PIFOC high-load focus scanner; 100 µm travel range; capacitive, direct position measuring; D-sub 7W2 (m); 1.5 m cable length
P-726 PIFOC High-Load Focus Scanner
Highly Dynamic Focus Scanner with Long Travel Range for Heavy Objectives
- Highly dynamic positioning and scanning for large objectives
- Resonant frequency 1120 Hz; 560 Hz with 210 g objective mass
- Typ. step-and-settle about 6 ms
- Travel range 100 µm
- Highest linearity, stability, and control dynamics due to direct-measuring capacitive sensors
- Resolution 0.3 nm
- Zero-play, high-precision flexure guide system for better focus stability
Application fields
- Super-resolution microscopy
- Light disk microscopy
- Confocal microscopy
- 3-D imaging
- Screening
- Interferometry
- Measuring technology
- Autofocus systems
- Biotechnology
- Semiconductor tests
Outstanding lifetime thanks to PICMA® piezo actuators
The PICMA® piezo actuators are all-ceramic insulated. This protects them against humidity and failure resulting from an increase in leakage current. PICMA® actuators offer an up to ten times longer lifetime than conventional polymer-insulated actuators. 100 billion cycles without a single failure are proven.
Subnanometer resolution with capacitive sensors
Capacitive sensors measure with subnanometer resolution without contacting. They guarantee excellent linearity of motion, long-term stability, and a bandwidth in the kHz range.
High guiding accuracy due to zero-play flexure guides
Flexure guides are free of maintenance, friction, and wear, and do not require lubrication. Their stiffness allows high load capacity and they are insensitive to shock and vibration. They work in a wide temperature range.
Automatic configuration and fast component exchange
Mechanics and controllers can be combined as required and exchanged quickly. All servo and linearization parameters are stored in the ID chip of the D-sub connector of the mechanics. The autocalibration function of the digital controllers uses this data each time the controller is switched on.
Maximum accuracy due to direct position measuring
Motion is measured directly at the motion platform without any influence from the drive or guide elements. This allows optimum repeatability, outstanding stability, and stiff, fast-responding control.
Specifications
Specifications
Motion | P-726.1CD | Tolerance |
---|---|---|
Active axes | Z | |
Travel range in Z | 100 µm | |
Travel range in Z, open loop | 100 µm | +20 / -0 % |
Linearity error in Z | 0.02 % | typ. |
Positioning | P-726.1CD | Tolerance |
Point repeatabilitiy in Z, 10% step, 1 sigma | 3 nm | |
Resolution in Z, open loop | 0.3 nm | typ. |
Integrated sensor | Capacitive, direct position measuring | |
System resolution in Z | 0.4 nm | |
Drive Properties | P-726.1CD | Tolerance |
Drive type | PICMA® | |
Electrical capacitance in Z | 6 µF | ±20 % |
Mechanical Properties | P-726.1CD | Tolerance |
Stiffness in Z | 3.4 N/µm | ±20 % |
Resonant frequency in Z, unloaded | 1120 Hz | ±20 % |
Resonant frequency in Z, under load with 210 g | 560 Hz | ±20 % |
Resonant frequency in Z, under load with 310 g | 480 Hz | ±20 % |
Permissible push force in Z | 100 N | max. |
Permissible pull force in Z | 50 N | max. |
Guide | Flexure guide with lever amplification | |
Overall mass | 575 g | |
Material | Aluminum, steel | |
Mechanical interface | M32 inner thread (can be adapted to all common threads using a QuickLock thread adapter) | |
Miscellaneous | P-726.1CD | Tolerance |
Operating temperature range | -20 to 80 °C | |
Connector | D-sub 7W2 (m) | |
Cable length | 1.5 m | +50 / -0 mm |
Recommended controllers / drivers | E-505, E-621, E-625, E-709.1C1L, E-754 |
The resolution of the system is limited only by the noise of the amplifier and the measuring technology because PI piezo nanopositioning systems are free of friction.
Downloads
Product Note
Product Change Notification Piezo Actuator Driven Products
Datasheet
Documentation
User Manual P726T0002
P-726.1CD PIFOC® High-Load Objective Scanner
Installation Instructions P726T0001
P-726.xx QuickLock Thread Adapters for P-726 PIFOC
3D Models
3-D-model P-726.1CD
Quote / Order
Ask for a free quote on quantities required, prices, and lead times or describe your desired modification.
