Advances in Precision Positioning Stage Design-Optimized Outgassing and Motion Performance in Ultra-High Vacuum Applications
Many processes in advanced research and industrial manufacturing can only be performed in a vacuum, such as thin-film sputtering and ion milling, and technologies formerly reserved for exotic materials processing are seeing application in new fields. And of course the march of Moore’s Law means new types of equipment have been developed that impose vacuum requirements in systems where none existed before, for example as EHUV reticle illumination supplants previous technologies.
Specialized motion control products constructed for safe operation in vacuum provide critical performance for today’s demanding vacuum applications in markets such as semiconductor manufacturing and inspection, fabrication, aerospace, life sciences, medical, nanotechnology, pharmaceuticals, photonics, telecommunications, semiconductors, astronomy and microscopy. Key attributes of these systems include materials and assembly details selected for use in vacuum, motor and electronic subassemblies with appropriate material and heat performance, bake-out compatibility, and clean preparation and shipping practices that avoid contamination.
Different Vacuum Levels
A vacuum is defined as pressure lower than normal atmospheric air pressure. According to DIN28400-1:1900-5, the following are the specified vacuum ranges:
- Low Vacuum (FV): Pressure range <1 – 1-10-3 hPa
- High Vacuum (HV): Pressure range <1×10-3 – 10-7 hPa
- Ultra-High Vacuum (UHV): Pressure range <1×10-7 – 1×10-9 hPa
- Ultra-High Vacuum Grease (UHV-G): Pressure range <1×10-7 – 1×10-9 hPa
- Ultra-High Vacuum Cryo (UHV-C): Pressure range up to 1×10-9 hPa
- Extreme Ultra-High Vacuum (EUHV): Pressure range <1×10-9 – 1×10-11 hPa
When specifying equipment for use in a required vacuum level it is important to work with a cognizant supplier who can help analyze the application and ensure no details are overlooked. With ultra-high vacuums (UHV) for example, the following factors influence product suitability:
- Lubricant- choice, reduction or elimination
- Surface area minimization, including elimination of rough or micro-cavitated coatings and finishes;
- Depending on the application, suitability for operation in magnetic fields, radiation resistance (particle-radiation, X-ray radiation, EUHV); or suitability for operation in a cryogenic environment at -269 to 40 °C;
- Particular process sensitivity to specific trace species;
- Pump capacity and bake-out practices.
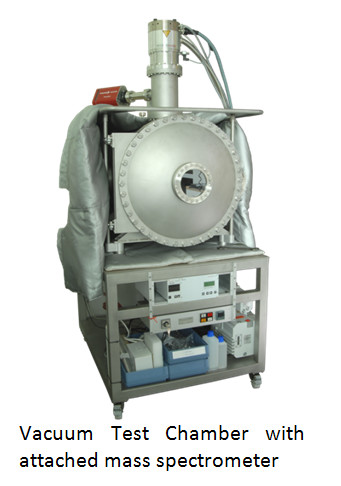
Engineering a System Solution for Ultra High Vacuum (UHV)
UHV is characterized by pressures lower than about 10−7 Pascal or 100 nanopascals (10−9mbar, ~10−9 Torr). To achieve the goal of an optimized, reliable UHV positioning system, electrical and electronic equipment like motors, position feedback sensors and limit/home switches have to be suitable for the specified environment, including such details as UV illumination and electromagnetic field compatibility. But other critical factors must be considered, such as material selection, positioning system design, outgassing, thermal management, and cleaning and assembly. Vacuum-facing components should undergo a three-stage cleaning process. The initial and key step as practiced by knowledgeable suppliers is an ultrasonic cleaning. Second, the components are dried in a climate cabinet under a nitrogen atmosphere. Third, assembling of the stage should be done in cleanroom or in a flow box. The system should then be packed in vacuum sealed bags, and protected against dirt, air and humidity, prior to shipping to the customer’s site.

Material Selection
Requirements for a vacuum-compatible material include:
- No particle emission
- No outgassing
- Bakeable and temperature resistant
This means the choice of materials for the body of any vacuum-compatible product is limited. For example, CuZn alloys cannot be used in vacuum systems, and standard plastic parts must be exchanged with PEEK (polyether ether ketone) or metal components to eliminate outgassing of organic contaminants. Preferred materials for vacuum positioning systems are stainless steel, titanium, bronze, aluminum, ceramic, sapphire, Viton, Teflon, PEEK, Kapton and Macor.
