Q&A with Dr. Harry Marth, Head of Piezo Technology Innovation, and Dr. Mathias Bach, Head of Piezo Systems at Physik Instrumente (PI), Karlsruhe, Germany.
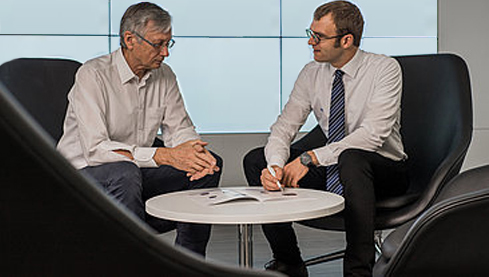
Most people would be looking forward to retirement after a successful career of 45 years. But Dr. Harry Marth is not like most people. Instead, he is most likely the world’s foremost expert on advanced piezo nanopositioning technologies. You would never know, meeting him casually, because despite all his achievements over several decades with PI, he has remained humble. And while he was recently able to drop most of his operational work load, he is looking forward to shifting his focus even tighter to the research side of business. Still closer to the beginning of his career, Dr. Mathias Bach heads PI’s Piezo Systems Group and is tasked with finding new application fields, as well as moving piezo devices into the IoT era.
Q: You have been driving the development of piezo precision systems forward since 1972 – 45 years of service for a still somewhat exotic technology. After starting out in the scientific community and moving into industrial R&D, 35 years ago, have you concluded your research?
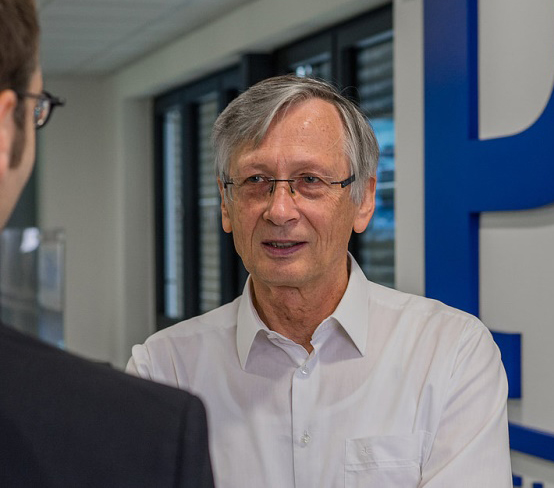
Dr. Marth: No. There’s always something new to find out about the piezo effect and its value for advancing technology, but recently the progress in materials has been showing some limitations. However, we are working on combining piezo actuator technology with other drive technologies, looking for new applications, and continually improving the performance of piezo nanopositioning systems by advancing digital control algorithms and drive electronics.
Q: New applications – The currently booming semiconductor industry is your most important business sector…
Dr. Bach: Correct, the semiconductor industry is very important for us as a piezo nanopositioning system supplier and keeps supplying new applications from the front end to the back end of the technology. Silicon Photonics (SiP), for example, is barely past its teething stage and requires extremely fast alignment mechanisms with nanometer range accuracy. Outside of the semiconductor sector, the machine tool and printing industries also use piezo motion systems to compensate for vibrations and increase production speed.
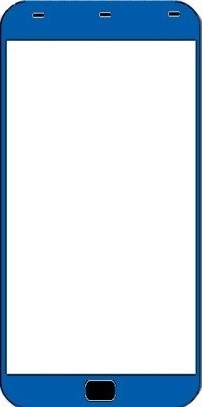
Q: How did you get to where the company is today?
Dr. Marth: Well, currently around 90% of all smartphones are manufactured with semiconductor processes that rely on our technology. We have grown together with the semiconductor and photonics sector and nowadays our technology is represented in a large number of applications. In the beginning, few other industries required the type of precision we achieve with our piezo systems, certainly not the automotive industry. Starting in the 1980s, the semiconductor industry began pushing us to develop motion systems with nanometer resolution.
Q: Which you wanted to sell?
Dr. Marth: Sure, but it wasn’t that simple. In that day, nobody in the semiconductor industry had any experience with piezo technology. That’s the reason why we decided to develop complete piezo motion solutions for the market. In a nutshell, we offer an integrated system, including the feedback sensors, guiding system, control algorithms, drive electronics and software, all out of one hand.
