Flying may once have been a privilege of the gods but today, traveling by air is taken for granted. The motto is larger, faster, and further but also safety first. Whatever component used in an airplane must be “airworthy” which means reliable, durable, and as light and small as possible. This also applies to acoustic sound transducers that generate warning sounds during automatic processes, such as closing the cabin doors of the Airbus A380.
More passengers per plane means higher profit margins per ticket – a mantra that has been driving the size of airplanes since the Wright Brothers took to the air for the first time. The largest passenger airplane currently in production is the Airbus A380. This wide-body airplane with a wing span of close to 80 meters can transport up to 850 travelers on two decks over distances close to 10,000 miles.
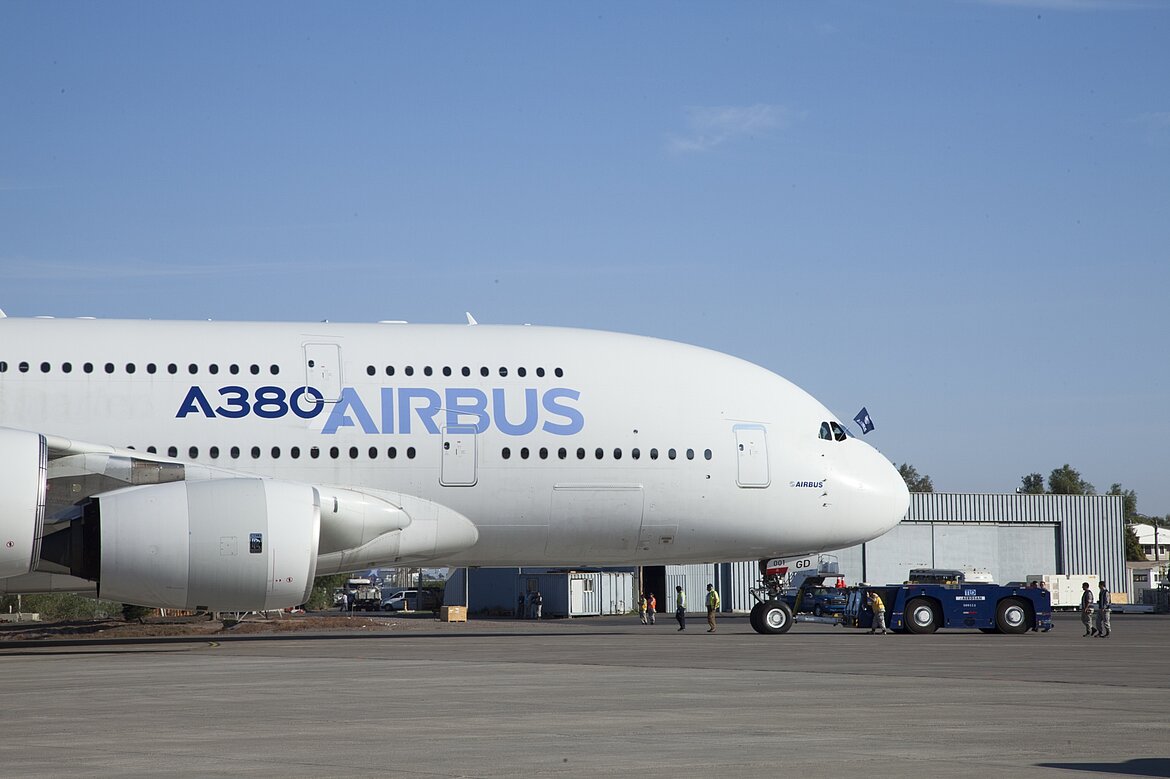
Monitoring the Door Locks
The XXL format carries some side effects – the doors on the A380 need to be closed by motor force, because they are too large and too heavy for manual operation – which in turn requires sensors and transducers to tightly monitor the closing and locking mechanism. If the locking procedure is incomplete, a warning sound is generated, and an “OK” signal is emitted when the doors are properly closed. For this purpose, 14 sound transducers are built into each airplane next to the doors.
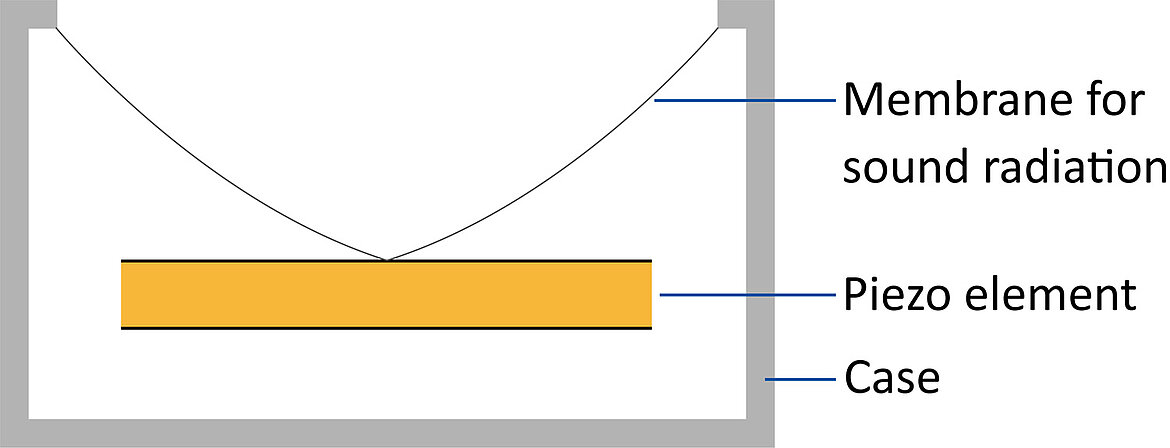
Holmberg GmbH of Berlin, Germany, who develops and produces electro-acoustic devices for professional use under demanding environmental conditions, has been a specialist for this type of airworthy sound transducers for a long time. The company is a certified manufacturer and maintenance organization for aviation devices, and in addition to Airbus, a large number of other renowned airplane manufacturers put their trust in the electro-acoustic devices from the Berlin manufacturer. This also includes the sound transducers, for which the aerospace industry requires comprehensive certification of the reliability and lifetime. The piezo sound transducers for the airplane doors are subject to considerably higher quality requirements than conventional mass-produced buzzers employed in alarm clocks and toys.