For vacuum-compatible precision positioning stages, suitable materials are aluminum alloys, stainless steel or titanium. Surface treatment is adapted to the vacuum class; for example, the surfaces of the higher vacuum classes are not coated but electro-polished. Anodizing of parts is routinely eliminated, since its intricate cavitation of the surface on a microscopic scale can increase the effective surface area of the part by a factor of six, and the dyes used to color ordinary parts can generate significant outgassing.
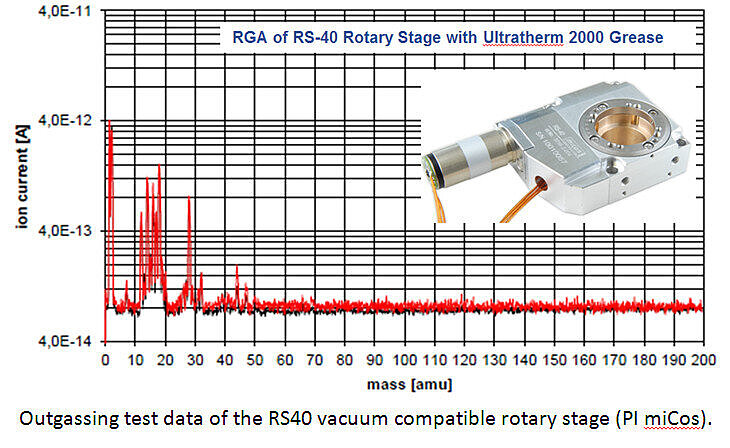
Vacuum Pressure vs Residual Materials
The pressure level alone is not the only critical parameter. Crystallography and optical coating manufacturing have different requirements not only with regard to overall chamber pressure but also regarding specific residual materials in the vacuum chamber. Frequently, the partial pressure of carbon hydrides is decisive. As part of lubricants and plastics, these hydrocarbons can be a source of contamination of surfaces. This is especially damaging in laser applications in the UV range, because the hydrocarbons can be split into reactive fragments which subsequently can deposit on optics. Using a chamber with a connected mass spectrometer enables verification of the suitability of possible materials, but vigilant selection of components used in in-chamber subsystems is critical.
The general prohibition of ordinary plastics inside a vacuum chamber means conventional wiring (with its plastic insulation) cannot be used in vacuum-compatible motion hardware, either in external cables or in internal wiring. Cable management system construction and materials typically utilize Teflon insulated wires along with specialized electrical connectors that employ a variety of materials including PEEK. Other cable and connection options are available depending on the application requirements.
Positioning System Design
An experienced motion-control provider will dive deeply into all aspects of a vacuum application to ensure that all details are considered. For one thing, vacuum chambers offer limited space and therefore require a compact design. Electronic subsystems such as controllers and amplifiers will not survive vacuum use, so they must be placed outside the vacuum chamber, which requires consideration of feedthroughs and cabling design. Unavoidably, some electronic components such as motors, end and home switches, and encoder read-heads must reside in-chamber and must be specifically constructed for vacuum compatibility and suitable for the wide temperature variations encountered in in-chamber usage.
Beyond the basic choice of materials and surface finish, the body of a positioning stage must be assembled with a focus on eliminating trapped pockets of air. Trapped air pockets can gas out very slowly: these are called virtual leaks and can considerably delay or even make generating a stable vacuum impossible. Holes, as well as screws, need to be vented. The formation of pockets between surfaces when bolted together (such as when a structure with stiffening ribs is bolted to plate) must be avoided, or provisions for rapid evacuation of the pocket (such as a drilled vent) must be incorporated.
The selection of suitable components, especially the drive elements, is very important. In particular, it is critical to take heat generation during operation into account, as heat can only be dissipated with great difficulty under vacuum. Knowledge of the planned working cycles is therefore useful for selection. This allows advance testing of the heat behavior of the selected individual parts.
Vacuum-Compatible Motors
Motorization provides ready adjustability of in-chamber elements and allows scanning, seeking and patterned-motion operations to be performed. Depending on the application’s requirement for such things as absolute positioning accuracy, minimum incremental motion, bi-directional repeatability and in-position stability, the optimal type of motion system will be evident. It is crucial, then, to work with a motion subsystem provider with access to a broad and deep toolkit of motion technologies.
