Different Hybrid Drive Concepts to Solve Tough Positioning and Alignment Problems in the Nanometer Range
Novel Hybrid Actuators Combine High Force, Nanometer Precision, and High Dynamics
When faced with challenging alignment applications, precision motion system designers often have to live with an unsatisfactory compromise between accuracy, force, and dynamics.
A new hybrid approach can solve many of these issues. Hybrid actuators combine the best features of two different drive concepts into one high-performance, precision positioning system. Several types exist, tailored for different applications including semiconductor manufacturing, optical inspection, astronomy, aerospace, and laser technology.
Hybrid Concept with Linear Voice Coil and Motor/Screw Drive
Ball or roller screw drives provide high feed and holding forces, over long travel ranges. Friction in the drive screw and the linear guides limit resolution, linearity and repeatability. Adding a voice coil motor in-line with drive screw can help overcome these limitations. Voice coils operate without friction, can provide smooth motion, sub-nanometer resolution, and fast response. Travel ranges are typically limited to one inch and they need to be powered to hold a load.
Operating both drives in series on a common position feedback signal, the voice coil can correct for all higher frequency error components such as caused by friction, cyclical errors, and stick-slip effects.
Hybrid Linear Actuator Concept with PiezoWalk Linear Motor and Piezo Stack Actuator
Another hybrid precision mechanism developed and established for high end semiconductor inspection applications is based on a combination of a PiezoWalk linear motor and an “analog” piezo actuator.
A variety of different piezo motor concepts is available to meet different requirements in terms of size, force, speed, and cost. The PiezoWalk® motor principle is especially robust, as it provides linear motion to a runner by a succession of small steps (see animation). Travel ranges are only limited by the length of the runner, and the motor is very stiff and self-clamping even when powered-down. Adding a PICMA® piezo stack actuator in-line with the runner can add high dynamics over travel ranges. The stiff, monolithic piezo stack with responsiveness in the millisecond range, or better, provides the high dynamics required for fast focusing and scanning applications.
Hybrid Concept with Piezo Stack and Motor/Screw Drive, Designed for the ELT Telescope
A closed-loop hybrid linear actuator based on a motor/screw drive and integrated piezo stack actuator was designed for the ELT telescope. PI engineers, fulfilling the requirements set by scientists and astronomers from the European Southern Observatory (ESO), came up with a unique ultra-high precision, high-load actuator to align the mirror segments of what will be the world's largest terrestrial optical telescope.
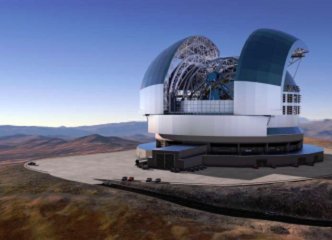
The telescope's revolutionary design consists of a 39m diameter primary mirror (M1) divided into 798 independent mirror segments (segmenting is required because it is technically not feasible to make one mirror of that size). Each mirror segment weighs about 550lbs and is positioned by three independent hybrid actuators, in a tripod configuration, providing a max travel range of 10mm and push force of 1050N.
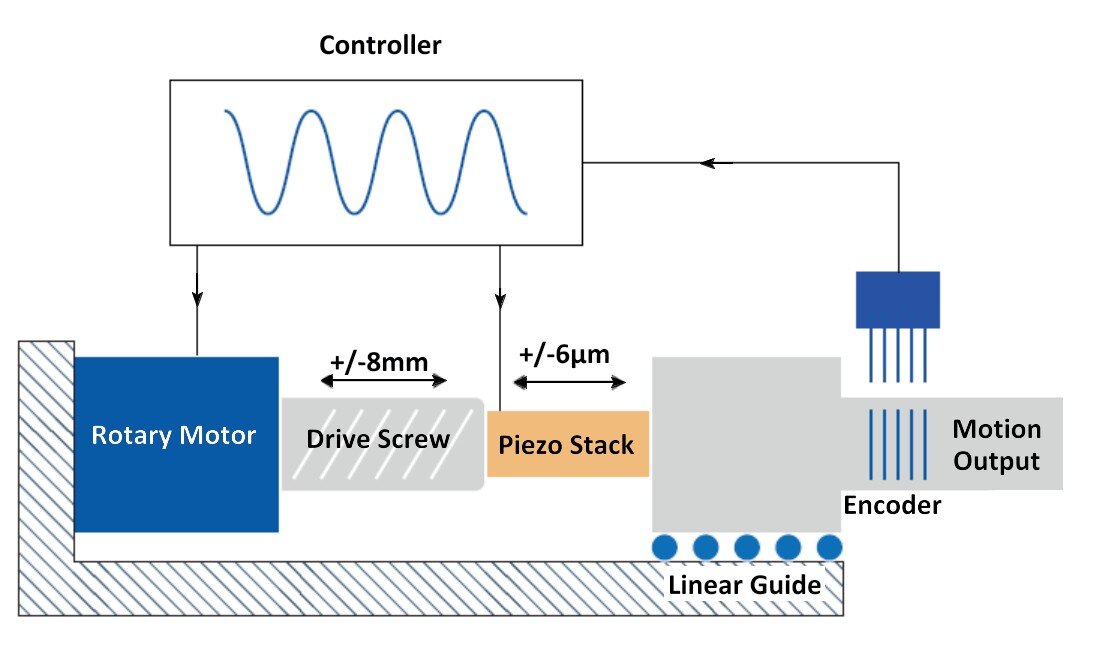
In order to reach the high optical resolution expected from the new telescope design, all mirror segments need to stay aligned to <2 nanometers at all time. Besides high precision and force, low energy consumption was another major requirement in the actuator design - to minimize the negative effects of heat dissipation on the performance of the telescope.
