Computing’s inflection points occur when new user-interface concepts enter the mainstream. The advent of the graphical user interface is one example; the touch interface, now universal on smartphones and tablets, is another. Computing is in the midst of yet another inflection with the advent of voice control, but meanwhile the haptic revolution is still unfolding.
Touch-sensitive interfaces are not only used in mobile devices, buttonless control surfaces are quickly conquering the automotive and medical device worlds. Behind every touch-enabled smartphone, tablet, laptop, trackpad, watch or other digital marvel are surprisingly sophisticated sensors. Increasingly these are force-sensitive as well as position-sensitive, for example marking not only where you touch on a screen but how hard and with what sort of change over time. Is your press a gentle swipe or an urgent stab? Are you sliding your finger across the glass or rolling it? Today’s sensors know, and the underlying software will differentiate between these actions and respond accordingly.
Producing devices with touch-sensitive interfaces also requires highly precise test equipment with the ability to reproducibly generate fine-grained motions of exacting force and time profiles. At the same time, position must be monitored and controlled, as position/time/force is often a complicated relationship. Even a simple push button switch must provide sufficient hysteresis to avoid “bouncing,” a phantom actuation that occurs near the switching threshold. Since this is a critical quality metric, production testing is often a must to ensure outgoing and incoming quality.
PI’s V-273 family of voice-coil actuators, coupled with the novel C-413 digital controller, offers developmental and test engineers the perfect tool for quantitatively qualifying touch-enabled devices. The system combines:
- An ultra-responsive, low-inertia, long-travel precision motion actuator with a sub-micron resolution, non-contacting linear encoder
- A sub-milliNewton-resolution force sensor
- A sophisticated all-digital controller capable of multivariate control, advanced servo algorithms, fast interfacing, and bumpless switching between position and force domains
- High throughput, with position and force settling times <15msec, including motions from non-contact to a specified target force level in contact
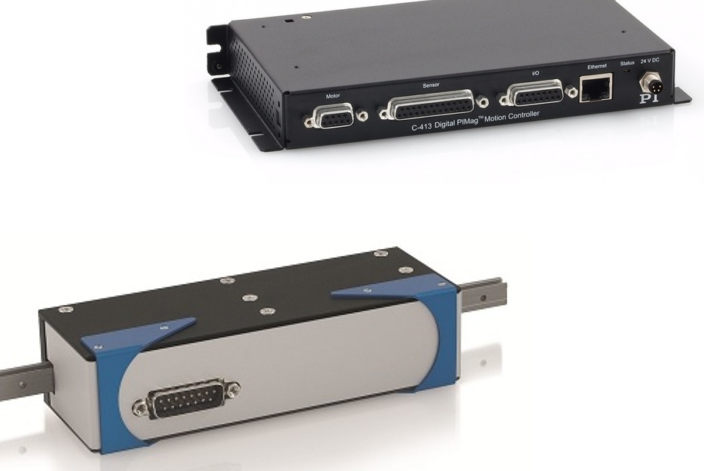
Position and force set points are easily commanded and switched between for quasi-static testing, and meanwhile the controller integrates a highly deterministic wave generator capable of arbitrarily complex position or force sequences. A built-in data recorder operating off the same clock as the wave generator allows engineers to acquire high-speed data absolutely synchronously with records of position and force. High-speed USB or Ethernet communications interfaces, plus auxiliary real-time TTL and analog I/O options, ensure system responsiveness and test productivity. Actuator tips are easily exchanged to meet specific needs for compliance, geometry, conductivity, and other details.
This system was shown in operation at SEMICON West 2016 in San Francisco. In our demonstration, a simulated touch device was repetitively actuated by a finger-simulating polymeric tip at the end of the actuator. A swept-sine sequence was generated by an easy-to-use graphical tool crafted in LabVIEW and offered for Windows, OS X, and Linux. This Patterned Force Generator utility is easily scriptable by Python, MATLAB, Excel or virtually any other software an engineer might wish to use to generate repetitive motion or force sequences, either on the same machine or remotely across a LAN.
Applications include production qualification and calibration of all manner of touch- and force-enabled sensors, assemblies, and fully manufactured devices. These include switches, touchscreens, and trackpads, in form factors from wrist-worn to pocketable to desktop, and wall-mounted formats, as well as automotive and medical applications. This highly responsive, cost-effective system is fully industrialized and suitable for the serious business of factory automation.
Blog Categories
- Aero-Space
- Air Bearing Stages, Components, Systems
- Astronomy
- Automation, Nano-Automation
- Beamline Instrumentation
- Bio-Medical
- Hexapods
- Imaging & Microscopy
- Laser Machining, Processing
- Linear Actuators
- Linear Motor, Positioning System
- Metrology
- Microscopy
- Motorized Precision Positioners
- Multi-Axis Motion
- Nanopositioning
- Photonics
- Piezo Actuators, Motors
- Piezo Mechanics
- Piezo Transducers / Sensors
- Precision Machining
- Semicon
- Software Tools
- UHV Positioning Stage
- Voice Coil Linear Actuator
- X-Ray Spectroscopy