Why Constant Velocity and Synchronized Motion Performance across Multiple Axes Matters for Ultrafast Laser Machining, Imaging, and Metrology
Children learn from an early age that focused light through a magnifying glass will create heat if left in the same position for too long or that pictures taken with an unsteady camera result in blurry images. In a modern context, these same principles apply to ultrafast lasers or line scan cameras where uniform motion is important to process optimization without defects or image distortion.
Modern laser processing, machine vision, and metrology systems rely on precision motion and automation mechanisms – and the ability to provide synchronized multi-axis dynamic motion performance with tight velocity regulation on complex trajectories has a big impact on the results.
If the path velocity is unstable, or during acceleration / deceleration phases the correlation of position and laser power is unknown or cannot be controlled tightly, the amount of material ablated, the quality of a cut or weld would vary, along with the velocity of the motion system.
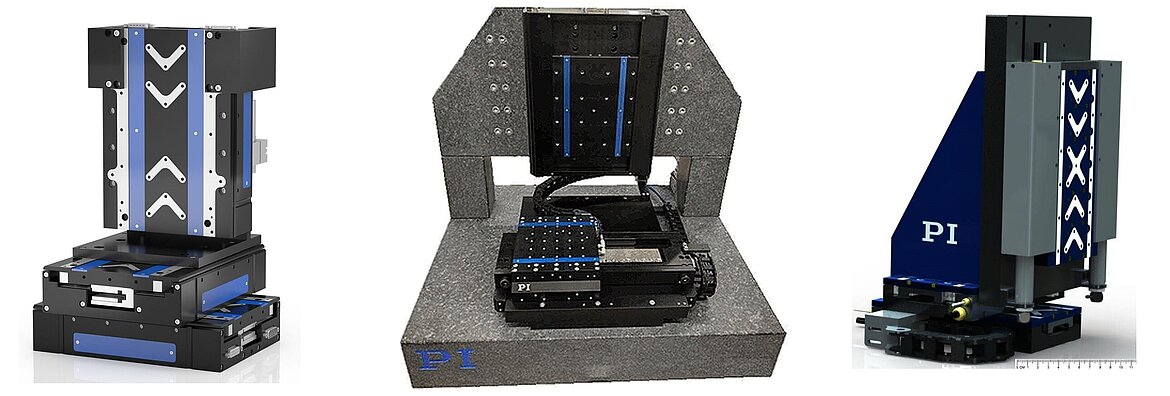
In order to avoid the above variations, a solid mechanical base with excellent dynamic properties, guiding, and position measuring systems is required. Here, proprietary technology extends from the core outward to the controls. It starts with stiff construction and an engineering design with low friction/quiet bearings (both mechanical and air) built on advanced grinding and machining processes. A prerequisite for high dynamics and excellent speed regulation, large ironless linear or torque motors are at the core of all positioning and automation systems for high precision industrial motion applications. Position feedback information is provided by proprietary nanometer- or sub-nanometer resolution linear encoders, preferably based on absolute measuring technology.
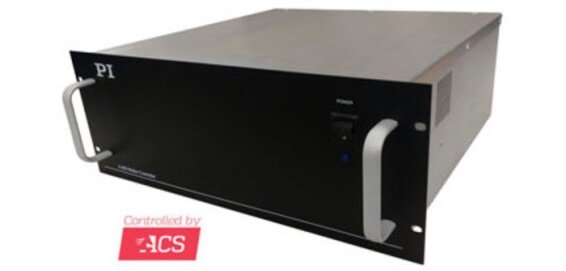
A-81x Series PIGlide Controllers based on ACS EtherCat connectivity with integrated low-noise amplifiers are optimized for dynamic range on the system and offer advanced multi-axis motion profiling algorithms to build complex optimized trajectory paths. These trajectory paths are followed with tight servo loops using real time disturbance attenuation resulting in best regulated dynamics to achieve world leading process goals.
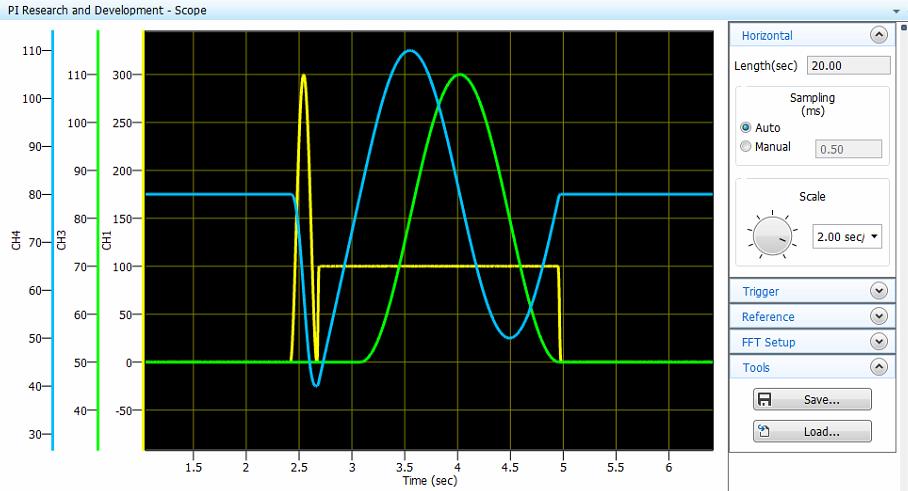
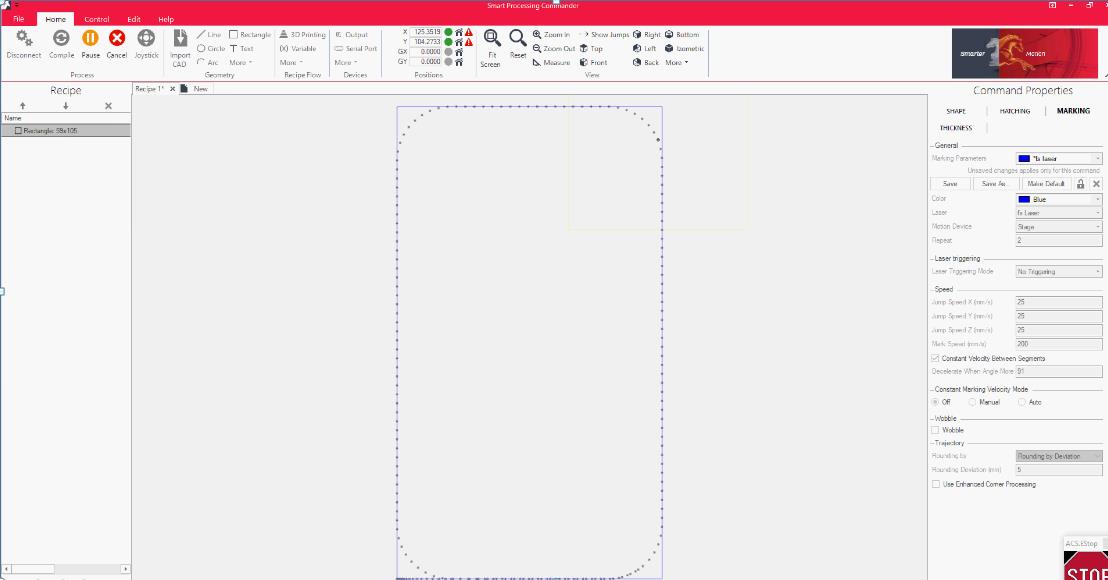
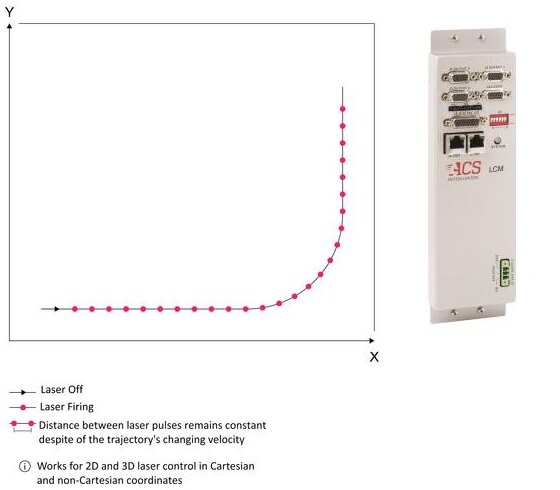
Blog Categories
- Aero-Space
- Air Bearing Stages, Components, Systems
- Astronomy
- Automation, Nano-Automation
- Beamline Instrumentation
- Bio-Medical
- Hexapods
- Imaging & Microscopy
- Laser Machining, Processing
- Linear Actuators
- Linear Motor, Positioning System
- Metrology
- Microscopy
- Motorized Precision Positioners
- Multi-Axis Motion
- Nanopositioning
- Photonics
- Piezo Actuators, Motors
- Piezo Mechanics
- Piezo Transducers / Sensors
- Precision Machining
- Semicon
- Software Tools
- UHV Positioning Stage
- Voice Coil Linear Actuator
- X-Ray Spectroscopy