PIFOC focus scanner for microscope objectives, high precision, fast step-and-settle, 100 µm, capacitive sensors, D-sub connector
P-725.xCDE2 PIFOC Focus Scanner for Microscope Objectives
Dynamic Scanning with Travel Ranges of 100 µm, 400 µm, or 800 µm
- Travel range 100 µm, 400 µm, or 800 µm
- Significantly faster response and longer lifetime than motorized drives
- Fine positioning of objectives with sub-nm resolution
- Direct position measuring with capacitive sensors: Highest linearity
- Large clear aperture with Ø 29 mm










Application fields
- Super-resolution microscopy
- Light disk microscopy
- Confocal microscopy
- 2-photon microscopy
- 3D imaging
- Screening
- Interferometry
- Measuring technology
- Autofocus systems
- Biotechnology
- Semiconductor inspection
Outstanding lifetime due to PICMA® piezo actuators
The PICMA® piezo actuators are all-ceramic insulated. This protects them against humidity and failure resulting from an increase in leakage current. PICMA® actuators offer an up to ten times longer lifetime than conventional polymer-insulated actuators. 100 billion cycles without a single failure are proven.
Subnanometer resolution with capacitive sensors
Capacitive sensors measure with subnanometer resolution without contacting. They guarantee excellent linearity of motion, long-term stability, and a bandwidth in the kHz range.
High guiding accuracy due to zero-play flexure guides
Flexure guides are free of maintenance, friction, and wear, and do not require lubrication. Their stiffness allows high load capacity and they are insensitive to shock and vibration. They work in a wide temperature range.
Specifications
Specifications
Motion | P-725.1CDE2 | P-725.4CDE2 | P-725.8CDE2 | Tolerance |
---|---|---|---|---|
Active axes | Z | Z | Z | |
Travel range in Z | 100 µm | 400 µm | 800 µm | +20 / -0 % |
Travel range in Z, open loop | 120 µm | 420 µm | 840 µm | ±20 % |
Linearity error in Z | < 0.03 % | < 0.03 % | < 0.03 % | |
Angular error around X | ± 10 µrad | ± 10 µrad | ± 50 µrad | |
Angular error around Y | ± 10 µrad | ± 45 µrad | ± 50 µrad | |
Positioning | P-725.1CDE2 | P-725.4CDE2 | P-725.8CDE2 | Tolerance |
Minimum incremental motion in Z | 1 nm | 4 nm | 5 nm | |
Point repeatabilitiy, 10% step, 1 sigma | 10 nm | 10 nm | 50 nm | |
Integrated sensor | Capacitive, direct position measuring | Capacitive, direct position measuring | Capacitive, direct position measuring | |
Sensor noise, 1 sigma | 0.2 nm | 0.2 nm | 0.8 nm | |
Position noise in Z | 0.1 nm | 0.1 nm | 0.4 nm | max. |
Settling time for 10% step in Z | 14 ms | 22 ms | 39 ms | ±10 % |
Drive Properties | P-725.1CDE2 | P-725.4CDE2 | P-725.8CDE2 | Tolerance |
Drive type | PICMA® | PICMA® | PICMA® | |
Electrical capacitance in Z | 3.2 µF | 6.4 µF | 12.8 µF | ±20 % |
Mechanical Properties | P-725.1CDE2 | P-725.4CDE2 | P-725.8CDE2 | Tolerance |
Stiffness in Z | 0.5 N/µm | 0.25 N/µm | 0.07 N/µm | ±20 % |
Resonant frequency in Z, unloaded | 680 Hz | 400 Hz | 230 Hz | ±20 % |
Resonant frequency in Z, under load with 150 g | 290 Hz | 175 Hz | 110 Hz | ±20 % |
Permissible push force in Z | 100 N | 100 N | 100 N | max. |
Permissible pull force in Z | 20 N | 20 N | 20 N | max. |
Guide | Flexure guide with lever amplification | Flexure guide with lever amplification | Flexure guide with lever amplification | |
Overall mass | 280 g | 280 g | 350 g | ±5 % |
Material | Stainless steel, aluminum | Stainless steel, aluminum | Stainless steel, aluminum | |
Objective diameter | 39 mm | 39 mm | 39 mm | max. |
Miscellaneous | P-725.1CDE2 | P-725.4CDE2 | P-725.8CDE2 | Tolerance |
Operating temperature range | 10 to 70 °C | 10 to 70 °C | 10 to 70 °C | |
Connector | D-sub 7W2 (m) | D-sub 7W2 (m) | D-sub 7W2 (m) | |
Cable length | 1.5 m | 1.5 m | 1.5 m | +50 / -0 mm |
Recommended controllers / drivers | E-709.1C1L - economic choice, suitable for most use cases; E-754.1CD - high performance choice for highest precision | E-709.1C1L - economic choice, suitable for most use cases; E-754.1CD - high performance choice for highest precision | E-709.1C1L - economic choice, suitable for most use cases; E-754.1CD - high performance choice for highest precision |
Linearity error in Z: Under laboratory conditions, a digital controller makes it possible to reduce the linearity error even further.
