The early foundations of 3D printing can be traced to mid-nineteenth century Paris and the work of Sculptor and Photographer, François Willeme. Willeme developed a patented photographic technique to capture and create 3D data models capable of being used to recreate solid objects. Further work in the later nineteenth century to generate topological relief maps, in a layer-by-layer fabrication approach, was done by Joseph Blanther. These concepts would be manifested in the first practical demonstration of 3D Printing in the 1980s, when Charles Hull made history with the invention of Stereolithography (SLA) with Selective Laser Sintering (SLS) to soon follow.
Since that time, additive manufacturing technology has evolved in both materials and methods leading to more precise structures generated in more functional materials with more demanding dimensional tolerances and feature sizes to the micron scale and sub-micron scale. Modern methods involve both direct material dispense (DIW, for example) and laser techniques, such as Two-Photon Polymerization, and in some cases, a combination of the two combined on a single system.
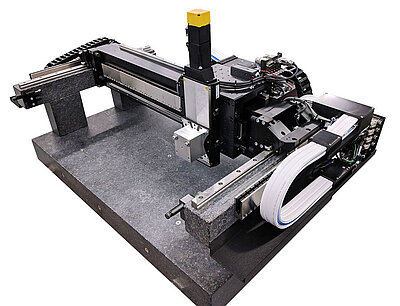
Direct Ink Writing
In material dispense, Direct Ink Writing (DIW) fabrication methods are playing an important role in the advancement of 3D printing at major research institutions, like the Colorado School of Mines. At these leading institutions, materials research and methods come with system level requirements that must consider an array of materials properties like rheological behavior, composition, feature size, and placement accuracy (especially critical for layer-by-layer fabrication with µm scale resolution) across the same coordinate system.
To address applications in DIW, PI provides a powerful and intuitive 3D Printing Software that allows direct import of industry standard STL files with flexible parameter settings and batch processing for multiple print jobs (far superior to alternative systems that are constrained to DXF file format and limitations for 3D Print). This software also allows integration of laser based processes with fixed or scanning optics, machine vision, and ability to integrate and communicate with other peripherals. The software conversion from model employs the most powerful trajectory algorithm and performance commercially available using ACS XSEG and material dispense is coordinated directly according to user-settings direct from motion controller through hardware layer to dispenser.
3D Printing motion systems are built from standard 3D Print optimized gantry platforms and pre-configured for use with Nordson Ultimus V (or customized to extruder). The direct hardware integration has been considered. The cabling for interface and triggering of the dispenser is provided with the system, optimized for controller cycle time and designed for correct trigger voltage. This allows for easy integration, powerful performance, and the motion sub-system to facilitate R&D and commercial 3D Printer builds.
With PI Motion, high performance 3D Print Systems can be built in a matter of days, work with industrial standard STL files, and offer the highest level of performance.
3D Bio-Printing
The promise and potential of directly printing living tissue, bone, cartilage, and organs is so disruptive in scope that it would appear to exist more in the domain of science fiction than reality. However, pioneers in the field of Bioprinting have already begun to adapt 3D printing technology to address applications in tissue engineering and regenerative medicine. Bioprinting comes at the leading edge of complexity of materials and general process tolerances. The process can require both mapping (through techniques like non-contact optical metrology and requires process control even at the cellular level). PI is prepared for the future of Bioprinting with high performance flying gantry systems that are completely non-wearing with software that can integrate third party peripherals like scanners and profilers (capable of both capturing 3D profiles) and executing layer-by-layer fabrication from such profiles.
What is a Gantry System?
Motion-centric systems, engineered for multi-axis operation with a moving overhead bridge are often called “Gantry System”. These types of precision motion systems are found in applications related to Automation, Digital Printing, 3D Printing, Scanning, Electronics Assembly and AOI (Automatic Optical Inspection). In general, a Gantry System provides an ideal solution when the workpiece must remain static with access from above. Linear-motor-driven gantries are used for highly dynamic, 24/7 processes, that necessitate high throughput and high precision.
Integrated Construction vs Discrete Stages
Typical gantry-type overhead motion systems designed by PI consist of a combination of several components at different levels of integration. For the highest performance, gantries are completely integrated, with bearing rails on granite, or air bearings. If demands on precision and performance are lower, gantries can be built from individual discrete linear stages. For optimum operation, specific gantry algorithms embedded in the motion controller can control Theta-Z motion and process information from multiple encoders per axis. As part of a complex design and manufacturing process, each component therefore needs to be carefully selected to fulfill the goal of the specific task at hand.
Performance Designed for your Needs
Consequently, every PI Gantry System is individually crafted to align with your unique specifications and needs. With the capacity for in-house design and production, our prior experience and pre-existing modules serve to notably expedite development times. By leveraging these strengths, we guarantee that our systems are adaptable, user-friendly, and swift to implement, no matter the volume required.
Blog Categories
- Aero-Space
- Air Bearing Stages, Components, Systems
- Astronomy
- Automation, Nano-Automation
- Beamline Instrumentation
- Bio-Medical
- Hexapods
- Imaging & Microscopy
- Laser Machining, Processing
- Linear Actuators
- Linear Motor, Positioning System
- Metrology
- Microscopy
- Motorized Precision Positioners
- Multi-Axis Motion
- Nanopositioning
- Photonics
- Piezo Actuators, Motors
- Piezo Mechanics
- Piezo Transducers / Sensors
- Precision Machining
- Semicon
- Software Tools
- UHV Positioning Stage
- Voice Coil Linear Actuator
- X-Ray Spectroscopy