P-730, P-731 XY Nanopositioning Stage with Piezo Drive and Flexure Guidance - NanoPositioners and Scanners
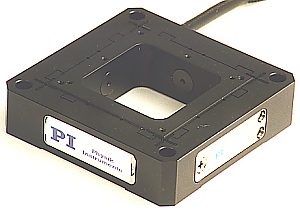
- Precision Trajectory Control
- For XY Scanning & Positioning
- 80 x 80 µm & 40 x 40 µm Versions
- Resolution < 1 Nanometer
- 50 x 50 mm Clear Aperture
P-730 and P-731 high speed nanopositioning stages are piezo driven and flexure guided. Flexure Translation Stages are fast and highly accurate low profile, XY scanning and positioning systems. These two-axis, high precision linear stages provide a positioning and scanning range up to 80 x 80 µm (using an integrated flexure piezo amplifier) with sub-nanometer resolution. Closed-loop capacitive feedback sensor equipped versions are offered for highest accuracy, precision and repeatability in the nanometer and sub-nanometer range.
The 50 x 50 mm clear aperture is ideal for transmitted light applications such as near-field scanning microscopy, confocal microscopy or mask alignment in semiconductor applications. P-730 and P-731 2-axis precision positioning stages are designed for applications with loads up to 2 kg.
Application Examples
Scanning microscopy, semiconductor test equipment, precision mask and wafer alignment, scanning interferometry, surface structure analysis, bio-technology, micromanipulation and other applications where single plane, high precision X-Y motion is required
More on Long Travel High Precision Motorized XY Translation Stages
Working Principle
P-730 and P-731 piezo nanopositioners are equipped with ultra-high reliability multilayer amplified piezo drives (and direct drives) integrated into a sophisticated flexure guiding system. The force exerted by the piezo drive pushes a multi-flexure parallelogram via an integrated motion amplifier. The wire EDM (Electric Discharge Machining) cut flexures are FEA (Finite Element Analysis) modeled for zero stiction/friction, ultra-high resolution and exceptional guiding precision. Integrated capacitive position feedback sensors provide sub-nanometer resolution and stability in closed loop operation (with PI electronics).
Ordering Information:
P-730.40 High Speed, XY Piezo Nanopositioning Flexure Stage, 40 x 40 µm
P-730.4L High Speed, XY Piezo Nanopositioning, 40 x 40 µm, Closed-Loop, LVDT Sensor
P-730.4C High Speed, XY Nanopositioning, 40 x 40 µm, Closed-Loop, Capacitive Sensor
P-731.80 XY PZT Flexure Stage, Amplified Piezo, 80 x 80 µm
P-731.8L XY PZT Flexure Stage, 80 x 80 µm, Closed-Loop, LVDT Sensor
P-731.8C XY PZT Flexure Stage, 80 x 80 µm, Closed-Loop, Capacitive Sensor
TECHNICAL DATA: | ||||||||
Models | P-730.40 | P-730.4L | P-730.4C | P-731.80 | P-731.8L | P-731.8C | Units | Notes |
Active axes | X,Y | X,Y | X,Y | X,Y | X,Y | X,Y | ||
Open loop travel @ 0 to 100 V | 40 x 40 | 40 x 40 | 40 x 40 | 80 x 80 | 80 x 80 | 80 x 80 | µm ± 20 % | A2 |
Closed loop travel › | - | 40 x 40 | 40 x 40 | - | 80 x 80 | 80 x 80 | µm | A5 |
Integrated feedback sensor | - | 2 x LVDT | 2 x Capacitive | - | 2 x LVDT | 2 x Capacitive | B | |
Closed / open loop ** | - / 0.5 | 10 / 0.5 | 0.5 / 0.5 | - / 1 | 10 / 1 | 1 / 1 | nm | C1 |
Closed loop linearity (typ.) | - | 0.1 | 0.03 | - | 0.1 | 0.03 | % | |
Full range repeatability (typ.) | - | ±20 | ±3 | - | ±20 | ±5 | nm | C3 |
Stiffness | 3 | 3 | 3 | 3 | 3 | 3 | N/µm ± 20 % | D1 |
Push/pull force capacity | 300 / 100 | 300 / 100 | 300 / 100 | 300 / 100 | 300 / 100 | 300 / 100 | N | D3 |
Max. (+/-) normal load | 2 | 2 | 2 | 2 | 2 | 2 | kg | D4 |
Tilt (θ X/θ Y) (typ.) | 25/25 | 25/25 | 25/25 | 25/25 | 25/25 | 25/25 | µrad | E1 |
Electrical capacitance | 1.8 / axis | 1.8 / axis | 1.8 / axis | 7.2 / axis | 7.2 / axis | 7.2 / axis | µF ± 20 % | F1 |
* Dynamic operating current coefficient (DOCC) | 4.5 / axis | 4.5 / axis | 4.5 / axis | 9 / axis | 9 / axis | 9 / axis | µA/(Hz x µm) | F2 |
Unloaded resonant frequency | 500 | 500 | 500 | 500 | 500 | 500 | Hz ± 20 % | G2 |
Resonant frequency @ 200 g load | 400 | 400 | 400 | 400 | 400 | 400 | Hz ± 20 % | G3 |
Resonant frequency @ 500 g load | 250 | 250 | 250 | 250 | 250 | 250 | Hz ± 20 % | G3 |
Operating temperature range | - 20 to 80 | - 20 to 80 | - 20 to 80 | - 20 to 80 | - 20 to 80 | - 20 to 80 | ° C | H2 |
Voltage connection | 2 x VL | 2 x VL | 2 x VL | 2 x VL | 2 x VL | 2 x VL | J1 | |
Sensor connection | 2 x L | 4 x C | 2 x L | 4 x C | J2 | |||
Weight (with cables) | 550 | 580 | 580 | 550 | 580 | 580 | g ± 5 % | |
Body material | Al | Al | Al | Al | Al | Al | L | |
Recommended Amplifier/Controller | G, C | H, E | H, L, F | G, C | H, E | H, L, F | M |
* Dynamic Operating Current Coefficient in µA per Hertz and µm.
Example P-731: Sinusoidal scan of 30 µm at 10 Hz requires approximately 2.7 mA drive current.
** Noise equivalent motion with E-503 amplifier.
This is a legacy product that may have limited availability or may have been replaced. Ask a PI engineer for an equivalent new model.