How to Align Opto-Mechanical Components with Simple and Effective Tools
Miniature Piezo Motorized Actuators Provide Reliable and High Precision Remote Alignment of Kinematic Mirror Mounts, Beam Paths, Sensors, Optical Assemblies
Scientific instruments, laser systems, life-science instrumentation all depend on the precise alignment of optical and opto-mechanical components such as lenses, mirror mounts, shutters or apertures. Key factors for practical usability are stability (no mechanical drift once a position has been set), reliability, minimum size and energy consumption (heat dissipation), easy remote control, and last but not least, affordability. The latest generation of motorized kinematic mirror mounts benefits from a compact motorized actuator principle explained below.
Piezo Ratchet Motor Actuators vs Stepper Motor Actuators
Stepper motor driven precision actuators have a good track record for precision alignment applications. They provide high resolution, force, and relatively high speed. Their downside is size and heat generation (especially when used in high-resolution micro-step mode, the motor will not hold a position when powered off).
Piezo-ratchet-motor-driven actuators can be designed much smaller than conventional stepper motor actuators. They provide nanometer resolution, very low energy consumption (heat dissipation), and are self-locking when powered down. Due to the compact size / form factor, they can be easily used to replace manual micrometers. For applications where the absolute position is not relevant (feedback is provided by a system parameter such as optical power, focus, etc), open-loop actuators can be used. This situation also allows for simple control solutions, where one driver can be used to operate multiple actuators in sequence, by an internal electronic switch. Compared to traditional motorized precision-actuators, piezo-ratchet motor actuators provide lower velocity and are ideal for “set-and-forget” applications that would typically be handled by manuals micrometers.
Piezo Ratchet Motors - How Do They Work?
Piezo ratchet motors are “stick-slip” type motors that make use of inertia (table cloth trick). Inertial drives utilize the cyclical alternation of static and sliding friction which is generated by a piezo element that expands slowly and contracts quickly, in the case of the PiezoMike motors, turning a fine-pitch screw. Each step is as small as 20 nanometers.
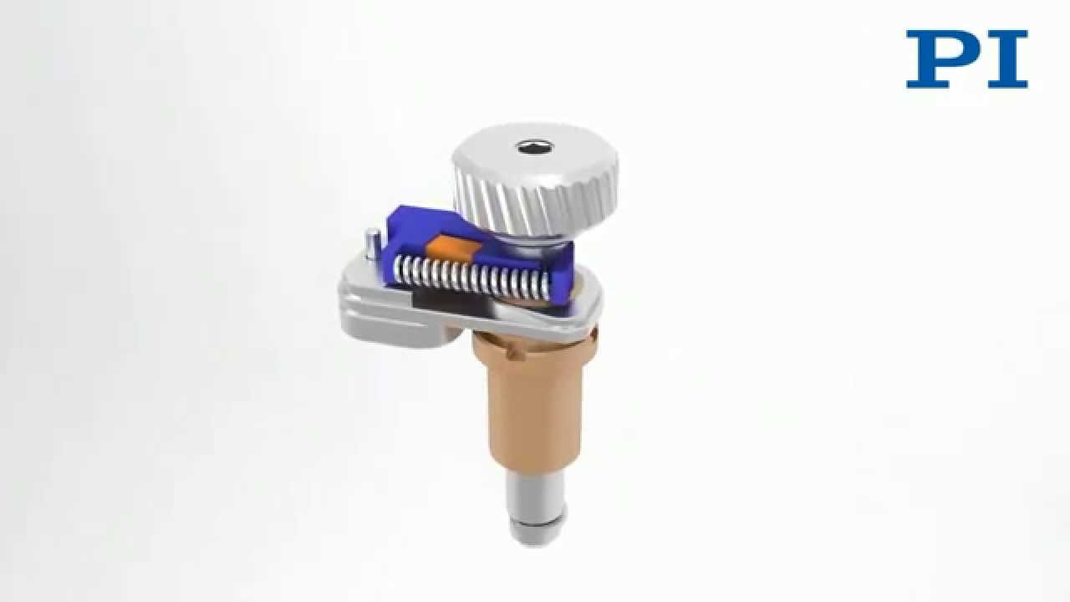
Components and Combinations
PiezoMike Piezo ratchet motor actuators are available for ambient and vacuum environments. In addition to actuators, solutions with kinematic mirror-mounts (tip/tilt mounts) are readily available for integration.
