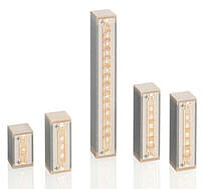
Active vibration isolation considerably reduces settling times, increases precision in measurement and production sequences and achieves high throughput rates. The systems that can benefit from this include laboratory set-ups, laser technology, mechanical engineering, optical metrology, microscopy and micromachining.
Vibration Detection and Compensation
Active vibration isolators first detect any vibrations using integrated acceleration sensors. The countermotions required for compensation are generated by piezo actuators, which are controlled by a real-time digital signal processor. It provides the computer power required for carrying out the extremely fast calculations for vibration compensation.
Piezo Actuators: Fast, Strong, Accurate
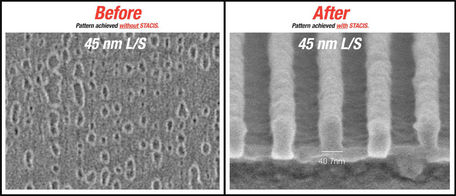
Due to their specific characteristics, piezo actuators offer the best conditions for use in isolators: They work with response times of a few milliseconds and resolutions in the subnanometer range. At the same time they can reach high accelerations of more than 10,000 g and allow loads of up to several tons to be moved.
Since the piezo effect is based on electric fields, piezo actuators do not produce magnetic fields nor are they affected by them. Varying ambient temperatures do not impair piezo actuators, which do not exhibit any mechanical wear either, since their motion is based on crystalline solid-state effects.