Complex patterned motion generation is becoming increasingly important for applications such as vehicular simulation and airborne platform simulation and test. However, many other emerging fields of structural and active mechanical subsystem analysis, validation, and design can also benefit from flexible, six-degree-of-freedom motion simulator mechanisms capable of generating specific motion patterns in real time.
Previously, mechanical shakers or generic stacks of positioning stages could sometimes be deployed to simulate simple target motions or approximate a desired mechanical stimulus, but these were inflexible and limited in their capabilities.
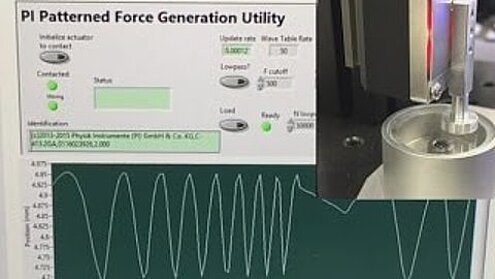
Now, a family of high-dynamic hexapods is available together with a broad and deep software toolkit for rapid development of patterned motion generation from the developmental laboratory to the production floor.
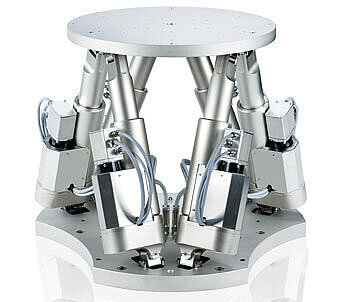
Example deployments range from simulation and compensation of physiological motions to calibrated oscillation of mechanisms for volume production validation. Applications include:
- Calibration and production test of active elements for volume consumer products
- Simulation of hand tremors and vehicular motions for imaging subsystem design and validation
- Simulation of patient and organ motions for medical systems development
- Active compensation of motions, disturbances, and physiological processes in the field
- Simulation of motion in airborne platforms
For example, the Camera and Imaging Product Association (CIPA) – an international alliance of camera manufacturers similar to an ISO committee – established standards for the test and evaluation of image stabilization systems. DC-011-2015 is its latest standard for motion simulation test conditions and several hexapods are certified by this standard.
Hexapods are ideal for the above listed uses thanks to their signature capability for six-degree-of-freedom motions in a user-defined coordinate system that places the rotational centerpoint at a desired position in space.
These advanced hexapods’ coordinate system’s origin and orientation can similarly be cast anywhere in space, rather than being fixed by the mechanical configuration of the system. Their controller’s built-in waveform generation is now capable of internal generation of millions of target positions at speeds of up to thousands of points/sec, addressing aliasing and generation artifacts. These capabilities are backed up by extraordinarily fast TCP/IP Ethernet interfaces, together with responsive RS-232 and standard, real-time TTL synchronization interfaces, plus available analog inputs and SPI, EtherCAT, and RS-422 interfaces. Two auxiliary motion axes are now standard as well for driving linear or rotary DC servo stages or actuators.
The family ranges from the cost-effective, high-speed H-840 hexapod for higher loads, to the compact, production-class H-811 with its long-life brushless DC servo motors, to the unique H-860KMAG hexapod with its wear-free, high-dynamic voice-coil drives and flexure guidance— ideal for 24/7 production deployments.
Software tools offer rapid application development across Windows, OS X, and Linux operating systems — and more. Dynamic libraries make for quick and productive programming in any language, while a simple, mnemonic ASCII command set makes for quick work in terminals or any scripting environment. An extensive, well-wrung-out, cross-platform-compatible LabVIEW library facilitates development of detailed and intuitive user interfaces on that platform as well. An example application offers especially easy-to-use multi-axis arbitrary waveform generation, including independently selectable sine, square, triangle, sawtooth, and swept-sine actuation, or the ability to import custom or proprietary position-vs-time tables in spreadsheet format.
Blog Categories
- Aero-Space
- Air Bearing Stages, Components, Systems
- Astronomy
- Automation, Nano-Automation
- Beamline Instrumentation
- Bio-Medical
- Hexapods
- Imaging & Microscopy
- Laser Machining, Processing
- Linear Actuators
- Linear Motor, Positioning System
- Metrology
- Microscopy
- Motorized Precision Positioners
- Multi-Axis Motion
- Nanopositioning
- Photonics
- Piezo Actuators, Motors
- Piezo Mechanics
- Piezo Transducers / Sensors
- Precision Machining
- Semicon
- Software Tools
- UHV Positioning Stage
- Voice Coil Linear Actuator
- X-Ray Spectroscopy