Modular Photonics Alignment Systems Enable Production Advances for SiP Devices
Motion control plays a key role in emerging technologies like Quantum Communications, Quantum Computing, Nanosats, LIDAR, optical logic. The need to process, store, and convey more data at higher speeds is relying heavily on Silicon Photonics. This presents many challenges for test and packaging processes and imposes the need to align fiber optic devices in production environments with high throughput.
PI offers efficient photonics alignment solutions that can be integrated quickly and perform optimally on the ACS motion controller platform. High precision, synchronized, multi-axis positioners along with PI proprietary firmware-based alignment algorithms have been developed for disruptive levels of throughput.
Comprehensive User-Friendly Software Packages Enabling Easy Integration
This comprehensive package includes our MMI Application Studio, a powerful, easy-to-use tool for configuring, tuning, programming, and characterizing motion performance.
The SPiiPlus Motion Simulator accelerates tool development with both controller level onboard routine programming as well as host level interfacing, all in advance of hardware delivery. This reduces the time to market by taking advantage of ACS host application libraries for popular platforms including C/C++, COM, .NET, Python, MATLAB, Linux, and low-level socket communication.
PI also offers open-source graphical applications examples in major languages, such as LabVIEW, Python, C#, and Visual Basic.
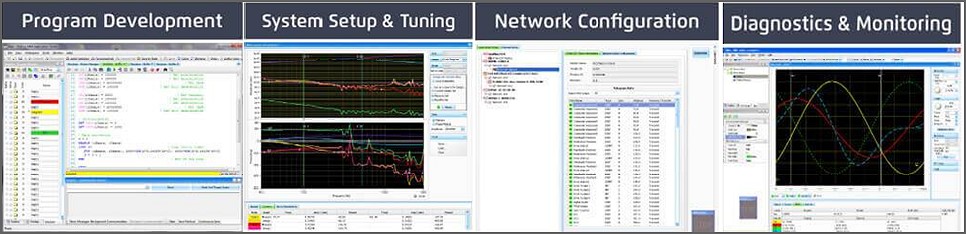
PI Proprietary Fast Alignment Algorithms for Quick Peak Finding
The fastest communication is the one that does not have to take place. That’s why PI alignment algorithms are embedded in the motion controller, rather than running on an external host PC. PI’s onboard FMPA (Fast Multi Channel Photonics Alignment) algorithms offer industry-leading performance and have demonstrated orders of magnitude higher throughput than conventional methods.
In silicon photonic circuits, the ability to measure with high dynamic range and low electrical noise is critical. For these applications, a high dynamic range optical power meter is used with a high-resolution analog output. This voltage signal is passed to the controller via a high-resolution analog input (24-bit) offering extremely low noise and fast synchronous data sampling to 5 kHz.
Choice of Area Scan Algorithms: Circular and Raster
Two area scan algorithms, for characterization and determining of the area with the main optical peak, are available. Both are optimized for minimum excitation of mechanical resonances and shortest execution time.
