High-performance motion and positioning platforms are complex systems categorized by many performance parameters. This complexity can easily lead to confusion when searching for the proper component for a particular application. Complicating the selection further is the abundance of seemingly overlapping terms used to describe independent technologies. The phrases "linear slide" and "linear stage," for example, are often used interchangeably. Although widely accepted in the motion control industry, this is technically incorrect.
In this article, PI aims to offer some guidance on the distinct motion control terminologies relating to linear slides and stages.
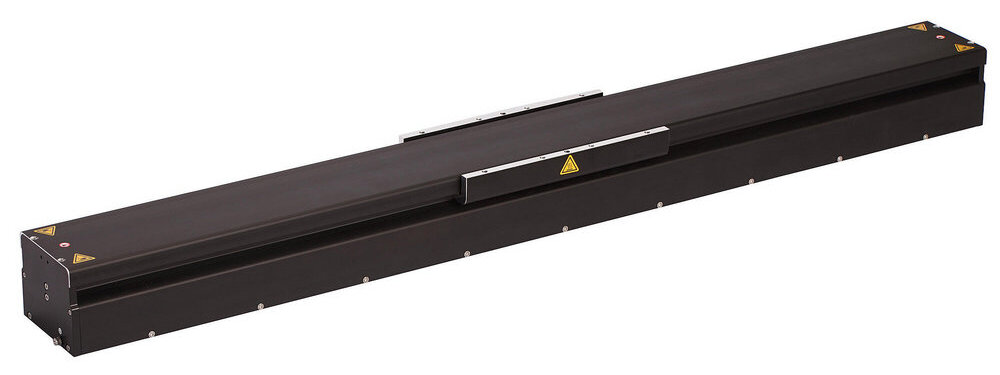
What is a Linear Slide?
A linear slide is a machine element within a motion platform that provides free motion across a single degree of freedom (X, Y or Z) and restricts undesirable movement across the other axes (including θ-X, θ-Y, θ-Z) as much as possible. “Slide” implies some kind of sliding motion, which seems at odds when ball or roller bearings are supporting the moving platform. In the most basic form of a linear slide, it may consist of only two parts: a base and a moving platform as shown in the dove-tail slide concept below.
There are no bearings between the base and the moving platform, which can be pushed around manually and could also be secured with the help of a locking mechanism. By adding a drive screw between the base and the platform, a motorized linear slide can be built. However, without any type of rolling elements (ball or roller bearings) between the base and moving platform, friction and wear can become a problem in addition to the limited guiding precision of these types of simple linear slides.
The term linear suggests that the slide can convey a motion platform or stage across its full range of available motion in a perfectly straight line. However, this is not strictly speaking true. As with all mechanical instruments and devices, margins of error do exist. Deviations from the desired axial motion in the context of high precision linear slides typically refers to unwanted movement in terms of travel flatness, straightness, pitch, roll, or yaw. These errors can be costly if not picked up in situ. Learn more on methods how to measure and reduce errors.
There is however one type of linear slide that uses no rolling elements and yet (or precisely for that reason) provides extremely high guiding precision: Air bearing slides. By controlling surface tolerances between the base and moving platform to the micron level and filling the gaps with pressurized air, the moving platform glides on an air film, never making contact with the base, leading to extremely straight, frictionless motion with no wearing parts.
In addition to the dovetail and air bearings discussed above, various other linear slide technologies exist today, including plain bearings, compound, and rack slides.
What is a Linear Stage?
Although often used synonymously with the phrase “linear slide”, the term “linear stage” is used mostly, when higher accuracy motorized positioners with precision bearings are referred to. Another variation for “linear stage” is “translation stage” and sometimes even the combination of both - “linear translation stage” - whereas “translation slide” is not common. The definition of translation comes from mathematics and defines the motion of a shape without rotating or flipping it.
Many different types of guide systems are used in linear stages, including ball bearings, crossed-roller bearings, air bearings, flexures (short travel) and even magnetic bearings such as those used in MagLev stages, each of which must be accompanied by a motor/actuator and position sensor/encoder to perform computer controllable accurate translation.
Linear stages are available for vertical, or lift, positioning, XY motion, and multi-axial positional control for a variety of applications.
What is a Linear Table?
The term linear table, is often used for XY positioning as XY table. Table in the context of motion control sometimes (but not always) refers to less precise positioning equipment, for higher load requirements. XY-positioning tables can be constructed of two or more linear slides modular or integrated into a single device to achieve all-in-one linear motion control across both horizontal axes – a principle of operation that is similar to the mechanisms of XY gantries.
PI: Global Supplier of Precision Motion Technology
PI is a world leader in the design and supply of precision motion control and positioning technology for high end instrumentation and analytical applications. We provide unique solutions for your business needs, offering a choice of products from the cost-effective to the ultra-precise.
If you would like to do some further reading on the subject of precision motion and positioning techniques, we provided a comprehensive deep dive into the subject in our previous post: What is a Motion Platform?
Alternatively, contact a member of the PI team today for more information about our linear slides, stages, and other translation technologies.
Blog Categories
- Aero-Space
- Air Bearing Stages, Components, Systems
- Astronomy
- Automation, Nano-Automation
- Beamline Instrumentation
- Bio-Medical
- Hexapods
- Imaging & Microscopy
- Laser Machining, Processing
- Linear Actuators
- Linear Motor, Positioning System
- Metrology
- Microscopy
- Motorized Precision Positioners
- Multi-Axis Motion
- Nanopositioning
- Photonics
- Piezo Actuators, Motors
- Piezo Mechanics
- Piezo Transducers / Sensors
- Precision Machining
- Semicon
- Software Tools
- UHV Positioning Stage
- Voice Coil Linear Actuator
- X-Ray Spectroscopy