A stepper motor is a brushless electric motor that divides one full rotation into several equidistant steps. You can command the position of the motor to hold and move at any one of those steps. There is no need for a closed-loop controller (involving a sensor and feedback loop) when the motor is sized to suit the application’s speed and torque requirements. Stepper motors serve a range of applications across several industries, thanks to reliability and cost-efficiency they offer in motion control.
Standard DC Electric Motors vs. Stepper Motor
Stepper motors rotate through well-defined steps or angles when operated with a suitable electronic control unit (linear stepper motors are also available, but less common). Unlike an ordinary DC electric motor that rotates continuously when a voltage is applied, a stepping motor can hold a position when energized.
Electromagnetic motors are based on the theory that like poles repel and unlike poles attract. When you feed DC electricity into a DC motor, it generates a torque and starts to rotate. The velocity depends on the voltage and torque depends on the current and velocity - DC motors provide the highest torque at 0 rpm. These types of motors are used in a wide range of equipment that requires continuous motion. However, they cannot stop at a predefined angle or lock into a discrete position without the help of additional sensors, and a more advanced closed-loop control circuit. Otherwise, the number of times they spin and their rotation angles are not predictable.
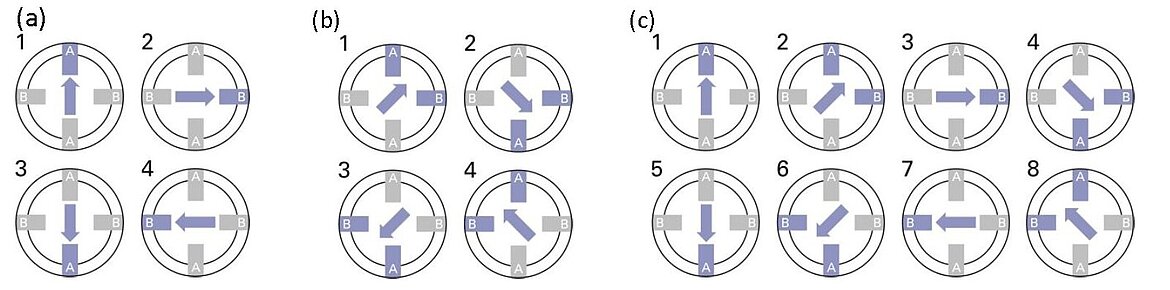
The stepper motor solves this problem. In its most simple form, a so-called two phase stepper motor makes use of two pairs of energized electromagnetic coils that can be switched on and off independently. The direction of the current going through the coils can also be switched. A relatively simple electronic controller takes care of the switching operation. There are four significant differences between a stepper motor is different from a regular DC motor (more ore information on brushless DC motors here).
- Regular DC motors have brushes and a commutator. Stepper motors have neither.
- In basic DC motors, inner coils rotate while the outer magnets stay static. In a stepper motor, the inside magnets rotate, and the outer coils remain static.
- Stepper motors have inner magnets divided into several sections. They also have corresponding teeth in the outer coils which supply the magnetic field that can be rotated or kept stationary.
- Stepper motors can remain still in a fixed position after rotating through a specific angle. This isn’t possible with a regular motor.
Controlling the Stepper Motor: Indexers and Drivers
In addition to the stepper motor that converts the digital pulses into the mechanical energy, two more elements are required:
- Indexers (or controllers): These are microprocessors which can generate direction signals and step pulses. They perform complex command functions.
- Drivers (or amplifiers): These amplify the control signals from the indexer, energizing the motor windings. Several driver types exist, with different current and voltage ratings and which utilize different technologies. Advanced drivers can perform microstep operations, dividing the output current into many discrete levels effectively multiplying the angular resolution of the motor.
Applications of Stepper Motors
Stepper motors are used for a large variety of motion control applications, including print head positioning in consumer ink-jet printers and high precision micropositioning tasks in the field of optics and lasers. You will find them used in linear stages and actuators, goniometers, mirror mounts, and rotation stages. They are also found in proportional valves for fluid control systems’ and in packing machinery. In terms of commercial use, you will find stepper motors in flatbed scanners, plotters, computer printers, slot machines, CD drives, and image scanners. They are also found in camera lenses, 3-D printers, CNC machines, and intelligent lighting.
In addition to the robotics industry, they are also widespread in medical equipment, aerospace spacecraft, and defense applications.
Summary: Advantages of Stepper Motors vs. Limitations
Advantages of Stepper Motors | Limitations of Open-Loop Stepper Motors |
---|---|
|
|
Other Types of Motors for Positioning and Motion Control Applications
With the ongoing cost reduction of sensors and electronics, brushless DC motors (BLDC) have become very popular and are starting to move into many applications that were once owned by stepper motors. BLDCs provide higher power density and higher velocity. For motion applications with the highest demand on dynamics, speed and accuracy, three phase linear and torque motors are used.
Blog Categories
- Aero-Space
- Air Bearing Stages, Components, Systems
- Astronomy
- Automation, Nano-Automation
- Beamline Instrumentation
- Bio-Medical
- Hexapods
- Imaging & Microscopy
- Laser Machining, Processing
- Linear Actuators
- Linear Motor, Positioning System
- Metrology
- Microscopy
- Motorized Precision Positioners
- Multi-Axis Motion
- Nanopositioning
- Photonics
- Piezo Actuators, Motors
- Piezo Mechanics
- Piezo Transducers / Sensors
- Precision Machining
- Semicon
- Software Tools
- UHV Positioning Stage
- Voice Coil Linear Actuator
- X-Ray Spectroscopy