Piezoelectric high-speed motion improves performance of die-sinking EDM in the micron realm.
The basic principle of the machining process, now known as electrical discharge machining (EDM), or die sinking, was discovered in the 1940’s by accident, when Russian scientists were trying to prevent the erosion of electrical contacts caused by sparking. Today, EDM is well established for precision manufacturing of tools and lately, micro-structured components, even in large quantities. The process requires high voltage run between two electrodes causing the removal of metal from the workpiece by the discharge of electric current.
Adding Vibration to Speed-Up Die-Sinking EDM
The Institute for Microtechnology in Mainz (ICT-IMM), Germany put a new spin on this old technology. The Sonodrive 300 vibratory spindle uses a patented process to cut machining times, in high-precision micro-drilling operations, by up to 60%. The spindle rotates and vibrates simultaneously, preventing the particles produced by EDM from being deposited in the hole, eliminating the need for additional machining time.
Pictured left,the Sonodrive 300 serial-production vibratory spindle can cut machining times by up to 60%, in high-precision micro-drilling operations, employing a patented process. (Image: ICT-IMM)
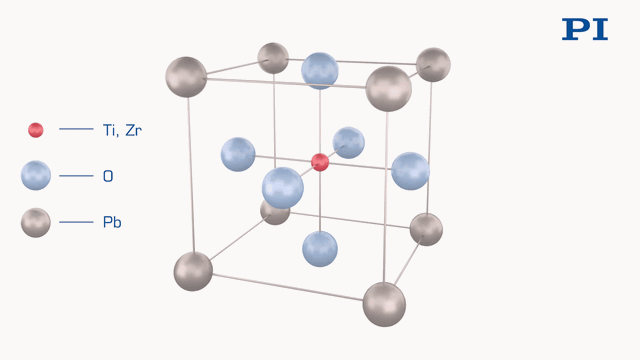
Shown to the left,an animation of piezo motion in PICMA multilayer low-voltage piezo stack: When an A/C voltage is applied to a piezo transducer, it will begin to oscillate, according to the applied voltage and frequency. Note: Typical amplitudes are on the order of 0.1% of the stack’s length. PICMA® piezo actuators survived 100 billion cycles of life-testing by NASA/JPL without failures (Image PI)
Compared with conventional methods, this process delivers substantial speed benefits because the small electrode distances do not allow any flushing in the micron range. The new spindle principle combines high concentricity tolerance of 1 to 2µm at speeds of up to 3,500 rpm with an oscillation of max. 300Hz at amplitudes up to 15 microns.
Piezoelectric Actuator Generates Precise High Speed Vibration
A piezoelectric transducer / actuator, designed by Physik Instrumente (PI), generates the vibratory motion. Piezo transducers are active ceramic elements that convert electric energy into mechanical energy. When an AC voltage is applied, the transducer starts to oscillate. The high stiffness and short response times of the electro-ceramic material (down to microseconds are feasible) benefits applications with fast motion requirements. Piezo actuated direct drives typically achieve displacements up to few hundred micrometers and high dynamics (flexure motion amplifiers are used for longer travels). With its low profile of only 25mm and Ø50mm OD / Ø25mm ID, the selected actuator facilitates integration in the vibratory spindle.
Solid-State Effects, NASA-Tested Technology
Piezoelectric motion is entirely based on solid-state effects; there is no wear and tear, no particulate generation and abrasion making the technology maintenance-free. In fact, NASA/JPL tested PI piezo actuators for the Mars mission, where they passed 100 billion cycles of life testing with zero failures.
Replacement Electrode Chuck for Commercial Die-Sinking EDM Machines
Piezoelectric transducers were also integrated in a vibration-supported electrode chuck, suitable as a “Plug & Play” solution for commercially available die-sinking EDM machines and clamping systems. A long-term experiment with a hard-metal electrode (0.2 x 5 mm) and a sinking depth of 7mm showed time savings of 70%. Likewise, the chuck generated vibrations of 300Hz with variable amplitudes up to 15 micrometers:
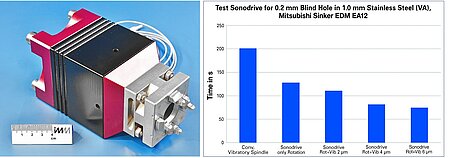
Blog Categories
- Aero-Space
- Air Bearing Stages, Components, Systems
- Astronomy
- Automation, Nano-Automation
- Beamline Instrumentation
- Bio-Medical
- Hexapods
- Imaging & Microscopy
- Laser Machining, Processing
- Linear Actuators
- Linear Motor, Positioning System
- Metrology
- Microscopy
- Motorized Precision Positioners
- Multi-Axis Motion
- Nanopositioning
- Photonics
- Piezo Actuators, Motors
- Piezo Mechanics
- Piezo Transducers / Sensors
- Precision Machining
- Semicon
- Software Tools
- UHV Positioning Stage
- Voice Coil Linear Actuator
- X-Ray Spectroscopy