Hexapod 6-axis positioning system and motion platforms have traditionally been used in engineering, optics, and physics applications for their ability to provide precision motion in all degrees of freedom and flexibility based on a programmable center of rotation. As hexapods become more mainstream, applications expand into medical fields as well. Dental biomechanics deals with the interactions between dental materials, treatment instruments or dentures and the reaction of teeth, biological tissues, etc. to mechanical stresses. A wide spectrum of force systems occur here with masticatory forces exerting loads to 380 N and torques to several Nm.
At the same time, movements of several orders of magnitude are involved: orthodontic equipment can change the position of teeth by up to several mm, whereas —during mastication— teeth are deflected by less than 100 µm and implants by as little as a few microns or less. These combinations of small forces with large deflections on the one hand, and large forces and extremely small deflections on the other, represent a challenge with respect to the biomechanical metrology.
To deal with this challenge, the Dental Clinic of the University of Bonn designed the HexMeS (Hexa- pod Measuring System) based on PI’s M-850 high load hexapod 6-axis stage positioning system. The ability to move in all six axes in a highly stiff, small package, with resolutions of less than 1 µm (1 arcsec) was key reasons for choosing the hexapod motion system.
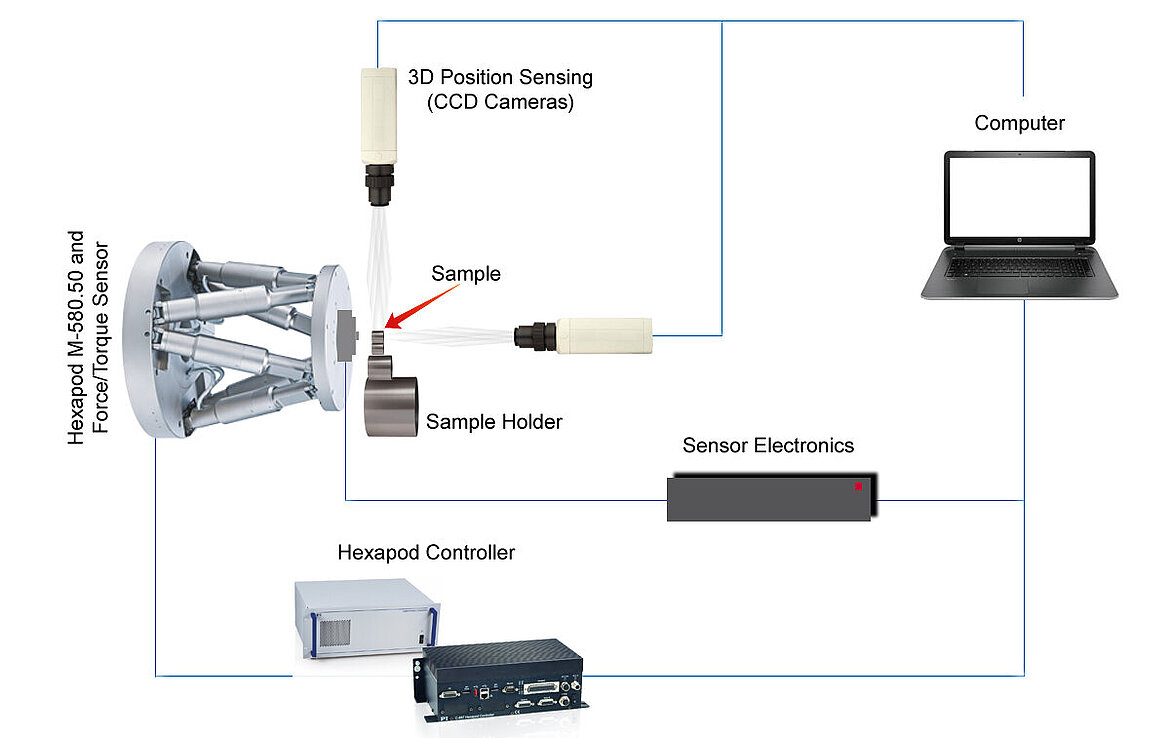
Because of the high hexapod stiffness of 100 N/µm, deflections can usually be calculated directly from the Hexapod motion. For high-load testing — simulations of mastication in the 100 N range — the optical sensor of the HexMeS is used, it provides resolution to 0.7 µm / 0.2 arcsec. The performance of the system has been tested with dental implants, telescope crowns, and orthodontic prostheses.