Settling time: 1% error band, 150 g load
Position noise: 1 sigma
The objective is not included in the scope of delivery.
At PI, technical data is specified at 22 ±3 °C. Unless otherwise stated, the values are for unloaded conditions. Some properties are interdependent. The designation "typ." indicates a statistical average for a property; it does not indicate a guaranteed value for every product supplied. During the final inspection of a product, only selected properties are analyzed, not all. Please note that some product characteristics may deteriorate with increasing operating time.
Downloads
Datasheet
Documentation
User Manual P725UM0001
P-725.xCDE2 PIFOC Focus Scanners for Microscope Objectives
Installation Instructions P725UM0002
Thread Adapters for P-725.xCDE2 PIFOC Focus Scanners and P-725.xCDE1S PIFOC Scanner Systems
3D Models
3-D model P-725.xCDE2
Brochure
P-725 PIFOC® Portfolio
Piezobased Objective Focus Drive Series
Ask for a free quote on quantities required, prices, and lead times or describe your desired modification.
PIFOC focus scanner for microscope objectives, high precision, fast step-and-settle, 400 µm, capacitive sensors, D-sub connector
PIFOC focus scanner for microscope objectives, high precision, fast step-and-settle, 800 µm, capacitive sensors, D-sub connector
How to Get a Quote
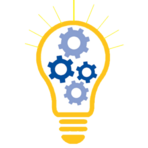
Questions? - Ask a PI Engineer
Technology
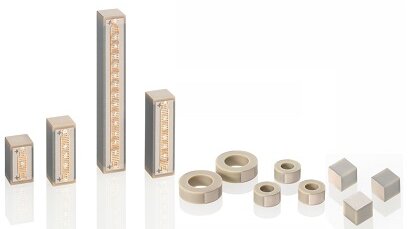
PICMA® Technology
Highly reliable and extended lifetime through the patented manufacturing process for multilayer actuators.
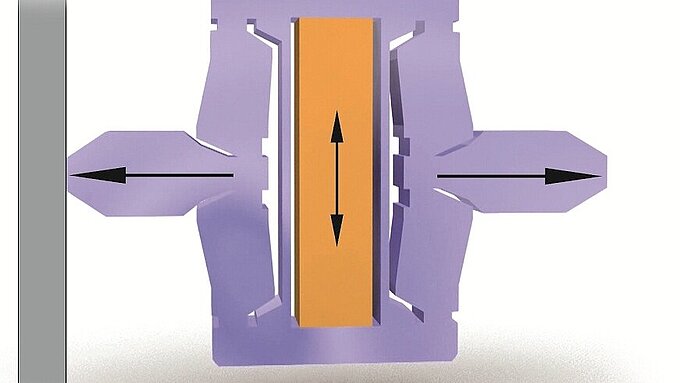
Flexure Guiding Systems
Flexure guides from PI have proven their worth in nanopositioning. They guide the piezo actuator and ensure a straight motion without tilting or lateral offset.
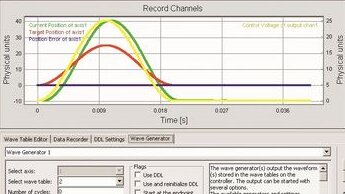
Digital Motion Controllers
Digital technology opens up possibilities for improving performance in control engineering which do not exist with conventional analog technology.
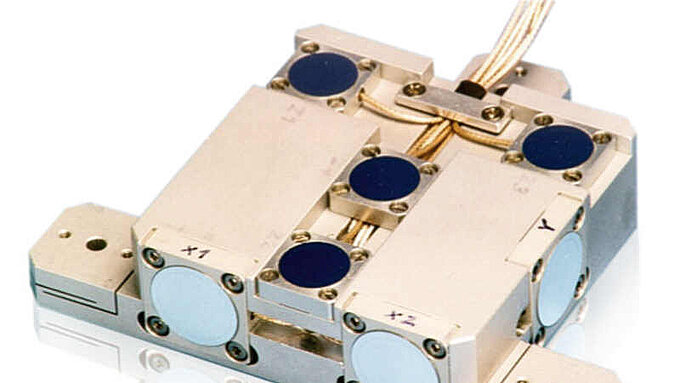
Capacitive Sensors
Capacitive sensors are the metrology system of choice for the most demanding nanopositioning applications.