How to Get a Quote
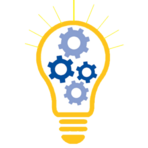
Questions? - Ask a PI Engineer
Technology
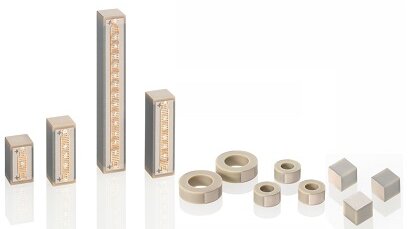
PICMA® Technology
Highly reliable and extended lifetime through the patented manufacturing process for multilayer actuators.
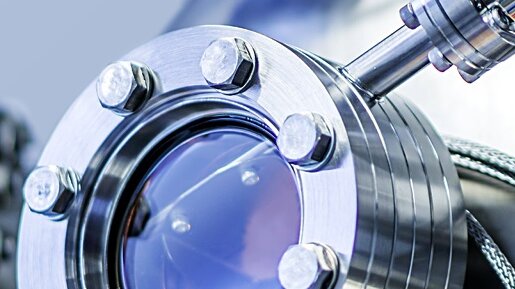
Vacuum
Careful handling, adequate premises: PI does not only have the necessary equipment for the qualification of materials, components and final products, but also has many years of experience with regard to HV und UHV positioning systems.
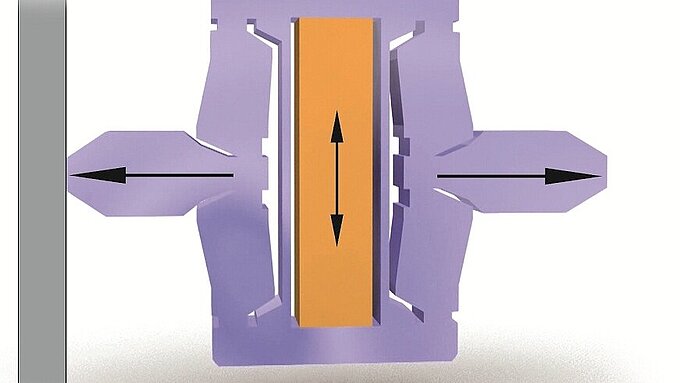
Flexure Guiding Systems
Flexure guides from PI have proven their worth in nanopositioning. They guide the piezo actuator and ensure a straight motion without tilting or lateral offset.
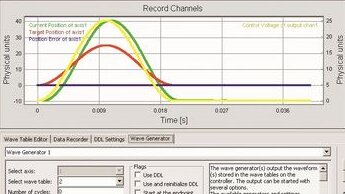
Digital Motion Controllers
Digital technology opens up possibilities for improving performance in control engineering which do not exist with conventional analog technology.
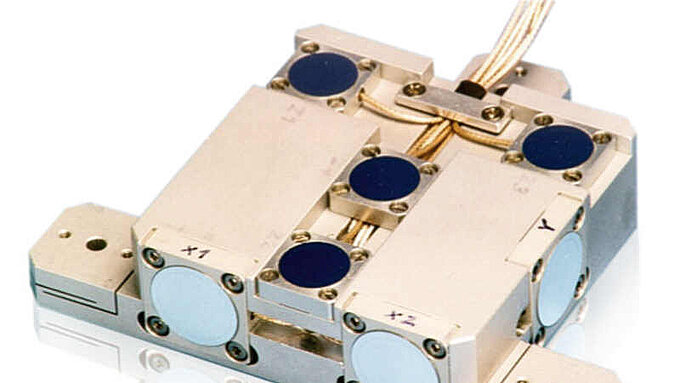
Capacitive Sensors
Capacitive sensors are the metrology system of choice for the most demanding nanopositioning applications.
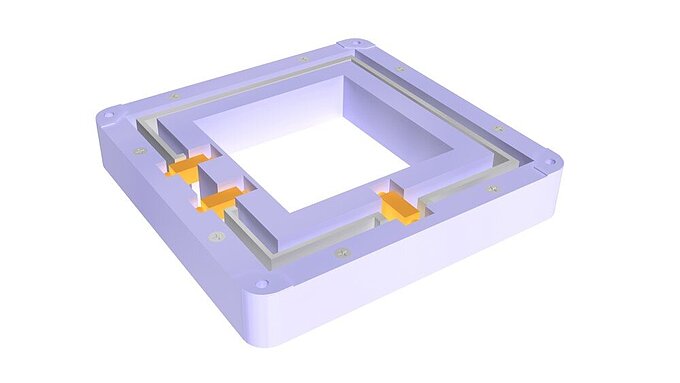
Piezo Positioning Systems with Parallel Kinematics
In a parallel-kinematic, multi-axis system, all actuators act directly on a single moving platform.