Compact 6-Axis parallel precision manipulator with nanometer resolution helps the goal of designing a single universal instrument for the use in different full-field X-ray diffraction imaging methods.
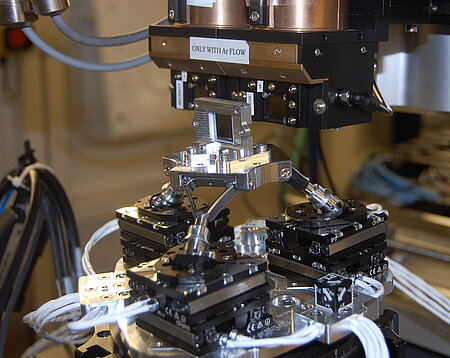
Modern methods of X-ray imaging allow micrometer accurate determination of crystal properties using diffraction contrast imaging methods. For example, the development of so-called diffraction laminography in recent years has made it possible for synchrotron sources to three-dimensionally image dislocations (line-type crystal defects of high technological relevance) in industrial semiconductor wafers and to investigate their formation and propagation [D. Hänschke et al, Three-dimensional imaging of dislocations by X-ray diffraction laminography, Appl. Phys. Lett. 101, 244103 (2012); D. Hänschke et al., Correlated Three-Dimensional Imaging of Dislocations: Insights into the Onset of Thermal Slip in Semiconductor Wafers, Phys. Rev. Lett. 119, 215504 (2017)].
The so-called “rocking curve imaging” allows a quantitative characterization of local crystal deformations (tilting, lattice spacing changes, defect densities) [D. Lübbert, μ-resolved high resolution X-ray diffraction imaging for semiconductor quality control, Nucl. Instrum. Methods Phys. Res. Sect. B 160, 521 (2000)].
With the aim of enabling the use of such different methods of full-field X-ray diffraction imaging with a single universal instrument, the Karlsruhe Institute of Technology (KIT) and the University of Freiburg are currently developing a mobile and flexible experimental setup in a joint project. The basic principle here is that a crystalline sample is first positioned in a highly parallel X-ray beam, then brought into Bragg condition by suitable tilting and finally, the image impressed on the diffracted beam profile is detected.
Depending on the exact type of measurement, the angle of attack should now also be varied with an accuracy of up to 0.001° and / or by rotating the sample, the viewing direction should be varied with a positioning error of less than 1μm. Decisive here is a correspondingly accurate and stable alignment of the sample (spatial and angular space!) relative to all involved axes. At the same time, the mass of the required multi-axis precision mechanism must be kept as low as possible to maintain the accuracy of the overall structure.
The system implemented here is a modified Q-845 miniature 6-axis parallel manipulator (SpaceFAB), manufactured by PI miCos, driven by closed-loop piezo inertia motors, equipped with nanometer resolution optical encoders. The low mass of only 1.9kg and the highly symmetric weight distribution aided by the basic design and the modified cable routing improves the overall system precision.
Author: Daniel Hänschke, KIT, Karlsruhe
Blog Categories
- Aero-Space
- Air Bearing Stages, Components, Systems
- Astronomy
- Automation, Nano-Automation
- Beamline Instrumentation
- Bio-Medical
- Hexapods
- Imaging & Microscopy
- Laser Machining, Processing
- Linear Actuators
- Linear Motor, Positioning System
- Metrology
- Microscopy
- Motorized Precision Positioners
- Multi-Axis Motion
- Nanopositioning
- Photonics
- Piezo Actuators, Motors
- Piezo Mechanics
- Piezo Transducers / Sensors
- Precision Machining
- Semicon
- Software Tools
- UHV Positioning Stage
- Voice Coil Linear Actuator
- X-Ray Spectroscopy