Piezo Z and tip/tilt scanner; 12 µm linear travel range; 1200 µrad × 1200 µrad rotation range (θX × θY); SGS, indirect position measuring; LEMO LVPZT connectors; 2 m cable length
S-316 Piezo Z and Tip/Tilt Scanner
High Dynamics Piezo Scanner with Aperture
- Clear aperture 10 mm
- Tripod piezo drive
- Linear travel ranges to 12 µm (phase shifter)
- Sub-ms response time
- Sub-µrad resolution
- Closed-loop versions for increased precision
Application fields
- Image processing / stabilization
- Laser scanning / beam steering
- Laser tuning
- Optical filters / switches
- Beam stabilization
- Interferometry
Outstanding lifetime thanks to PICMA® piezo actuators
The PICMA® piezo actuators are all-ceramic insulated. This protects them against humidity and failure resulting from an increase in leakage current. PICMA® actuators offer an up to ten times longer lifetime than conventional polymer-insulated actuators. 100 billion cycles without a single failure are proven.
High guiding accuracy due to zero-play flexure guides
Flexure guides are free of maintenance, friction, and wear, and do not require lubrication. Their stiffness allows high load capacity and they are insensitive to shock and vibration. They work in a wide temperature range.
Automatic configuration and fast component exchange
Mechanics and controllers can be combined as required and exchanged quickly. All servo and linearization parameters are stored in the ID chip of the D-sub connector of the mechanics. The autocalibration function of the digital controllers uses this data each time the controller is switched on.
High dynamics multi-axis operation due to parallel kinematics
In a parallel-kinematic multi-axis system, all actuators act on a common platform. The minimum mass inertia and the identical design of all axes allow fast, dynamic, and nevertheless precision motion.
Specifications
Specifications
Motion | S-316.10 | S-316.10H | Tolerance |
---|---|---|---|
Active axes | Z ǀ θX ǀ θY | Z ǀ θX ǀ θY | |
Travel range in Z | 12 µm | 12 µm | |
Travel range in Z, open loop | 12 µm | 12 µm | +20 / -0 % |
Rotation range in θX | 1200 µrad | 1200 µrad | |
Rotation range in θY | 1200 µrad | 1200 µrad | |
Rotation range in θX, open loop | 1200 µrad | 1200 µrad | +20 / -0 % |
Rotation range in θY, open loop | 1200 µrad | 1200 µrad | +20 / -0 % |
Linearity error in Z | 0.2 % | 0.2 % | typ. |
Linearity error in θX | 0.2 % | 0.2 % | typ. |
Linearity error in θY | 0.2 % | 0.2 % | typ. |
Positioning | S-316.10 | S-316.10H | Tolerance |
Resolution in Z, open loop | 0.2 nm | 0.2 nm | typ. |
Resolution in θX, open loop | 0.05 µrad | 0.05 µrad | typ. |
Resolution in θY, open loop | 0.05 µrad | 0.05 µrad | typ. |
Integrated sensor | SGS, indirect position measuring | SGS, indirect position measuring | |
System resolution in Z | 0.4 nm | 0.4 nm | |
System resolution in θX | 0.1 µrad | 0.1 µrad | |
System resolution in θY | 0.1 µrad | 0.1 µrad | |
Drive Properties | S-316.10 | S-316.10H | Tolerance |
Drive type | PICMA® | PICMA® | |
Electrical capacitance in Z | 0.31 µF | 0.31 µF | ±20 % |
Electrical capacitance in θX | 0.31 µF | 0.31 µF | ±20 % |
Electrical capacitance in θY | 0.31 µF | 0.31 µF | ±20 % |
Mechanical Properties | S-316.10 | S-316.10H | Tolerance |
Stiffness in Z | 10 N/µm | 10 N/µm | ±20 % |
Resonant frequency in X, under load with glass mirror (Ø 15 mm; thickness 4 mm) | 4.1 kHz | 4.1 kHz | ±20 % |
Resonant frequency in X, under load with glass mirror (Ø 20 mm; thickness 4 mm) | 3.4 kHz | 3.4 kHz | ±20 % |
Resonant frequency in Z, unloaded | 5.5 kHz | 5.5 kHz | ±20 % |
Resonant frequency in Z, under load with glass mirror (Ø 15 mm; thickness 4 mm) | 4.1 kHz | 4.1 kHz | ±20 % |
Resonant frequency in Z, under load with glass mirror (Ø 20 mm; thickness 4 mm) | 3.4 kHz | 3.4 kHz | ±20 % |
Moment of inertia in θX, unloaded | 150 g·mm² | 150 g·mm² | ±20 % |
Moment of inertia in θY, unloaded | 150 g·mm² | 150 g·mm² | ±20 % |
Distance of pivot point to platform surface | 5 mm | 5 mm | ±0,5 mm |
Guide | Flexure guide with lever amplification | Flexure guide with lever amplification | |
Overall mass | 55 g | 55 g | ±5 % |
Material | Steel | Steel | |
Miscellaneous | S-316.10 | S-316.10H | Tolerance |
Operating temperature range | -20 to 80 °C | -20 to 80 °C | |
Connector | LEMO LVPZT | D-sub 37 (m) | |
Sensor connector | LEMO for strain gauge sensors | — | |
Cable length | 2 m | 2 m | +100 / -0 mm |
Recommended controllers / drivers | E-503, E-505, E-509, E-610, E-625 | E-727 |
The resolution of the system is limited only by the noise of the amplifier and the measuring technology because PI piezo nanopositioning systems are free of friction.