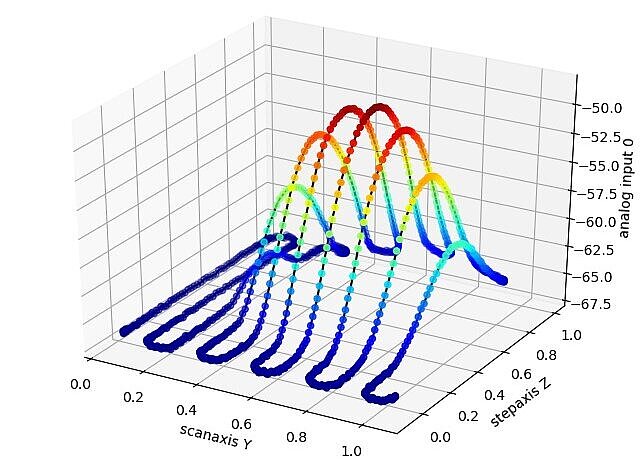
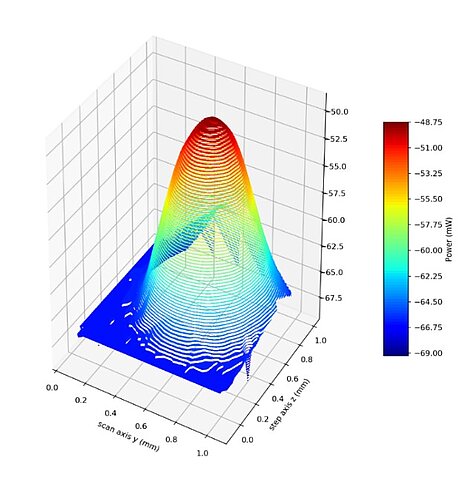
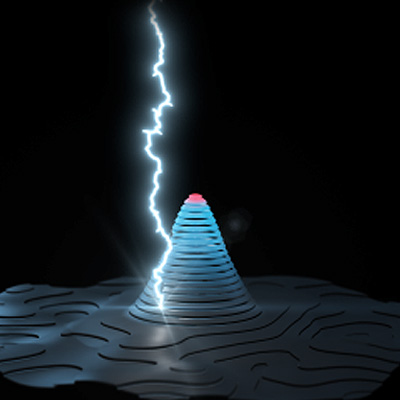
Prior to initiating the optimization process, it is imperative to detect an optical signal—above the noise level—a step referred to as the first light capture.This task has historically proven to be very time-consuming across various industrial photonics alignment applications, such as wafer probing and device packaging. However, the challenge is notably heightened in devices with inputs and outputs, where aligning both sides is essential to attain even a threshold level of coupling, further extending the time required for the process. Engineers at PI’s Silicon Valley Tech Center have now solved the first-light capture problem, with a new algorithm dubbed PILightning. This new technology is ideal for high-volume PIC testing. It promises to reduce first-light capture time by orders of magnitude and is outpacing any other technique currently used for automated photonics alignment. In dual-sided first-light capture tests, we have seen improvements of 500X and more.
Gradient Search Algorithm
A gradient search is a dither routine intended to detect the signal maximum by calculating and acting on steepest gradient to peak. The starting point of a gradient search can be the position determined by the area scan (where first light was found). When more than one peak is to be expected, it is especially important to run an area scan first to avoid locking onto a spurious peak. When Gradient calculations are done rapidly onboard to enable fast optimization and tracking of peak signal.
F-141 Compact Cost-Optimized Alignment System, 4- and 6-Axis Options
For applications where fast alignment in 4 or 6 axes within a very compact package is beneficial, the F-141 PINovAlign system offers a cost-optimized, high-performance solution. It integrates three V-141 three-phase motor-driven stages with precision crossed roller bearings, arranged in an XY+Z stack. A custom, voice-coil-driven, flexure-guided rotary stage is mounted to the front of the Z-axis, enabling precise Theta-Y motion. To enhance stability, the Z stage includes a pneumatic counterbalance and an integrated brake, making the system ideal for demanding precision alignment tasks.
This compact system combines ultra-precision crossed roller bearings and flexure guidance for high-performance motion with exceptional stiffness and positional stability. Its space-efficient design minimizes angular errors, enabling highly repeatable positioning at the probe tip. Equipped with direct-drive motors and optical encoders, the F-141 supports fast scanning over both short and extended travel ranges.
An optional motorized or manually adjustable pitch/yaw base adds full six-degree-of-freedom alignment capability. Additional configurations are available to accommodate various optical axis orientations.
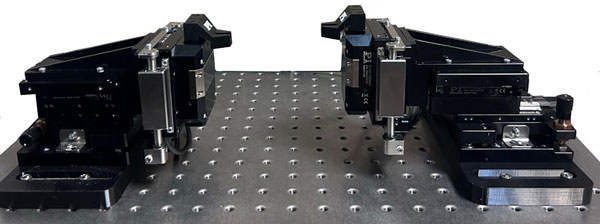
F-716, 6-DOF Parallel-Kinematics Air Bearing Motion System
The F-716 is a high-precision, high performance air bearing motion system with six degrees of freedom ideal for Fast Multi- Channel Photonics Alignment (FMPA) involving fiber arrays, silicon photonics circuits, and wafer level short range metrology applications.
