The ongoing miniaturization of piezo transducers opens up new opportunities in medical device manufacturing. PI’s piezo transducer division, PI Ceramic, is experienced in the design and manufacture of miniaturized piezo transducers and components with both traditional pressing and multi-layer tape casting technology.
Components with external dimensions below 1mm can be produced. Miniaturized sensor and actuator elements can be found in novel scanning catheter endoscopes or in active implants that regulate internal eye pressure.
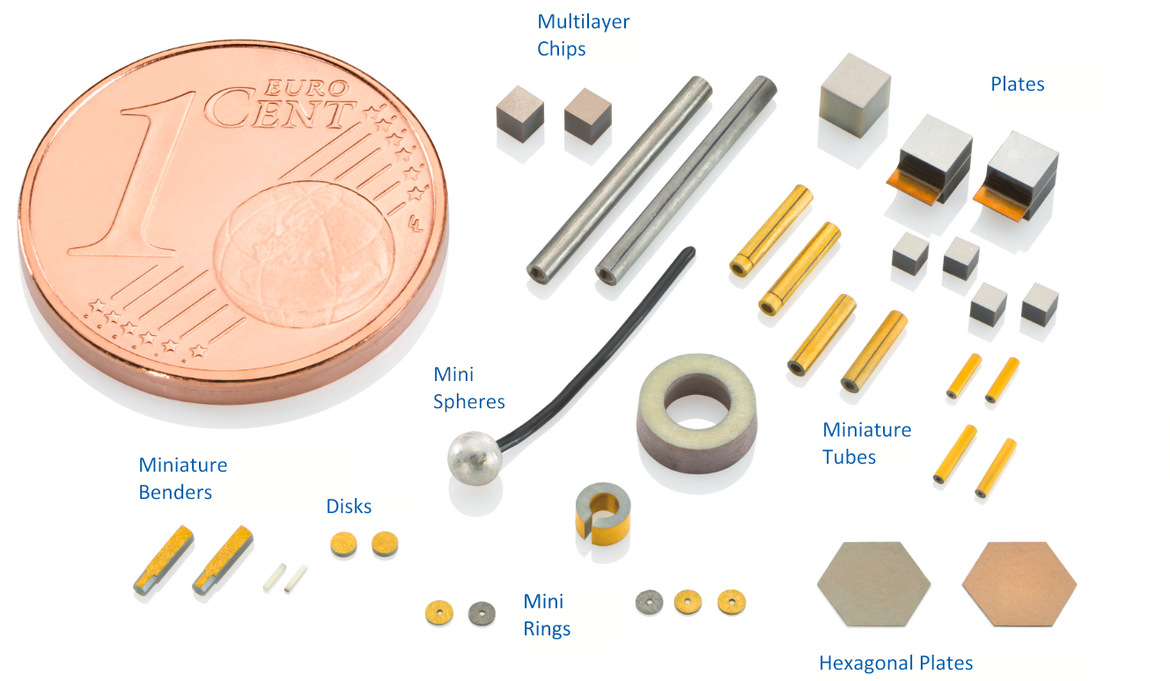
To match the individual application, PI supports a wide variety of designs, materials (including lead-free), and geometries, such as discs, plates, tubes, spheres, cuboids, and customer defined shapes for OEMs.
Miniaturized Piezo Tubes for Scanning Catheter Endoscopy (SFE)
Piezo tubes, for example, offer radial and axial deflection or, when equipped with segmented electrodes, can be used to provide scanning motion in the XY plane. PI Ceramic can manufacture miniature piezo tubes with standard diameters below 0.8mm and extremely tight tolerances in the 50µm range. Miniature piezo tubes are employed in medical instrumentation, such as endoscopes.
The latest designs are called scanning fiber or scanning catheter endoscopes (SFE) for large-area, full-color imaging with a diameter of only 1mm. These miniature endoscopes enable high-quality, laser-based video images for minimally invasive procedures, but can also open the doors for novel bio-technology applications. The functional principle is based on a segmented miniature tube bonded to a single mode optical fiber running through the tube. The piezo tube is operated in resonant mode and by controlling the phase between the X and Y axes, a spiral scan pattern can be produced.
The application-specific actuator is miniscule, only 4mm long at 0.45mm diameter with very low power requirement for typical operation (5.5mW at 20V operating voltage).
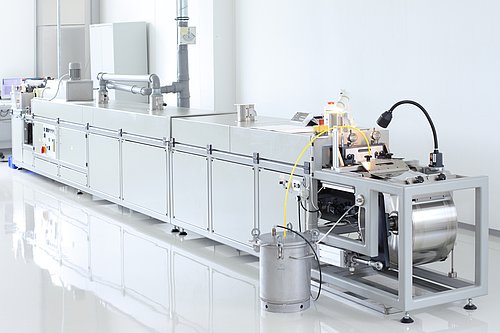
Miniature Piezo Plates for Micro Dosing and Nano Pumps
Miniature piezo transducer plates can be employed as the driving element in micro-dosing and nano-dosing pumps. Because the piezo elements can react to a drive signal change almost instantaneously, they can provide high pump frequencies and flow rates compared to their size. The drive signal amplitude determines the stroke and allows for a highly precise control of the dosing volumes.
Researchers at the Fraunhofer Institute for Microsystems and Solid State Technologies (EMFT) are working on an active implant to regulate intraocular pressure. The implant consists of a micro-pump system, with sensor-based pump control, an integrated, wirelessly rechargeable battery and a data transmission module. The implant can be applied directly to the eyeball. The driving force of the micropump is a piezo transducer disk applied directly to a silicon substrate. It generates the required motion very precisely and can be easily adapted to the application environment. Even with counter pressure, the delivery rates required for the therapy can be achieved by varying the switching frequencies or the amplitude of the piezo transducer by means of an appropriate control system. The pump in the eye implant operates at a maximum delivery rate of 30 microliters per second and, depending on the symptoms, can wet the eye or pump out aqueous humour.
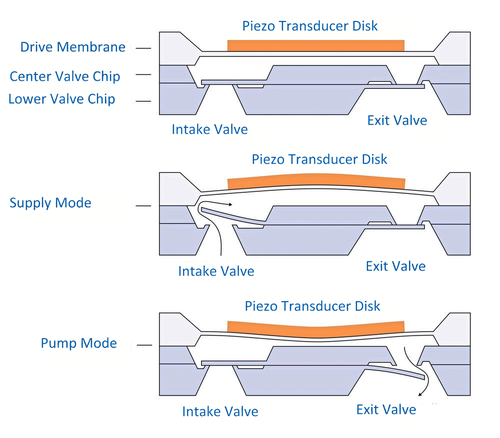
Blog Categories
- Aero-Space
- Air Bearing Stages, Components, Systems
- Astronomy
- Automation, Nano-Automation
- Beamline Instrumentation
- Bio-Medical
- Hexapods
- Imaging & Microscopy
- Laser Machining, Processing
- Linear Actuators
- Linear Motor, Positioning System
- Metrology
- Microscopy
- Motorized Precision Positioners
- Multi-Axis Motion
- Nanopositioning
- Photonics
- Piezo Actuators, Motors
- Piezo Mechanics
- Piezo Transducers / Sensors
- Precision Machining
- Semicon
- Software Tools
- UHV Positioning Stage
- Voice Coil Linear Actuator
- X-Ray Spectroscopy