Mechanical tilt, optical beam deflection is twice as large. For maximum tilt range, all three piezo actuators must be biased at 50 V. Due to the parallel-kinematics design, linear travel and tip/tilt angle are interdependent. The specified values are the maximum for pure linear respectively tilt motion.
At PI, technical data is specified at 22 ±3 °C. Unless otherwise stated, the values are for unloaded conditions. Some properties are interdependent. The designation "typ." indicates a statistical average for a property; it does not indicate a guaranteed value for every product supplied. During the final inspection of a product, only selected properties are analyzed, not all. Please note that some product characteristics may deteriorate with increasing operating time.
Downloads
Product Note
Product Change Notification Piezo Actuator Driven Products
Datasheet
Documentation
User Manual S310T0001
S-310, S-311, S-314, S-315, S-316 Piezo Z / Tip / Tilt Scanner
3D Models
S-316 3-D model
Ask for a free quote on quantities required, prices, and lead times or describe your desired modification.
Piezo Z and tip/tilt scanner; 12 µm linear travel range; 1200 µrad × 1200 µrad rotation range (θX × θY); SGS, indirect position measuring; D-sub 37-pole (m) connector; 2 m cable length
How to Get a Quote
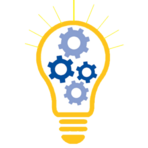
Questions? - Ask a PI Engineer
Technology
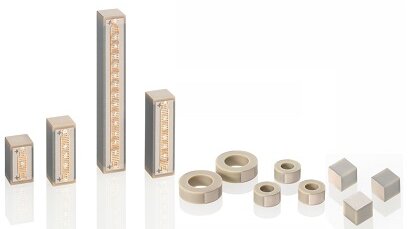
PICMA® Technology
Highly reliable and extended lifetime through the patented manufacturing process for multilayer actuators.
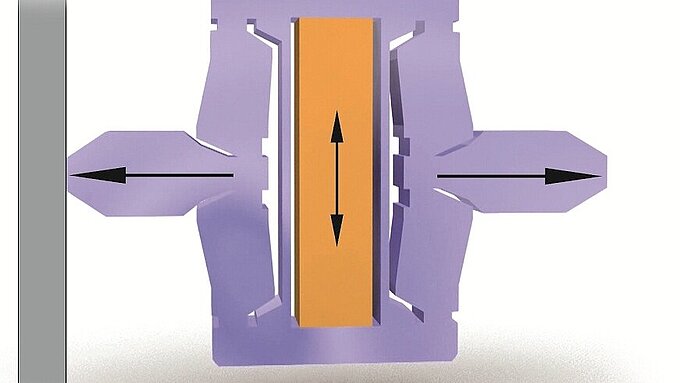
Flexure Guiding Systems
Flexure guides from PI have proven their worth in nanopositioning. They guide the piezo actuator and ensure a straight motion without tilting or lateral offset.
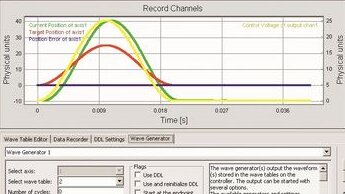
Digital Motion Controllers
Digital technology opens up possibilities for improving performance in control engineering which do not exist with conventional analog technology.
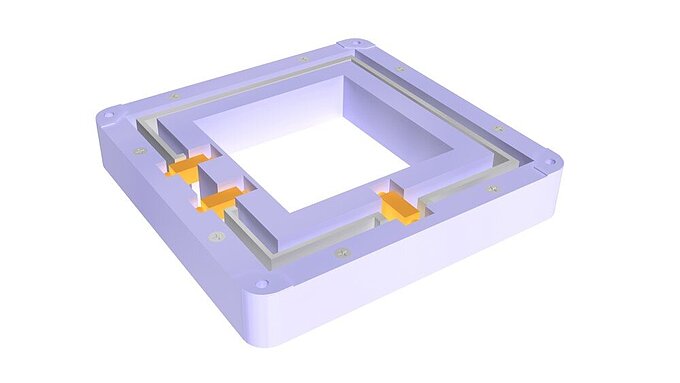
Piezo Positioning Systems with Parallel Kinematics
In a parallel-kinematic, multi-axis system, all actuators act directly on a single moving platform.