High Resolution Sensors for Nanometer-Class Positioning Devices
The following description explains the features of different high resolution sensor types used for closed loop control of Piezo actuators. The given bandwidth is open loop bandwidth of the sensor. Closed loop bandwidth of a Piezo/sensor/servo controller system is limited by the mechanical and electrical properties of the system.
Capacitive Position Sensors
Based on the capacitance between two plates.
The sensor consists of two RF excited plates that are part of a capacitive bridge. One plate is fixed, the other plate is connected to the object to be positioned. The distance between the plates is inversely proportional to the capacitance which is a measure for the displacement. Resolution on the order of picometers is achievable with short range capacitive position sensors. (See "Capacitive Displacement Sensors" section for details).
Resolution: better than 0.1 nm
Repeatability: up to 0.1 nm
Bandwidth: up to 10 kHz
Advantages:
- highest resolution of all commercially available sensors
- excellent long term stability
- excellent frequency response
Other features:
- extra space for mounting required
- parallelism of the plates must be controlled for optimal performance of the plates
Examples:
P-500 series of Flexure Stages
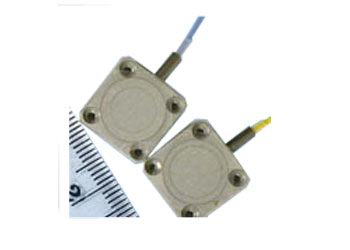
Strain Gage Sensors
Based on the principle of electrical resistance.
There are two basic types: semiconductor strain gauges (piezo resistive) and film / wire strain gauges (classic)
Piezoresistive strain gauges (silicon) provide a higher gage factor, are extremely compact. Foil type sensors have small advantages when it comes to linearity, temperature stability and by covering a larger area, they provide advantages when applied to large piezo stack actuators.
Example of piezo nanopositinoing stage with piezo resistive position sensors.

Foil gauges work as a resistive film, bonded to the piezo material changes resistance when strain is applied. Up to four strain gages (the actual configuration varies with the Piezo construction) form a Wheatstone bridge driven by a DC voltage (5 to 10 V). When the bridge resistance changes, electronics converts the resulting voltage change into a signal analogous to displacement.
Resolution: better than 1 nm (for 15 µm actuator)
Repeatability: up to 0.1% of nominal displacement
Bandwidth: up to 5 kHz
Advantages:
- high bandwidth
- high-vacuum compatible
- extremely small (no extra mounting space/no reduction of active cross section causing reduced stiffness)
- cost effective
Other Features
- low heat generation (0.01 to 0.05 W sensor excitation power)
- long term position accuracy (> 1 h) may be affected by the bond between sensor and Piezo ceramics
- measuring principle (inferred vs. direct) can lead to reduced absolute accuracy
Examples: Most PI LVPZT and HVPZT actuators are available with strain gage sensors for closed loop control (see "Piezo Actuators" section).
Linear Variable Differential Transformers (LVDTs)
Based on the principle of magnetic induction.
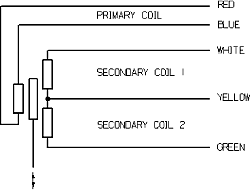
A magnetic core, attached to the moving part, determines the amount of magnetic energy induced from the primary windings into the two differential secondary windings. The carrier frequency is typically 10 kHz.
Resolution: up to 10 nm
Repeatability: up to 0.1% of nominal displacement
Bandwidth: up to 1 kHz
Advantages:
- good temperature stability
- very good long term stability
- controls the position of the moving part rather than the position of the Piezo stack
- cost effective
Other features
- outgassing of insulation materials may limit applications in UHV
- extra space for mounting required
Examples:
P-780, P-721.10, P-762.
If you have any questions, ask a PI engineer for help.