Controller and Position-Feedback Sensor for the Hybrid Drive System
Unlike conventional coarse/fine systems where two independent mechanisms work with independent position sensors and controllers, the advantages of the novel hybrid drive can only be achieved when a common controller and position feedback sensor are used. In this case, a high-resolution optical linear encoder with 0.1nm resolution per increment was selected.
The drive screw is operated by a brushless, high-torque motor via a high-ratio, zero-play, reduction gearhead with a constant transmission ratio. The high transmission ratio helps to hold the load in place even when the motor is not powered (another measure to reduce power consumption).
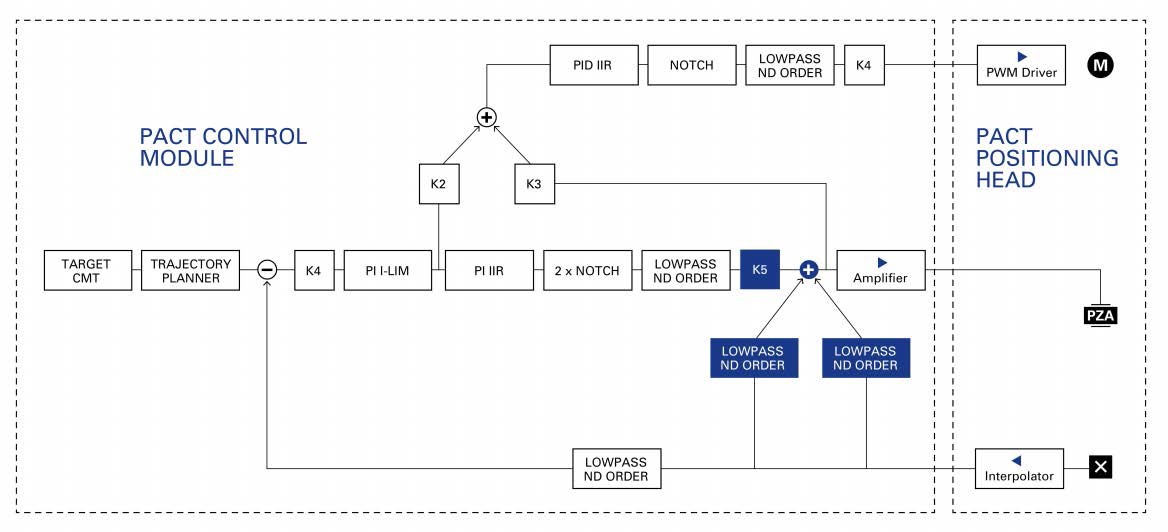
A dedicated control module controls both drives simultaneously receiving feedback from the common position measuring system. The servo-algorithm is designed to see the brushless motor/screw and the piezo actuator as a single unit.
Outside of astronomy, application areas for hybrid precision actuators include measuring technology, surface inspection, semiconductor manufacturing, microscopy, and laser technology.
Traditional Piezo Actuators - Short Range Positioning with Sub-nanometer Accuracy, High Force, and Fast Response
Piezo actuators convert electrical charges into mechanical displacement and vice versa. Due to the solid stage nature of this effect, resolution is virtually unlimited. Linear motion can be generated without conversion from rotation, without any friction involved. The piezo effect is maintenance- and wear-free. Traditional piezo actuators provide travel ranges of 10 to a few 100µm, but they can move loads up to several tons with extreme precision. Electrically, piezo actuators act as capacitive loads and need virtually no power in steady state operation – but they can respond rapidly to a drive voltage change with rise times in the microsecond to millisecond range.
The lifetime of piezo actuators is convincing: In a study, NASA/JPL ran PICMA® multilayer actuators, 100 billion cycles without failures, before sending them to Mars on the Curiosity rover’s science lab.
In PICMA® multilayer actuators, the active layers consist of thin ceramic films surrounded by an all-ceramic insulating layer that protects electrodes against humidity, thereby highly reducing the risk of failure caused by leakage currents. The monolithic piezoceramic block of such an actuator is very reliable even under extreme ambient conditions and high temperature differences. It has succeeded in applications including machining, aerospace, life science, medical technology, and microscopy.
For additional protection, the piezo actuators used in the telescope hybrid actuator are embedded in sealed metal containers filled with nitrogen in order to reach 30-years of lifetime in the adverse ambient conditions in the Atacama Desert.
Authors: Oliver Dietzel, Stefan Vorndran
Blog Categories
- Aero-Space
- Air Bearing Stages, Components, Systems
- Astronomy
- Automation, Nano-Automation
- Beamline Instrumentation
- Bio-Medical
- Hexapods
- Imaging & Microscopy
- Laser Machining, Processing
- Linear Actuators
- Linear Motor, Positioning System
- Metrology
- Microscopy
- Motorized Precision Positioners
- Multi-Axis Motion
- Nanopositioning
- Photonics
- Piezo Actuators, Motors
- Piezo Mechanics
- Piezo Transducers / Sensors
- Precision Machining
- Semicon
- Software Tools
- UHV Positioning Stage
- Voice Coil Linear Actuator
- X-Ray Spectroscopy