Software Tools
- UHV Positioning Stage
- Voice Coil Linear Actuator
- X-Ray Spectroscopy