The system features direct drive motor technology in combination with air bearings; the frictionless, non-contact design makes it a perfect solution for 24/7 highly dynamic applications. In combination with high resolution linear encoders, the F-716 system is a great fit for alignment applications.
Lack of mechanical bearings makes the F-716 non-wearing, maintenance free, with virtually unlimited lifetime ideal for cleanroom environments.
F-716 Low Profile Design
The F-716 air bearing system is extremely low-profile (100mm overall height). The wide base, low-profile stiff design of the system enhances both guiding performance as well as top-line dynamics and servo-bandwidth (high-throughput) while being easily integrated with minimal vertical space requirement in the tool/setup. The profile height of only 100mm keeps the center of gravity down for better dynamics and stability.
F-716 Programmable Pivot Point
Onboard Inverse and Forward Kinematics provide automatic coordinate transforms for simple commanding of the 6-DOF motion system with programmable virtual pivot. This allows simple angular adjustments to be made around critical alignment points easily, quickly, and with high precision.
The Compact F-142 Series High Performance Air Bearing XYZ Stage
The F-142 XYZ air bearing motion system is a high-performance, highly dynamic, modular, and very compact solution to Fast Multi-Channel Photonics Alignment, configurable as XY, YZ, or XYZ. A high value solution for a range of alignment applications including Photonic Circuit surface coupling, fiber-to-fiber and fiber-to-waveguide applications.
The very compact design of F-142 stages makes these systems ideal for space confined applications. The XYZ system features a cost-effective counterbalanced Z version with minimal impact on stage form factor.
High Frequency Scanning Motion with High Servo Bandwidth
The F-142 air bearing stage features a voice coil motor and air bearings to offer very high dynamics under light load conditions. The stage itself has a moving mass of only 250g (most of the motor force is available for better dynamic performances and better throughput). Demonstrated here are dynamics test results with fixed frequency fast area scans at scan frequencies of 20Hz. Looking at reference position vs feedback position, there is minimal phase lag error and minimal following error, so the stage achieves 20Hz with relative ease dynamically. (This is with 200µm peak-to-peak, repetitive alignment scanning motions.)
The frictionless design of the F-142 avoids wear and tear, requires no maintenance, and guarantees a long lifetime. It is perfect for 24/7 highly dynamic applications.
The F-143 alignment system is the larger brother of the F-142, featuring 25mm travel, 1nm resolution absolute encoders and higher force linear motors. In addition to the pneumatic counterbalance on the vertical axis, it also comes with an integrated brake. More information on the F-143.
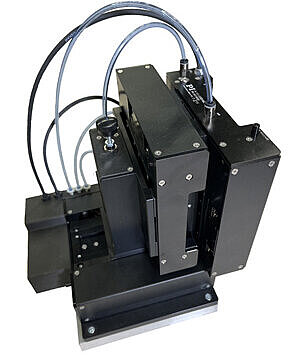
Gantry Platforms for Large-Area Photonic Test and Assembly
Processing nanoscale structures densely packed over large areas in semiconductor or photonics test and manufacturing applications require high precision, high throughput solutions delivered on reliable and stiff platforms. PI flexible gantry systems running firmware-based proprietary alignment algorithms have proven performance to improve throughput by a factor of 100 (compared to other approaches) delivering repeatable and robust results.
PI gantry systems use two large, ironless linear motors to accommodate the high dynamics required in photonics applications. These highly efficient direct drive motors combined with two high resolution linear encoders on the gantry axis (nanometer or sub-nanometer resolutions) can deliver ultra-repeatable positioning on demanding duty cycles.
