EtherCAT®: Ethernet for Control Automation Technology and its Advantages for Precision Motion Systems
The fastest Industrial Ethernet-based fieldbus system keeps gaining popularity for a variety of reasons.
EtherCAT® is a modern, cost efficient, open real-time Ethernet-based fieldbus system. It is a registered trademark and patented technology, licensed by Beckhoff Automation GmbH, Germany. EtherCAT is short for “Ethernet for Control Automation Technology” and is used by control and system engineers as a robust, high-speed, real-time network for machine control solutions. The flexibility of the fieldbus system and the precise synchronization of all network devices help EtherCAT to gain popularity on a global base.
Real-time networks are characterized by
- High degree of reliability
- Very precise timing
- Deterministic behavior with guaranteed response times
Precision automation applications and cutting edge machine control solutions require fast data update rates, or cycle times ≤100µsec along with very low latency and low communication jitter. When multiple axes and events need to be synchronized exactly, jitter as little as 1µsec can already have a negative effect on the system performance.
Why use EtherCAT?
Performance
EtherCAT is the fastest industrial Ethernet technology and can synchronize with nanosecond, accuracy significantly improving application efficiency.
Flexible Topology
EtherCAT doesn’t need hubs or switches that limit conventional Industrial Ethernet systems, making it virtually limitless when it comes to network topology. Line, tree, star topologies and any combinations thereof are possible with a nearly unlimited number of nodes. The network topology is only determined by the machine structure.
Simplicity and Robustness
Since EtherCAT doesn’t require switches and active infrastructure components, the costs for these components and their installation, configuration, and maintenance are also eliminated. The Ethernet fieldbus makes configuration, diagnostics, and maintenance easier, reducing system costs.
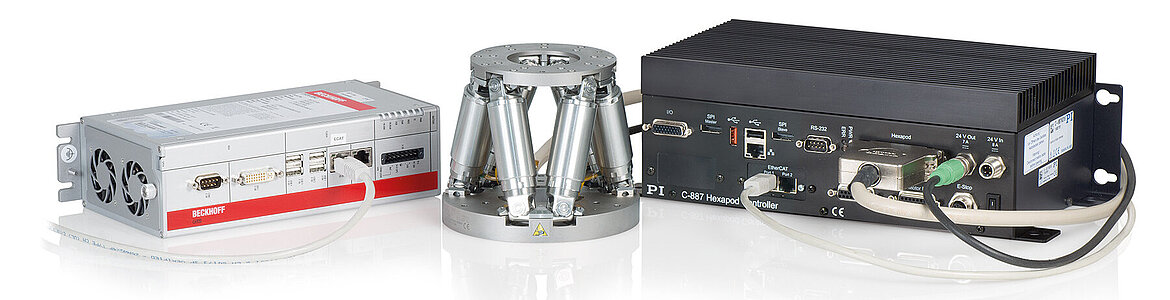
Affordability
EtherCAT delivers the features of Industrial Ethernet at the price of a classic fieldbus system because no expensive interface cards or co-processors are necessary. The master device simply requires an Ethernet port.
InputShaping and Gantry Control: Advanced Control Algorithms
PI precision automation sub-systems are based on ACS motion control hardware, benefiting from EtherCAT integration.
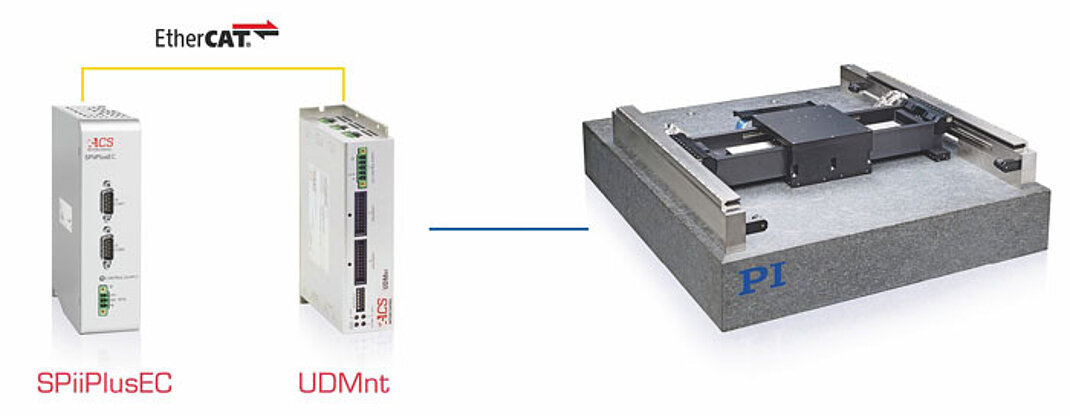
EtherCAT Technology Background
An EtherCAT network includes one EtherCAT Master and one or more EtherCAT nodes. One network can include a maximum of 65,535 nodes.