Applications
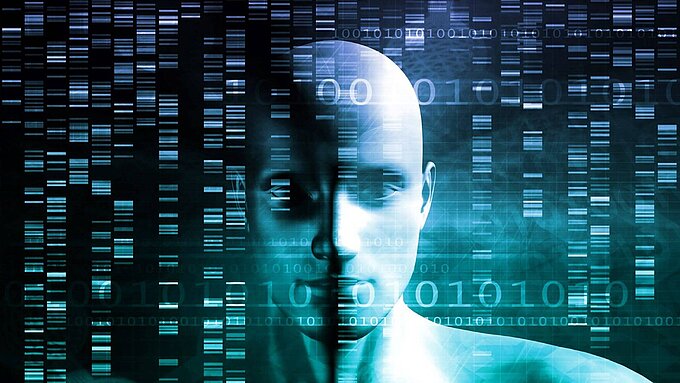
Genome Sequencing
Be it in medicine, forensics, or genetics - the genome is the key to new insights for numerous questions. The method known as sequencing-by-synthesis, which used to decipher the genome, has become faster and more precise since it was first developed — the cost has decreased, respectively. The positioning techniques employed in the microscope systems used for this purpose have also contributed to...
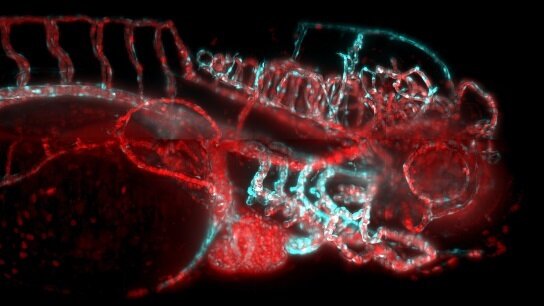
IsoView Light Sheet Microscope
Light Sheet Microscopy is a fascinating technology with a huge application potential in life sciences and biotechnology. IsoView is a brilliant interpretation of this technology, especially intended for imaging fast cellular dynamics across large specimens over several hours. Specimen positioning and objective translation plays a major role in the design of IsoView.
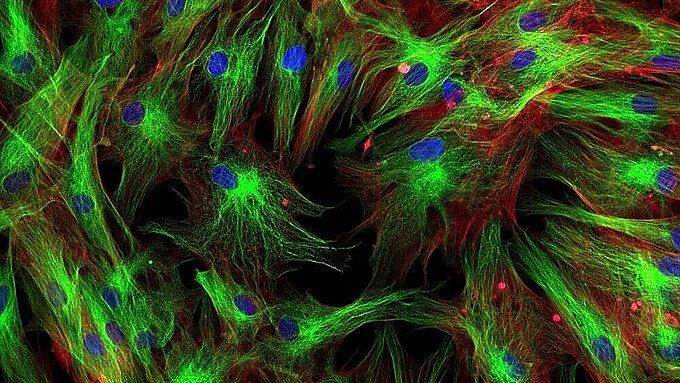
GATTAscope (TIRFM)
Linear stages adjust the laser beam in the TIRF microscope. Precision positioning of the sample is possible by combining two XY stages.
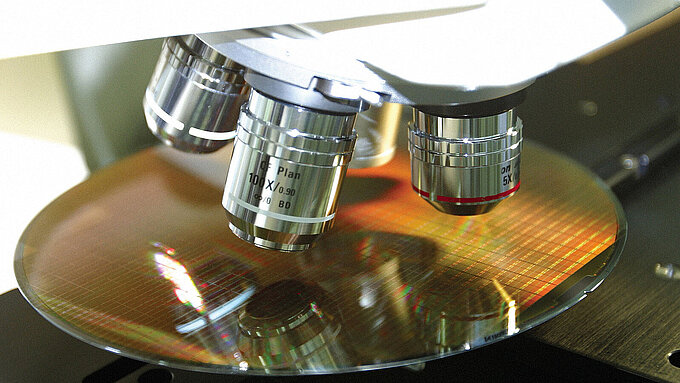
High-Speed Microscopy
For the first time ever, scientists from the Fraunhofer Institute for Production Technology IPT in Aachen have succeeded in achieving 100 percent microscopic testing in the industrial environment. The piezo-based PIFOC® drive system from PI was decisive for this success.
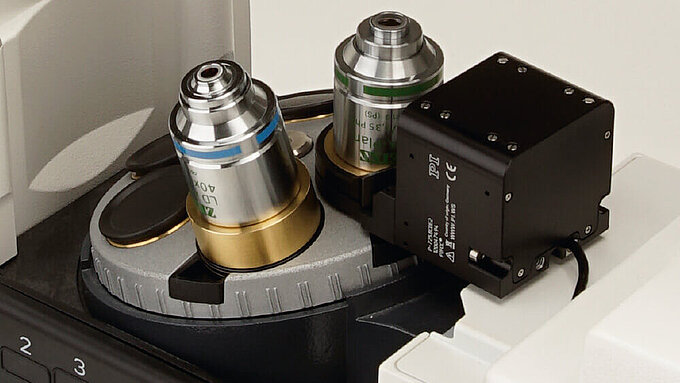
Confocal Microscopy
Confocal microscopy is used to detect the structure of the sample surface through the shifting of the focal plane, for example in dermatology.

Optical Coherence Tomography
Piezo actuators and drives, e.g., PILine® OEM motors, ensure the high precision and position stability required for optical coherence tomography (OCT).