A recent paper on testing commercial short dental implants is available here.
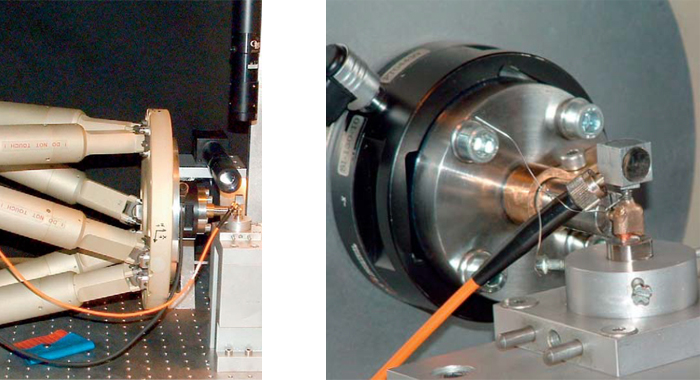
Additional research to improve simulation results has been carried out by scientists at the University of Ulm.
Here, the focus was the adaptation of orthodontic apparatuses, to better understand the response of a tooth (elastically embedded in the jaw bone) to forces and torques. The measurements cannot be done directly in vivo on the patient. FEA simulation alone did not provide a clear answer, because of too many unknowns – e.g. the biomechanical behavior of the connective tissue of the periodontal ligament (PDL).
Scientists from the University of Ulm tried a different approach using realistic simulations on a model. The result is a numerically controlled experimental setup that allows measurements of the clinically relevant forces acting on the tooth during the orthodontic tooth motion. In this way, FEA models can be checked and modified on the basis of real measurements.
Using a Hexapod with 6 degrees of freedom motion and a programmable center of rotation provides advantages for simulating the small motions of a tooth in the jawbone. For simulation, the Hexapod was combined with a force sensor mounted on a rigid rotary table. A phantom tooth (essentially an orthodontic bracket) is mounted directly at the sensor.
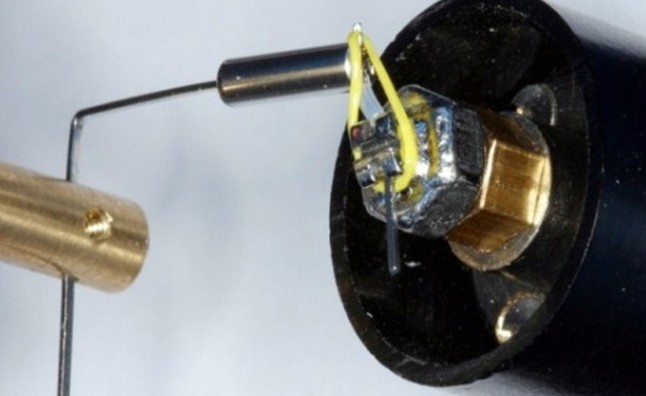
Thanks to the high stiffness and positioning accuracy of the hexapod, the force applied to the specimen can be exactly assigned to a position, allowing the stress points at the tooth to be determined.
The results obtained with the simulation model contribute to a better evaluation of orthodontic processes in the oral cavity and a more effective design of corrective measures. Similar results can also be achieved in other areas, for example in dental and hip implants or the like, using suitable test setups.
Blog Categories
- Aero-Space
- Air Bearing Stages, Components, Systems
- Astronomy
- Automation, Nano-Automation
- Beamline Instrumentation
- Bio-Medical
- Hexapods
- Imaging & Microscopy
- Laser Machining, Processing
- Linear Actuators
- Linear Motor, Positioning System
- Metrology
- Microscopy
- Motorized Precision Positioners
- Multi-Axis Motion
- Nanopositioning
- Photonics
- Piezo Actuators, Motors
- Piezo Mechanics
- Piezo Transducers / Sensors
- Precision Machining
- Semicon
- Software Tools
- UHV Positioning Stage
- Voice Coil Linear Actuator
- X-Ray Spectroscopy