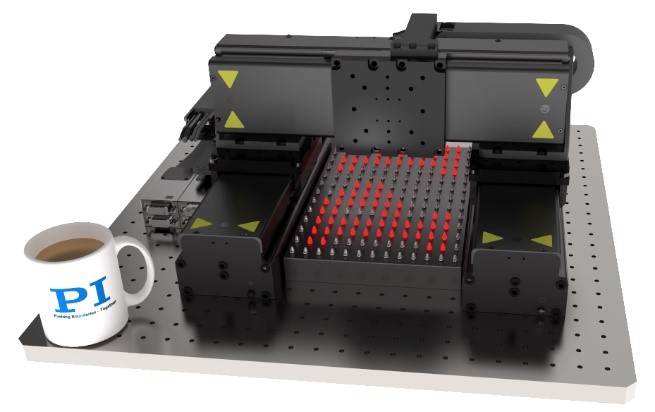
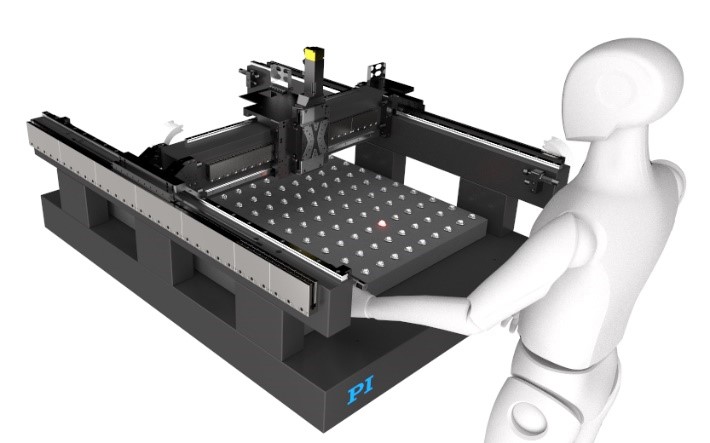
F-308 Compact XYZ Direct Drive Photonics Alignment System
The F-308 is an ultra-compact linear-motor-driven alignment system and provides 7mm travel with 1 nanometer resolution. It is based on the V-308 nanopositioning linear stage. A few key specs are listed below:
- Low profile, low moving mass, high dynamic direct drive stage design
- Integrated user-adjustable magnetic counterbalance for vertical application (up to 1kg of load)
- Highly dynamic direct drive with voice coil motor
- High-resolution PIOne proprietary linear encoder (1nm resolution)
- Precision anti-creep crossed roller bearings
F-408 Compact XYZ Direct Drive Photonics Alignment System
The F-408 alignment system is based on the V-408 linear motor stage. It provides up to 25mm travel range with 20nm resolution. A few key specs are listed below:
- Compact, high-dynamic, low-profile, direct drive, modular design
- Highly efficient, compact, ironcore linear motor
- PI two proprietary linear encoder (20nm resolution)
- Precision crossed roller bearings with extended operated life at rated load
- Integrated pneumatic counterbalance with brake for vertical applications
F-508 Compact XYZ Direct Drive Photonics Alignment System
The F-508 alignment system is based on the V-508 linear-motor stage with crossed roller bearings. This stage provides long travel ranges to 170mm and is equipped with an ultra-high-resolution PIone incremental encoder.