Stepper motors are a versatile type of magnetic motor that require no brushed commutation, a significant advantage for outgassing and motor lifetime in a vacuum application. They provide a native holding force and can be operated in many modes depending on application needs. Stepper-motor vacuum stages typically employ special two-phase stepper motors that operate reliably up to 10-9 hPa and eliminate vacuum-incompatible construction details common among everyday stepper motors. For example, two-phase stepper motors for vacuum operation typically utilize a stainless steel housing, actively heated up to 120° C for outgassing, and of course plastic and other incompatible elements are eliminated.
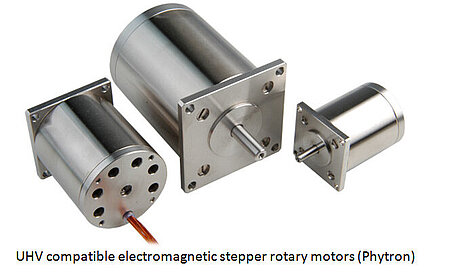
Other common types of motors are less suitable for in-chamber use. For example, brushed DC servo motors are usually a poor choice due to unavoidable brush arcing, which contributes to outgassing and can present hazardous current paths in the corona regime. Similarly, magnetic linear motors present significant heat-management problems in vacuum use and are typically avoided.
Reduction or elimination of lubricants means that in general, motorized vacuum stages offer lower velocities and a shorter service life than equivalent models configured for lab or fab use.
Piezoelectric technology offers another class of motion drive that is exceptionally well suited for vacuum use as a matter of principle, as piezo drive elements (and the flexure mechanisms in which they are often deployed) do not require any lubricants for operation. PI’s PICMA®piezo actuator, for example, shows controllable nanoscale displacements well into the cryogenic range, down to -271° C. This is an example of a piezoelectric nanopositioning stack, a ceramic structure formed by sintering thin layers of specialized ceramic between metallic electrodes. These actuators eliminate the vacuum-incompatible polymer insulation ordinarily applied to piezoelectric stacks, substituting an advanced ceramic encapsulation that is inherently vacuum-compatible. These stacks are at the heart of many ultra-precision applications like microlithography, as application of a voltage produces fast material expansion that can be precisely controlled well below the nanoscale, although travel ranges are necessarily small.
Piezo actuator single-axis and multi-axis scanning stages combine nanometer-precision resolution and guiding precision with minimum crosstalk. This makes them particularly suitable for reference applications in metrology, for microscopic processes, for interferometry or in inspection systems for semiconductor chip production.
Beyond the familiar piezoceramic stacks, piezoelectric ceramics have been configured in a variety of novel motor designs which eliminate the small-travel drawback. Some of these piezomotors provide many millimeters of travel yet retain the sub-nanometer position resolution for which piezoelectric stacks are renowned.
Regardless of the drive principle, all piezomotors can be configured for use in a vacuum environment with simple attention to details like wire insulation. Piezomotors can also be used in high-field applications like magnetic resonance imaging, because they do not generate magnetic fields nor are they affected by them. Piezomotors are an enabler in UHV, especially when radiation resistance and travel ranges in the millimeter range are required.
PiezoWalk® stepping drives are a type of piezomotor based exclusively on static friction contacts of several piezo actuators on a rod. For feed forward, the actuators are lifted physically from the rod, minimizing wear and abrasion. These drives have high resolution of less than one nanometer. Their small size makes them ideally suitable as drive systems for stages and actuators in a vacuum down to 10-9 hPa, allowing them to be used for 6-axis hexapod systems, such as specialized units constructed for high-field applications.
Multi-Axis Motion in a Vacuum
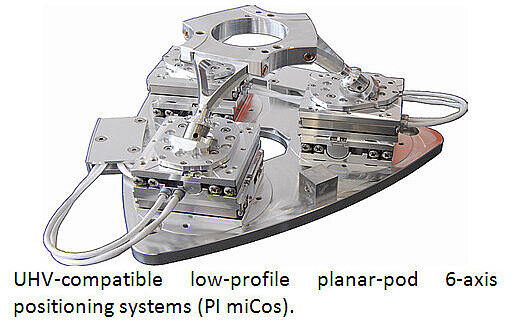
Multi-axis motion can be accomplished using classical stacks of individual linear and rotary stages (serial kinematics) or with a more compact and elegant parallel kinematics approach. Two basic designs are common: Hexapod positioners (Greek for “six-legged”) and planar parallel-positioners (SpaceFabs). Hexapods are also known as Stewart Gough platforms.