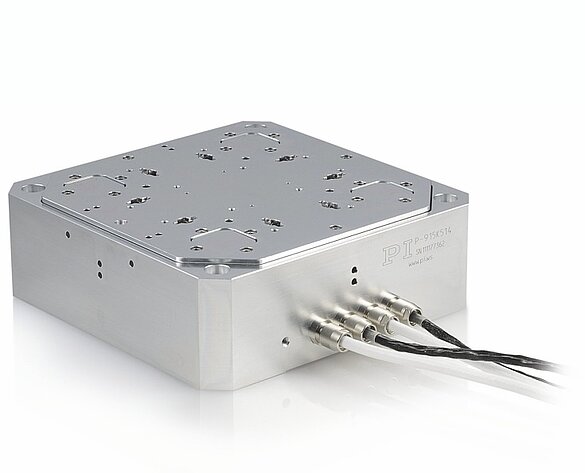
Q: What about the ceramics?
Dr. Bach: We started our own piezo ceramic manufacturing division almost 3 decades ago. That is an important competitive advantage because we can exercise influence on the ceramic material, do the research, and adapt to customer requirements. Actuator-type piezo ceramics continues to be a very small niche market for large industrial ceramics manufacturers and it is a market difficult to serve. Our piezo ceramic actuators and motors are cultivated especially for applications with precision positioning tasks and need to deliver bulletproof reliability and extremely long lifetime.
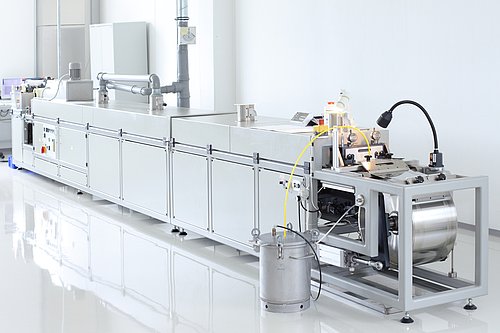
Q: You have been building up your piezo ceramic materials expertise since the 1990s – what does that mean for the industry?
Dr. Marth: Over the decades, we have learned how piezo ceramics behave and how to fine-tune the ingredients. That is our wealth of data that we use for modeling the piezo lifetime and the motion characteristics. Other precision motion providers must take whatever ceramics they can find on the market and that often means limitations on performance and lifetime. Talking about lifetime – there’s no place for production downtimes in the semiconductor industry. As a precaution, companies are more inclined to change components beforehand in order to prevent a shut-down. That does not always make economic sense. We are able to reliably assess the performance of a piezo ceramic actuator.
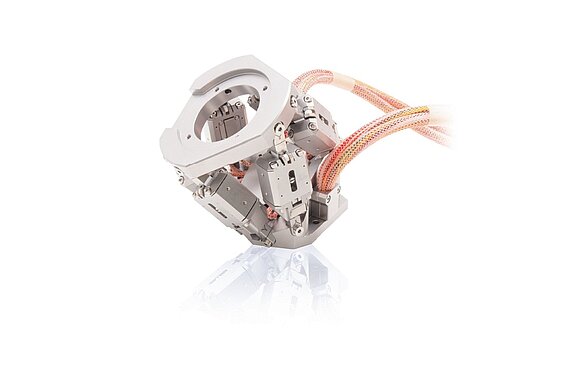
Q: Is that the reason for digitizing the piezo?
Dr. Bach: Yes, each piezo will soon have its own IP address (laughs) – even in a vacuum. Seriously though: The piezo ceramics reacts to temperature, humidity and air pressure, like any other drive system. We want to record and analyze these environmental influences to further improve our lifetime models or even perform remote maintenance. We basically need a weather station for each piezo so to speak, but it has to be miniscule in size to be integrated, because a decisive advantage is the small installation space our technology requires.