- Low-profile Al alloy body with low moving mass
- Smooth dynamics, compact, ironless linear motor
- High-precision, PIOne linear encoder (2µm pitch, 1 nm, interpolated resolution)
- Precision anti-creep crossed roller bearings
- Integrated pneumatic counterbalance with brake for vertical applications
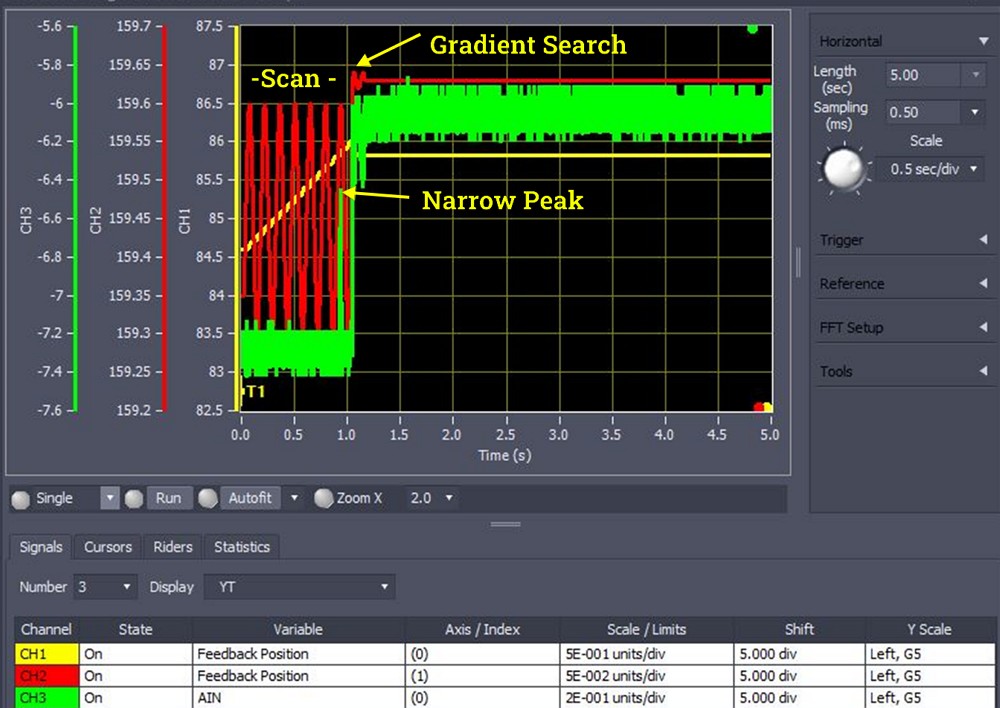
Photonics Alignment Systems mentioned will be fully assembled with factory optimized configuration under application-specific applied dummy load. System metrology to measure repeatability and accuracy will be performed with error mapping included. System parameter information along with Error Maps, Alignment Algorithms, and safety parameters will be uploaded on high-performance A-81x series motion controller (an ACS based controller). Motion System will be ready for turnkey operation on delivery.
ACS controls featuring a wide range of powerful tools and advanced capabilities are the industry leader providing motion solutions to high demand applications.
Advanced Servo Control Tools
- ServoBoost, ServoBoostPlus
- Compensates Real Time Disturbances for faster settling, better stability, lower jitter, better constant velocity, better following error
- Input Shaping
- Avoids exciting resonances
- PILOT
- Improves step-settle dynamic performance by reducing motor current requirements and heat generation (enhanced throughput)
- LearningBoost
- Increases motion system accuracy and throughput by learning and pre-emptively compensating for system disturbances
PI is a world leader in active photonics and optical alignment technology, pioneering ultra-fast mechanisms, controllers and algorithms such as Fast, Multi-Channel Photonics Alignment (FMPA) technology in numerous areas of application. We have recognized the potential for frictionless, air bearing alignment, a technology that has proven crucial many high tech industries such as semiconductor production, laser processing and medical equipment manufacturing. Active optical alignment has shown benefits in applications including silicon photonics, optical cable manufacturing, smartphone cameras, metrology equipment and more.
If you would like to learn more about active photonics alignment solutions, please contact a PI engineer directly.
Blog Categories
- Aero-Space
- Air Bearing Stages, Components, Systems
- Astronomy
- Automation, Nano-Automation
- Beamline Instrumentation
- Bio-Medical
- Hexapods
- Imaging & Microscopy
- Laser Machining, Processing
- Linear Actuators
- Linear Motor, Positioning System
- Metrology
- Microscopy
- Motorized Precision Positioners
- Multi-Axis Motion
- Nanopositioning
- Photonics
- Piezo Actuators, Motors
- Piezo Mechanics
- Piezo Transducers / Sensors
- Precision Machining
- Semicon
- Software Tools
- UHV Positioning Stage
- Voice Coil Linear Actuator
- X-Ray Spectroscopy