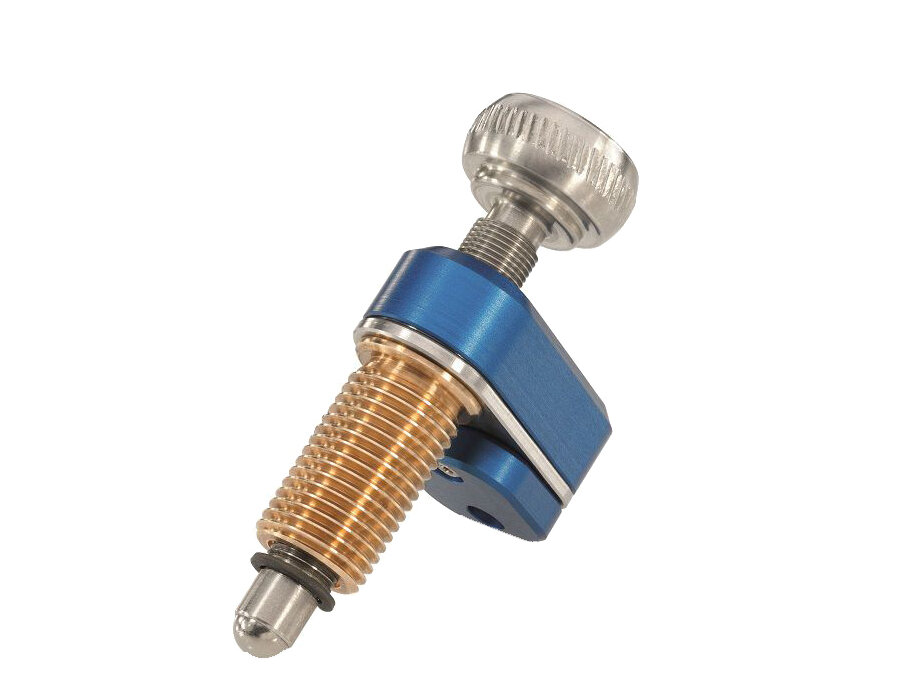
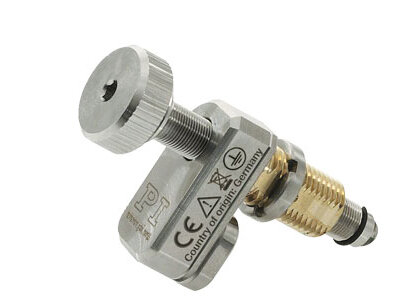
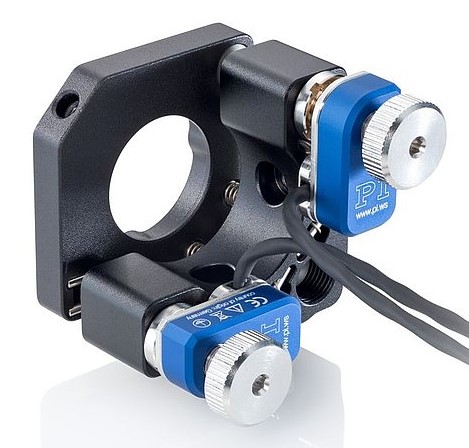
High Push and Holding Force, Excellent Long-Term Stability
Due to the compact, simple, and robust design, PiezoMike linear actuators are vibration-proof, shock-resistant, and long term stable. Despite the miniature size, the piezo-ratchet mechanism provides a feed force of >20N (~4.5lbs) and 100N (~22lbs) holding force, making it the ideal choice for “set-and-forget” applications.
High Reliability - 1 Billion Steps
PiezoMike linear actuators can provide a billion steps or turn the screw 20,000 times. The materials and piezo driver are designed such that even after long periods of rest, the PiezoMike will reliably move when a positioning command is sent.
How to Control the PiezoMike Actuators?
The driver is designed to provide a quasi-saw-tooth like signal, tuned to the electrical & mechanical properties of the actuator. An example is given below – the E-872 driver contains one piezo driver circuit that can operate up to 4 actuators sequentially – a compact and cost-efficient solution.
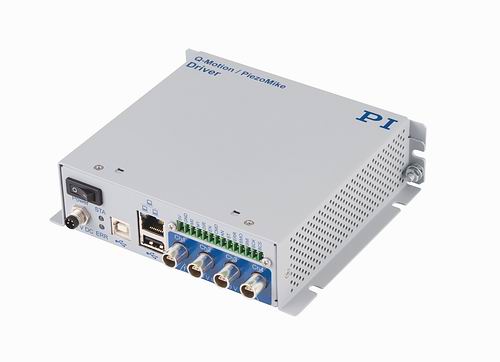
Blog Categories
- Aero-Space
- Air Bearing Stages, Components, Systems
- Astronomy
- Automation, Nano-Automation
- Beamline Instrumentation
- Bio-Medical
- Hexapods
- Imaging & Microscopy
- Laser Machining, Processing
- Linear Actuators
- Linear Motor, Positioning System
- Metrology
- Microscopy
- Motorized Precision Positioners
- Multi-Axis Motion
- Nanopositioning
- Photonics
- Piezo Actuators, Motors
- Piezo Mechanics
- Piezo Transducers / Sensors
- Precision Machining
- Semicon
- Software Tools
- UHV Positioning Stage
- Voice Coil Linear Actuator
- X-Ray Spectroscopy