High Stability Positioning Stage with Self-Clamping Ceramic Linear Motors Provides Long-Term Nanoscale Stability
An insidious nanoscale instability process is the quasi-asymptotic settling due to lubricant flow processes in drive, alignment and adjustment elements such as lead-screws and micrometer drives. It has been thought that this progresses at the nanoscale over many minutes, but conventional position-metrology instrumentation is typically less stable than recent process tolerances over the timescales involved, so quantification of these issues has been lacking.
![Figure 1. Optical tweezers are a tool of single-molecule biophysics which allow quantitative measurement of position with sub-nanometer resolution and, in dual-trap configurations, commensurate long-term stability. (From Neuman, Block [2])](/fileadmin/user_upload/pi_us/img/blog_images/Optical-Trapping-PI.jpg)
Researchers in the field of single-molecule biophysics utilized optical tweezers [Figure 1] in a configuration that allowed quantitative comparison of the stabilities of screw-driven and piezomotor-driven stages with sub-nanometer sensitivity over many minutes [1]. As in many semiconductor-industry applications, the test setup stacks coarse-positioning (resolution 0.1 micron) and fine-positioning motion elements (resolution 0.1 nanometer) in a sophisticated microscopy configuration. By swapping the coarse-positioning stage between screw-driven and piezomotor-driven models, the long-term, nanoscale stability provided by the piezomotors was quantitatively revealed.
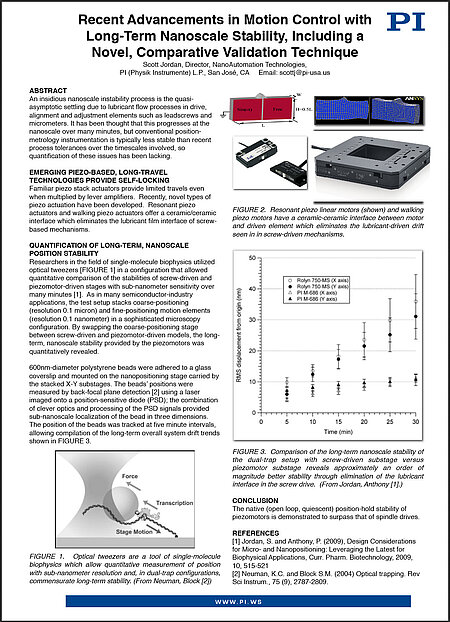
- Application abstract (PDF)
Blog Categories
- Aero-Space
- Air Bearing Stages, Components, Systems
- Astronomy
- Automation, Nano-Automation
- Beamline Instrumentation
- Bio-Medical
- Hexapods
- Imaging & Microscopy
- Laser Machining, Processing
- Linear Actuators
- Linear Motor, Positioning System
- Metrology
- Microscopy
- Motorized Precision Positioners
- Multi-Axis Motion
- Nanopositioning
- Photonics
- Piezo Actuators, Motors
- Piezo Mechanics
- Piezo Transducers / Sensors
- Precision Machining
- Semicon
- Software Tools
- UHV Positioning Stage
- Voice Coil Linear Actuator
- X-Ray Spectroscopy