More than 80 years ago, a discovery by Austrian Kurt Gödel put an end to the dream mathematicians had pursued for centuries: a final unifying “Theory of Everything” or the idea that a system could be devised strong enough to verify itself. Gödel’s findings may seem rather obvious, but they had an enormous impact on all branches of science and today are widely considered as important as Einstein’s Theory of Relativity.
What has become known as the “Incompleteness Theorem” asserts that no statement can prove its own truth. One of the well-known analogies is that no one can lift themselves up in the air by their own bootstraps, no matter how hard they pull.
What It Means for Test and Measurement
Verification of the positional stability/drift, accuracy, and position resolution of a closed-loop positioning system requires an independent sensor (of higher accuracy). In the nanopositioning world, the most credible results come from a standards-traceable instrument, such as a laser interferometer because it measures distance directly using the wavelength of light. Good laser interferometers are expensive and the setup requires trained technicians and a stable, vibration and temperature controlled environment.
Cheap and Flattering Shortcuts
The above may be the reason that cheap and flattering (but flawed) short-cuts are sometimes proposed. One such “solution” excites a vibration in the positioner and uses its internal sensor to infer its positional resolution (from the frequency spectrum), instead of measuring the actual stage position with an independent external sensor.
This method violates the fundamentals of measuring technology (one sensor cannot verify its own capabilities). By switching from the time domain to the frequency domain, the results become less applicable to nanopositioning and could conceivably be used to prove anything.If conducted with a precise external sensor, frequency domain measurements would allow the accurate comparison of positioning systems based on their ability to reproduce certain frequencies. While essential for characterizing HIFI speakers, the method does not really apply to precision positioning equipment.
How Nanopositioning Stages are Used
Nanopositioning stages, especially if piezo-driven are typically operated in one of three ways: point to point motion, scanning, or tracking. In all three cases, the motion of the stage is expected to be in a certain place at a certain time. The correlation of position and time is very important. For example in imaging applications, the data gathered along the way is later easily reconstructed into an image by matching the data point with the position at a given time. This is why position vs. time (time domain) measurements can say more about the qualities of a nanopositioning system than other tests. In addition to graphically showing system behavior when it comes to reproducing nanometer-sized steps, they also indicate stability (ability to hold position over time), settling time, overshoot, and repeatability.
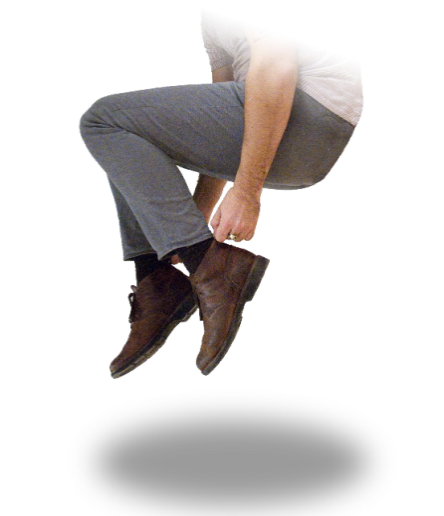
Frequency domain measurements (FFT analysis) are useful to characterize system resonances. Frequency domain information, however, offers no time / position correlation. Again, for meaningful results, measurements need to rely on independent external metrology, such as laser vibrometry.
Defining Resolution in Positioning Systems with Non-Incremental Actuators and Sensors
Because of the analog nature of the amplifiers and sensors usually employed in closed-loop piezo positioners, resolution is not determined by discrete steps (as is typical with stepper motors or incremental encoders), making it theoretically infinite. In reality, there is always micro friction to be considered and sensor and control-electronics noise also have an impact on the practically usable resolution. For typical imaging, positioning, and alignment applications, the practically usable resolution is 1σ the independently-measured positional noise, or ~1/6 of the peak-peak noise. As stated above, in addition to this statistical figure, the graphical data of nanometer sized discrete steps performed by the positioner reveals a great deal of information on system response, stability, and repeatability and is directly applicable to the way nanopositioning systems are used.
Blog Categories
- Aero-Space
- Air Bearing Stages, Components, Systems
- Astronomy
- Automation, Nano-Automation
- Beamline Instrumentation
- Bio-Medical
- Hexapods
- Imaging & Microscopy
- Laser Machining, Processing
- Linear Actuators
- Linear Motor, Positioning System
- Metrology
- Microscopy
- Motorized Precision Positioners
- Multi-Axis Motion
- Nanopositioning
- Photonics
- Piezo Actuators, Motors
- Piezo Mechanics
- Piezo Transducers / Sensors
- Precision Machining
- Semicon
- Software Tools
- UHV Positioning Stage
- Voice Coil Linear Actuator
- X-Ray Spectroscopy