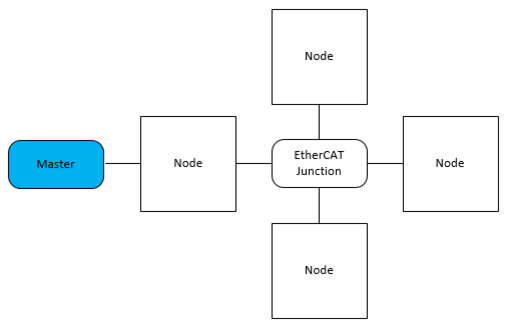
Since EtherCAT was introduced in April 2003, more than 4500 companies around the world have developed EtherCAT-based products and related software – which is easily explained given its exceptional performance, flexible topology, simple integration, and robustness.
What Network Topology Is Supported by ACS Hardware?
Line, ring, and star topologies are supported. Ring topology NetworkBoost™ is a feature that increases system uptime and productivity by network failure detection and recovery. The star topology, based on EtherCAT junctions, might be beneficial when using the Flexible Configuration feature which enables disconnecting groups of nodes during machine operation.
Synchronization: What Cycle Times Can Be Achieved?
In high performance applications exact synchronization is a critical factor. ACS nodes are synchronized applying the EtherCAT Distributed Clocks (DC) mechanism. The controller supports short cycle times: 1msec, 0.5msec, 0.25msec and 0.2msec (1, 2, 4 and 5 kHz).
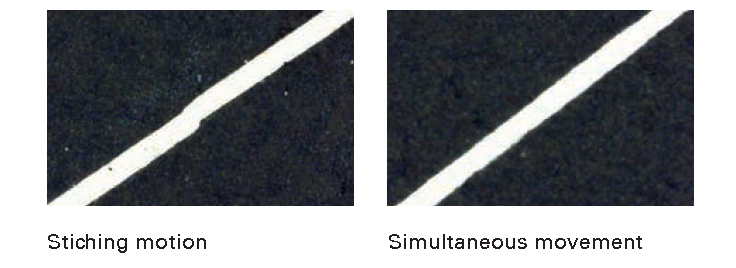
Integration of Third Party Products Made Simple
Non-ACS DS402 Drives and other types of EtherCAT nodes are commonly used with ACS controllers. The integration with other ACS products in the same EtherCAT network is easy and does not require any special adjustments.
Motion Subsystems Controlled by Third-Party EtherCAT Master
The new SPiiPlusES can also be controlled by a third-party EtherCAT Master. SPiiPlusES is a motion controller for ACS “internal” networks and, as an EtherCAT drive, supports up to 8 axes according to DS402 standard. In addition, it can be used as EtherCAT bridge, providing the functionality of synchronized data exchange between the non-ACS and ACS networks.
Advanced control algorithms, such as ServoBoost (optimize step-and-settle times), and NanoPWM (tracking with subnanometer precision) are then available within the existing network.
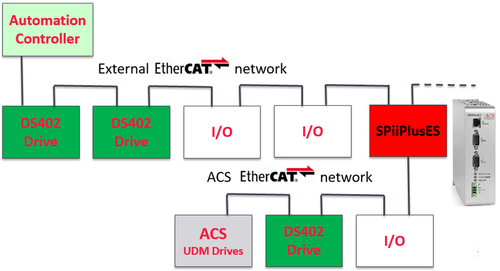
PI and ACS provide motion centric solutions for industrial automation such as those in assembly, semiconductor manufacturing, mechanical engineering, laser material processing, inspection systems, and in additive manufacturing.
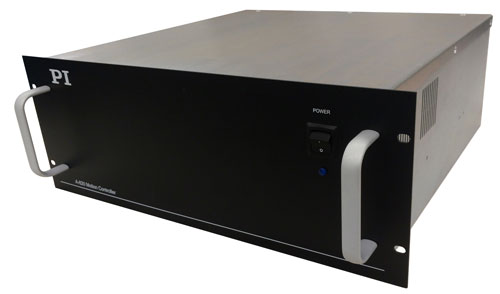
Blog Categories
- Aero-Space
- Air Bearing Stages, Components, Systems
- Astronomy
- Automation, Nano-Automation
- Beamline Instrumentation
- Bio-Medical
- Hexapods
- Imaging & Microscopy
- Laser Machining, Processing
- Linear Actuators
- Linear Motor, Positioning System
- Metrology
- Microscopy
- Motorized Precision Positioners
- Multi-Axis Motion
- Nanopositioning
- Photonics
- Piezo Actuators, Motors
- Piezo Mechanics
- Piezo Transducers / Sensors
- Precision Machining
- Semicon
- Software Tools
- UHV Positioning Stage
- Voice Coil Linear Actuator
- X-Ray Spectroscopy