To meet the demanding requirements, Holmberg selected custom piezo ceramic discs manufactured by PI Ceramic. Reliability, durability, and exact adherence to the technical specifications are important parameters for their use in an airplane component.
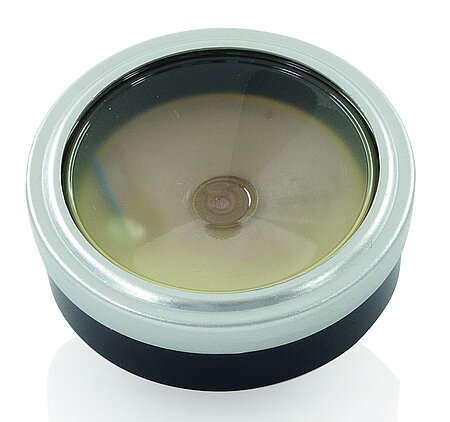
Basically, sound transducers consist of two piezo disks glued to each other, a plastic membrane, and a waterproof case. When electrical voltage is applied, the piezo ceramic begins to deform analogous to the drive frequency. This is the so-called inverse piezo effect; the piezo element converts the electrical energy to mechanical energy. The motion is transferred to a membrane which then radiates sound waves. Depending on which of the piezo disks is operated, two different tones are generated according to the respective resonant frequency; the OK signal for “door closed” or the warning tone. The “volume” of the small sound transducer is 160 dB and after installation, it is reduced to 84 dB, which is still quite remarkable.
Piezoelectric Sound Transducer Sub-Assembly by PI Ceramic
“We obtain the two piezo disks which are already glued together, from PI Ceramic“, explains Peter Köppel, technical director at Holmberg, and quickly explains the reasons: “The piezo disks meet our high standards of quality and are distinguished by a very low tolerance to all piezoelectric parameters relevant for sonic performance such as resonant frequency, electrical capacitance and coupling coefficients.“
PI Ceramic has been developing and manufacturing piezo ceramic materials, components, and sub-assemblies for standard and OEM applications since 1992 and is able to respond quickly to customer-specific requirements. “The piezo specialists have proven this in the case of our sonic transducers”, emphasizes Köppel. “When we were looking for the fastest possible replacement for our previous supplier, PI Ceramic understood our requirements right from the very beginning and was able to comply with all required specifications with the first prototype.”
PI Ceramic piezo sub-assemblies can be easily adapted to any application requirement because PI Ceramic controls all production steps from the raw material, the geometric design, and all assembly steps.
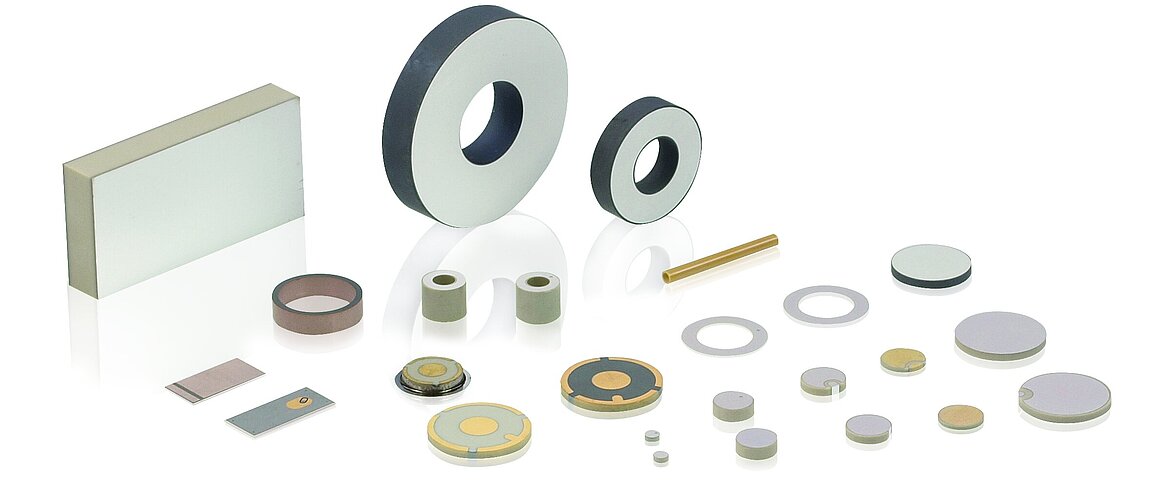
Blog Categories
- Aero-Space
- Air Bearing Stages, Components, Systems
- Astronomy
- Automation, Nano-Automation
- Beamline Instrumentation
- Bio-Medical
- Hexapods
- Imaging & Microscopy
- Laser Machining, Processing
- Linear Actuators
- Linear Motor, Positioning System
- Metrology
- Microscopy
- Motorized Precision Positioners
- Multi-Axis Motion
- Nanopositioning
- Photonics
- Piezo Actuators, Motors
- Piezo Mechanics
- Piezo Transducers / Sensors
- Precision Machining
- Semicon
- Software Tools
- UHV Positioning Stage
- Voice Coil Linear Actuator
- X-Ray Spectroscopy