Products - PI (Physik Instrumente) L.P.
Precision Gantry provides XYZ Motion
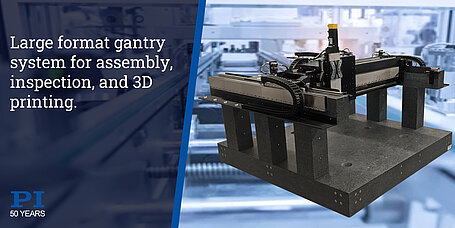
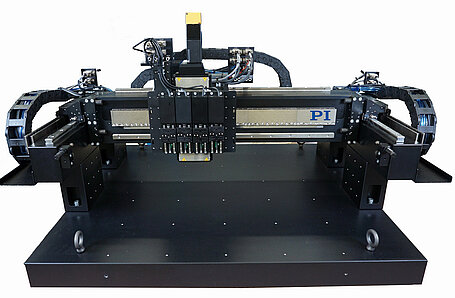
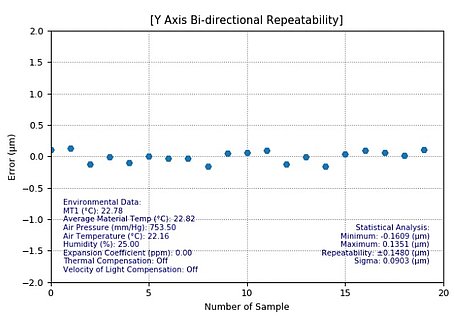
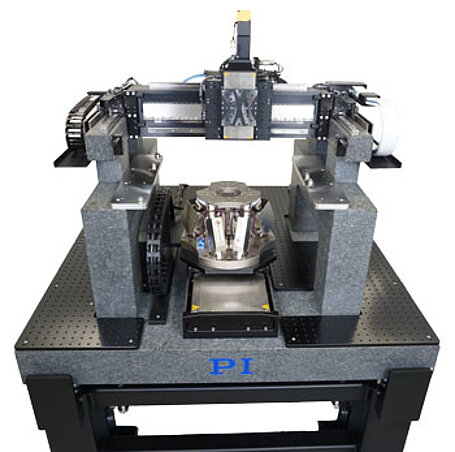
Why Use Precision Gantry Systems?
Industrial precision gantries are designed for multi-axis operation where typically two parallel linear motion modules move a cross axis (gantry axis). These designs are called Gantry Systems or Gantry Stages. When the work piece cannot be moved, is large or must be processed from the top, a precision gantry stage is a better solution than a traditional XY or XYZ positioning stage.
Gantry motion systems most often find applications in automated optical inspection (AOI), 3D printing, scanning, digital industrial printing, flat panel processing, electronics manufacturing, laser processing, and PCB drilling.
What Motors are Used in Gantries for XY and XYZ Motion?
There are different types of motors and drive systems, but for industrial, high dynamic, 24/7 applications, direct-drive linear motors are best suited because of their high dynamics, reliability, and robustness (no need for maintenance, no wear). Closed-loop, direct-drive linear motors with linear encoders are far superior in this respect to low-cost gantries based on ball-screw or leadscrew drives and rotary stepper or servo motors.
PI provides a number of standard integrated-construction gantry types with granite or AL bases and works with customers on modifications to provide the exact solution for their needs. All basic gantries provide XY motion, and XYZ motion can be achieved by adding a Z-Axis stage on the cross axis. PI provides air bearing Z-stages with linear motors and pneumatic counterbalance, voice-coil stages with magnetic counterbalance, and servo motor stages with ball screws.
EtherCat Motion Controllers Improve Synchronization of All Components
All PI gantry stage systems are based on closed-loop brushless linear servo motors for the highest possible performance for applications like precision assembly, micromachining, inspection, flat panel processing, and more. They also use motion controllers based on the EtherCat industry standard, that allows high throughput data exchange for perfect synchronization with all motion axes and 3rd party equipment such as cameras, lasers, galvos, dispensers, etc. for the highest overall system performance and accuracy.
Based on the success of the mid-motion range A-351 XY / XYZ stage gantry and the unique A-341 air bearing hybrid gantry, PI now introduces the new A-352 gantry XY / XYZ stage series with travel ranges up to 2 meters.
- Overhead moving XY gantry w/ Z-option
- Long travel ranges, to 1m x 2m
- Precision recirculating ball bearing guides
- Absolute measuring linear encoders
- Sub-micrometer precision
- High-performance, high speed ironless, brushless linear motors
- Various travel ranges. Options and customized adaptations
- Flexible modular platform
- Precision Z-stages with air bearings, voice coil or servo-motor / ball screw drives and brake option
- Full cable management for all stages and customer applications
- Extremely high-performance motion, accuracy, orthogonality, flatness and repeatability
Absolute Measuring Linear Encoders Improve Performance and Up Time
PI’s controller design allows for the use of advanced absolute linear encoders which not only increases accuracy but also improves the uptime, reduces the chances of missing encoder counts, and eliminates the need for homing procedures. Due to the advanced motion controller and the use of ironless linear motors, there is no influence on the motion uniformity by so-called cogging, leading to improved velocity stability. Advanced motion algorithms in PI’s high-performance motion controller and the use of the EtherCat communication protocol facilitate integration with factory automation systems, another plus for system integrators and machine builders.
Additional Information: