Mechanical Considerations
There is no international standard for measuring piezo actuator stiffness. Therefore stiffness data of different manufacturers cannot be compared without additional information.
Maximum Applicable Forces
(Compressive Load Limit, Tensile Load Limit)
The mechanical strength values of Piezo ceramic material (given in the literature) is often confused with the practical long term load capacity of a Piezo actuator. Piezo ceramic material can withstand pressures up to 250 MPa (2500 x 105 N/m²) before it breaks mechanically. For practical applications, this value must not be approached because depolarization occurs at pressures on the order of 20 to 30 % of the mechanical limit. For actuators (which are a combination of several materials) additional rules apply. Parameters such as aspect ratio, buckling, interaction at the interfaces etc. must be considered. If the maximum compressive force for a Piezo is exceeded, damage to the ceramics as well as depolarization may occur.
The load capacity data listed for PI actuators are conservative values which allow long lifetime. Standard PI Piezo stack actuators can withstand compressive forces to several 10,000 N (@ several tons).
Tensile loads of non preloaded PZTs are limited to 5 - 10 % of the compressive load limit. PI offers a variety of piezo actuators with internal spring preload for extended tensile load capacity. Preloaded elements are highly recommended for dynamic applications.
Shear forces must be isolated from the Piezo ceramics by external measures (flexure guides, etc.).
Stiffness
When calculating force generation, resonant frequency, system response, etc., piezo stiffness is an important parameter. In solid bodies stiffness depends on the Young's Modulus which is the ratio of stress (force per unit area) to strain (change in length per unit length). It is generally described by the spring constant kT, relating the influence of an external force to the Dimensionsal change of the body.
This narrow definition does not apply fully for Piezo ceramics; large and small signal conditions, static and dynamic operation, open and shorted electrodes must be distinguished. The poling process of Piezo ceramics leaves a remanent strain in the material which depends on the magnitude of polarization. The polarization is affected by both the drive voltage and external forces. When an external force is applied to poled Piezo ceramics, the Dimensionsal change depends on the stiffness of the ceramic material and the change of the remanent strain (caused by the polarization change). The equation LN = F/kT is only valid for small forces and small signal conditions. For larger forces, an additional term describing the influence of the polarization changes, is superimposed on stiffness (kT).
Since piezo ceramics are active materials, they produce an electrical response (charge) when mechanically stressed (e.g. in dynamic operation). When the electric charge cannot be drained from the Piezo, it generates a counter force to the mechanical stress. This is why a Piezo element with open electrodes appears stiffer than one with shorted electrodes. With actuators (compound structures of different active and passive materials) the scenario is even more complicated.
The above discussion explains why the (dynamically measured) resonant frequency of a piezo actuator does not necessarily match the results calculated with the "simple harmonic oscillator equation": f0 = (1/2π)*√(kT/meff) with statically measured stiffness. (For more details see "Resonant Frequency").
Since stiffness values of Piezo actuators are not constants they can only be used to estimate the behavior under certain conditions and to compare different Piezo actuators of one manufacturer.
Mechanical Considerations
It must be understood that a piezo actuator can only generate considerable force if it is directly coupled (no slack!) to an element which is stiff when compared to the Piezo.
Force Generation
In most applications, piezo actuators are used to produce displacement. If used in a restraint, they can generate forces. Force generation is always coupled with a reduction in displacement. The maximum force (blocked force) a piezo actuator can generate depends on its stiffness and maximum displacement.
Fmax ≈ kT*ΔLO (4-3)
Maximum force that can be generated in an infinitely rigid restraint (infinite spring constant). At maximum force generation, displacement is zero.
where
ΔL0 = max. nominal displacement without external force or restraint [m]
kT = Piezo actuator stiffness [N/m]
In actual applications the load spring constant can be larger or smaller than the Piezo spring constant. The force Fmax eff generated by the Piezo is:
Fmax eff ≈ kT*ΔL0 (1-kT/(kT+kS)) (4-4)
Effective force a piezo actuator can generate in a yielding restraint
where
ΔL0= displacement (without external force or restraint) [m]
kT = Piezo actuator stiffness [N/m]
ks = spring stiffness [N/m].
Example:
Force generation of P-845.20. The Piezo can produce a maximum force of 30 mm * 200 N/mm = 6000 N. When force generation is maximum, displacement is zero. At full displacement no force can be generated (see Fig. 4.23/1 for details).
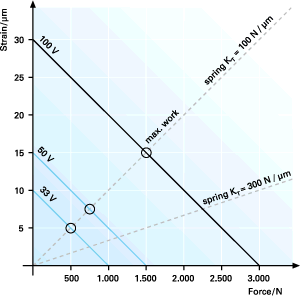
Example:
A piezo actuator is to be used in a metal sheet embossing application. At rest (zero position) the distance between the Piezo tip and the sheet is 30 microns (given by mechanical system tolerances). A force of 500 N is required to emboss the metal.
Q: Can a 60 µm actuator with a stiffness of 100 N/µm be used?
A: Under ideal conditions this actuator can generate a force of 30 x 100 N = 3000 N (30 microns are lost motion due to the distance between the sheet and the Piezo tip). In reality the force generation depends on the stiffness of the metal and the support. If the support was a soft material, with a stiffness of 10 N/µm the Piezo could only generate a force of 300 N onto the metal when operated at maximum drive voltage. If the support was stiff but the metal itself was very soft (gold, aluminum, etc.) it would yield and the piezo actuator still could not generate the required force. If both the support and the material were stiff enough, but the Piezo mount was too soft, the force generated by the Piezo would push the actuator away from the material to be embossed. The situation is similar to lifting a car with a jack. If the ground (or the car's body) is too soft, the jack will run out of travel before it generates enough force to lift the wheels off the ground.
If you have any questions, ask a PI engineer for help.