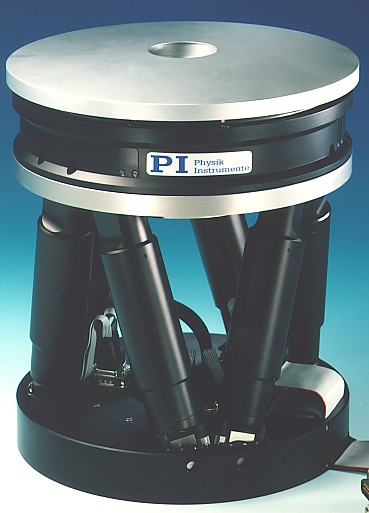
Q: Is it not already too late for that? Servo motors or magnetic direct drives will soon be able to do that.
Dr. Marth: It’s not too late. The piezo effect is more complex than traditional drive technologies and requires more control knowledge and sensor technology. We have data from customer surveys and we are responding to them.
Q: You will need to get into the user interfaces of machines, comply with or create standards for communication – are your piezo experts able to do this?
Dr. Bach: We need system architects. Our colleagues must be proficient in piezo technology, have knowledge of cabling and contacting, control and software, flow charts and communication – it’s difficult to find these types of experts, so I have to agree with you on that. But we do have one advantage: Our engineers work very closely with our customers from the start of each project – this puts us in a position to cooperate on the definition of the communication requirements and find a solution.
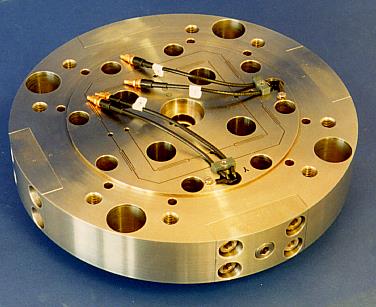
Q: And what about the traditional machining industry – what do you tell their engineers at the upcoming trade fairs?
Dr. Marth: Even traditional machining engineers want work to with more precision and they are intrigued by our technology. We see applications for piezo systems in cutting and grinding. We also combine classical drive systems or hexapod parallel kinematics machines with piezo motion to provide more options. In the past, some customers were under the impression “PI” was short for “Piezo Instruments” – but that’s not true. We engineer precision. At Physik Instrumente, the customer can chose from air bearings, magnetic direct drives, motor screw drives, hexapods, and, of course, a large variety of piezo motors and positioning systems.
Q: Ceramics in a machine tool – what is the acceptance?
Dr. Bach: We still need to further educate parts of that industry. Ceramics are more sensitive and that’s the reason why we have to take our customers by the hand, help with the integration, and encapsulate the systems. However, the semiconductor industry provides excellent references for mechanical engineering. Then, there are laser machining applications with fast piezo beam steering systems and certainly in the future, the field of active optics for laser beam shaping.
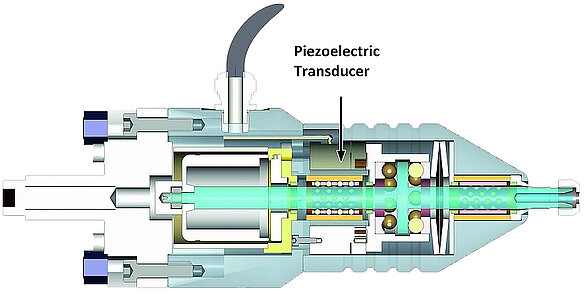
Q: So, the intelligent piezo system will become standard?
Dr. Bach: No, we don’t necessarily need intelligent piezo actuators for every application. If a machine in a research lab is down for a few days, we’re not talking about an economic disaster – unlike when a semiconductor production line comes to a screeching halt. In addition to more complex and advanced systems, we will continue to provide simple actuators and motion solutions as well.
Blog Categories
- Aero-Space
- Air Bearing Stages, Components, Systems
- Astronomy
- Automation, Nano-Automation
- Beamline Instrumentation
- Bio-Medical
- Hexapods
- Imaging & Microscopy
- Laser Machining, Processing
- Linear Actuators
- Linear Motor, Positioning System
- Metrology
- Microscopy
- Motorized Precision Positioners
- Multi-Axis Motion
- Nanopositioning
- Photonics
- Piezo Actuators, Motors
- Piezo Mechanics
- Piezo Transducers / Sensors
- Precision Machining
- Semicon
- Software Tools
- UHV Positioning Stage
- Voice Coil Linear Actuator
- X-Ray Spectroscopy