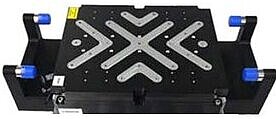
Magnetic levitation, often referred to as maglev, is a frictionless motion technology that uses magnetic fields to levitate and propel objects. It is used in various applications, best known from high-speed trains and magnetic bearings, and has great benefits for precision motion control and nanopositioning technology.
The basic principle of magnetic levitation is that like magnetic poles repel each other. To achieve magnetic levitation in its most simple form, two magnets are used; one magnet is placed in the object that needs to be levitated, and the other magnet is placed beneath it.
To make this principle useful for precision motion control, for example in linear stages, the magnets in the base must be electrically controllable coils and it takes more than just a pair to also control lateral motion, vertical motion and pitch, yaw, and roll. In many practical implementations, Hallbach arrays are used to minimize the energy consumption, increase the load capacity, and reduce thermal energy dissipation.
A position sensing system is also required to provide feedback to the motion controller. Since no mechanical bearings restrict the motion of the linear stage platform to precisely one degree of freedom, a powerful, high-bandwidth multi-axis controller is required to keep all other degrees of freedom in check.
While this seems complicated, the benefits can be huge. Not being limited by a mechanical bearing adds an incredible amount of freedom to electronically correct bearing insufficiencies. It also allows for controlled small angular motions, e.g., to align a sample perfectly with an optics or camera or chip without the need for adding a bulky theta stage to the linear stage. In addition, vertical motions can be programmed, very useful for precise focusing.
PI has been investing in research on magnetic levitation for nanopositioning applications and will work with customers to move the technology forward together. A technology demonstrator is available at PI’s Silicon Valley tech center.
- Guiding of all six degrees of freedom actively controlled and controllable
- Guiding behavior can be defined by sensor and controls. Some degrees of freedom can be actively used for positioning, in addition to the main X-axis.
- Steady state stability (jitter) is neither influenced by stick-slip effects nor by air flow
- Frictionless guiding: no rolling elements, no lubrication, no air flow
- No stick slip effects, no maintenance, no wear and tear, no abrasion from rolling elements
- No particle generation, highest cleanliness, ideal for cleanroom applications
- Highest precision possible, solely depending on sensors, drives and controls / control loop
- Vacuum compatibility possible
- No outgassing from lubricants, encapsulation of critical materials
The compact technology demonstrator has the following specifications:
- Linear travel range in X: 44mm
- Linear travel range in Y, Z: 0.5mm
- Rotational range in Theta X, Y, Z: 5mrad
- Max. Velocity in X: 400mm/s
- Load: up to 2kg w/o increased power consumption
- Upside-down operation feasible
- Fully passive slider, no cable connections to the static base
- Dimensions: 200x160x45mm
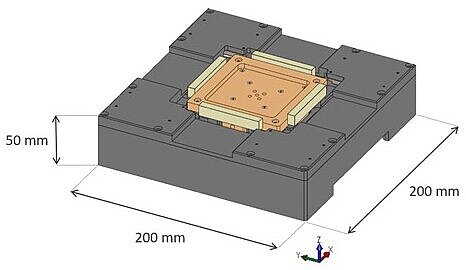
PI is one of the partners in the MetExSPM project and EMPIR (European Metrology Research Programme) initiative.
PI will design a planar magnetic levitation picopositioning stage and hybrid piezo stages. The project’s goal is to develop an ultra-high-performance scanning probe microscope.
Preliminary specs for the planar motion stage for sample positioning and scanning are:
- Position resolution: < 100 picometers
- Position noise (1σ): < 300 picometers
- Bandwidth (1µm amplitude): ≈100 Hz
- XY travel range: 12.7x12.7mm
- Z travel range: ±0.25mm
- Rotation range (pitch, roll, yaw): ±0.25°
- Motion velocity (XY plane): 10mm/s
- Acceleration (XY plane): 1 m/s²
Blog Categories
- Aero-Space
- Air Bearing Stages, Components, Systems
- Astronomy
- Automation, Nano-Automation
- Beamline Instrumentation
- Bio-Medical
- Hexapods
- Imaging & Microscopy
- Laser Machining, Processing
- Linear Actuators
- Linear Motor, Positioning System
- Metrology
- Microscopy
- Motorized Precision Positioners
- Multi-Axis Motion
- Nanopositioning
- Photonics
- Piezo Actuators, Motors
- Piezo Mechanics
- Piezo Transducers / Sensors
- Precision Machining
- Semicon
- Software Tools
- UHV Positioning Stage
- Voice Coil Linear Actuator
- X-Ray Spectroscopy