A particularly demanding application is low-temperature spectroscopy utilizing the ultra-short-wavelength probe beam provided by large synchrotron accelerators. These are the most brilliant light sources on the planet and are instrumental in delving ever deeper into the structural intricacies of micro-electronic materials and biological specimens. Often significant travels in multiple degrees of freedom are necessary. A popular approach to providing stable, high-resolution, 6-DOF positioning in these and other applications is the novel planar parallel positioner (SpaceFab) mechanism manufactured by PImiCos of Eschbach, Germany. These are tri-strut assemblies with fixed-length struts actuated in a common plane by three XY stacks of ultraprecision stages. This assembly provides long transverse travel in the XY plane together with precision adjustability in the three angular axes and Z via differential actuation of the stage stacks. A noteworthy capability of this mechanism is the option to place the rotation centerpoint anywhere in space, such as a focal point or other optical sweet spot. With this flexible, modular and extensible principle, a wide variety of motion technologies can be utilized, including UHV-compatible magnetic and piezo stepper motors.
Hexapods offer less planar XY travel than a SpaceFab but even higher stiffness, greater load capacity, larger angular range and a smaller surface area. Benefits in common with SpaceFab include the virtual rotational centerpoint. Some manufacturers integrate especially tidy cable management that eliminates moving/sweeping cables. An example is PI’s M-824 Vacuum hexapod, a 6-Axis micropositioning and alignment system which provides high resolution submicron motion in six degrees of freedom. It is designed to work in a vacuum and provides up to 45 mm (linear) and 25 degrees (rotation).
The greatest hexapod advantage is their compact size compared to conventional six-axis stage stacks, a fact that is especially beneficial in applications in vacuum chambers, where space is at a premium. Many have through-apertures as well, which facilitates optical designs. Typical applications focus on semiconductor technology, multi-axis alignment of optics, X-ray microscopy, and X-ray monochromators.
Thermal Management and Outgassing
Thermal management is key in vacuum systems because they cannot rely on convection or fans for the removal of heat from the motors, electronic subsystems and bearings. Without careful thermal management, stage performance, reliability and life can be reduced significantly. Development of thermal isolation methods and passive and active cooling techniques help to maximize conduction modes of cooling and reduce or eliminate heat sources inside the chamber.
Similarly, outgassing is a challenge to creating and maintaining clean high-vacuum environments. NASA maintains a list of low-outgassing materials (http://outgassing.nasa.gov) to be used for spacecraft, as outgassing products can condense onto optical elements, thermal radiators, or solar cells and obscure them. Materials not normally considered absorbent can release enough light-weight molecules to interfere with industrial or scientific vacuum processes. Even metals and glass can release gases from cracks or impurities, but moisture, sealants, lubricants, and adhesives are the most common sources. The rate of outgassing increases at higher temperatures because the vapor pressure and rate of chemical reaction increases. For most solid materials, the method of manufacture and preparation can reduce the level of outgassing significantly. Cleaning surfaces, or baking individual components or the entire assembly before use, can drive off volatiles.
Summary
Sophisticated, vacuum-compatible motion devices are increasingly being utilized by product designers and incorporated successfully into a widening range of ultra-high vacuum applications. These devices are compact, clean, stable, deliver high throughput, exhibit short response time, generate little heat, and are optionally nonmagnetic as well as vacuum compatible. They have few mechanical component parts to wear out and service.
Now, the latest vacuum-compatible motion control devices deliver an even broader product development capability for OEM designers of ultra-high vacuum systems. A key to application success is to partner with a motion equipment provider with a deep toolkit and experience across a variety of fields. This helps ensure that optimal and supportable in-chamber motion technologies are selected, and that lessons learned in parallel fields are leveraged.
Blog Categories
- Aero-Space
- Air Bearing Stages, Components, Systems
- Astronomy
- Automation, Nano-Automation
- Beamline Instrumentation
- Bio-Medical
- Hexapods
- Imaging & Microscopy
- Laser Machining, Processing
- Linear Actuators
- Linear Motor, Positioning System
- Metrology
- Microscopy
- Motorized Precision Positioners
- Multi-Axis Motion
- Nanopositioning
- Photonics
- Piezo Actuators, Motors
- Piezo Mechanics
- Piezo Transducers / Sensors
- Precision Machining
- Semicon
- Software Tools
- UHV Positioning Stage
- Voice Coil Linear Actuator
- X-Ray Spectroscopy