A servomechanism, or servo for short, is a closed-loop device that produces motion in response to a command. These mechanisms can be driven by traditional electric motors, piezoceramics or even pneumatics and hydraulics. They utilize an electronic feedback loop to regulate the speed and direction of that motion using a feedback device to generate a position, velocity or even force signal. For long range precision motion, usually highly sensitive digital optical or magnetic linear encoders are used; for short ranges, analog sensors such as capacitance or strain gauges are also available. Modern encoders and sensors can provide precision in the nanometer range. Various servo positioner types are available on the market with high-precision applications favouring electromechanical device architectures and digital controllers.
In this blog post, PI outlines the basics of servo positioners in a little more depth.
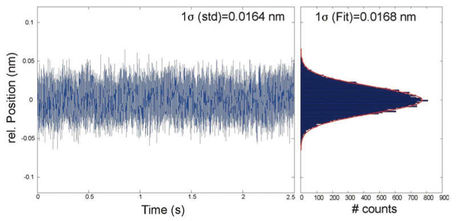
Precision Servo Positioners: The Basics
Servo positioners are comprised of multiple essential components; first and foremost, is the physical positioning stage. The stage platform can be driven by a rotary motor/screw combination or a linear motor. Outstanding accuracy of servo motor positioners can be achieved using a highly accurate position encoder, which continuously monitors the stage position and feeds data back to the controller. For motor/screw drives, a rotary encoder can be mounted on the motor, indirectly measuring the platform position.
A better, more accurate way is to mount a linear encoder on the stage with its read head attached to the moving platform, directly measuring the position. This represents one-half of the servo positioner’s closed-loop system.
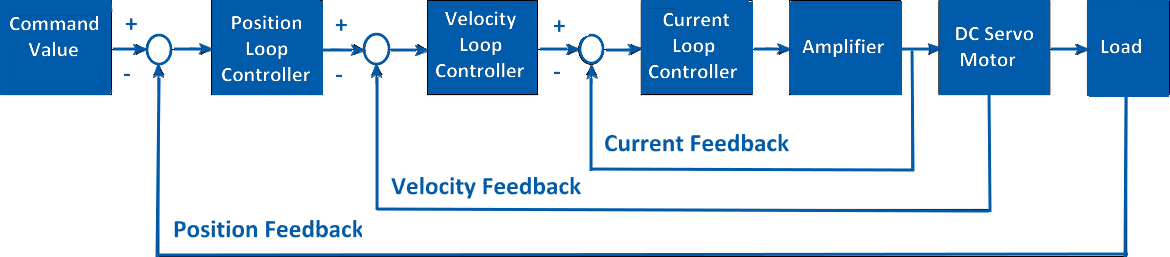
The second half requires a device controller which receives data from the encoder and regulates the electrical output signal to the motor. This is representative of the final command position for the servo positioner stage.
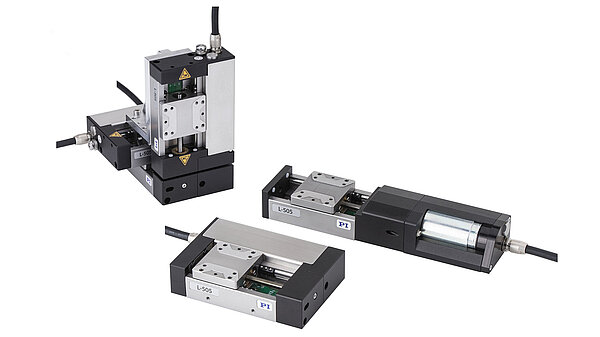
A good example of this basic device architecture is the L-505 Miniature Linear Stage, which is available with a DC servo motor and a linear encoder, as well as with stepper motors. It operates on the above principle to control a positioning stage with a linear travel range of up to 1 inch (26mm), a velocity of up to 0.6in/sec (15mm/sec), and a typical minimum incremental motion of better than 1 micrometer (µm). This is ideal for precision micro-assembly and research applications.
Classification of Servo Positioners
Servo motors are classified primarily on their current type; whether they utilise an alternating or direct current (AC/DC). AC-servo motors control rotation as a function of frequency, while in DC motors, rotation speed is directly proportional to the input voltage. The self-contained motor may also be classified as brushed or brushless, which determines whether the rotation is conducted mechanically with a commutator or electronically without. Learn more»
There is a diverse range of servo positioning stages available utilizing various design types and component options. For screw-driven positioners, lead screw or ball screw drives are generally employed. Lead screws can provide higher resolution and holding forces while ball screws provide improved throughput with higher speed capabilities and reduced friction. Screw-less linear stages can be driven by 3-phase linear motors or single-phase voice coil motors for short ranges. At PI, we provide servo positioners travel ranges of 5 – 1016mm (1/5” to 40”) and longer stage travel ranges upon request.
Our miniature servo positioners provide resolutions down to the single digit nanometer range and linear motor driven positioning stages can actually provide ½ nm steps as shown below.
Servo motors have also been utilized in rotation stages with outstanding resolution for turn table motion and unlimited rotational ranges. Direct drive versions with torque motors, are used for high loads and speeds, while miniature stages are often used in optical alignment applications. The RS-40 Miniature Rotation Stage from PI, for example, is available with a DC servo motor with a rotational range of 360° and an integrated rotary encoder with a sensor resolution of 2048 counts per revolution equivalent to 0.45µrad per count.
Servo Positioners from PI
PI is a world leader in the design and supply of precision motion and positioning mechanics and controllers for various high technology markets. We offer servo motor stages and controller modules to facilitate extremely precise, highly repeatable control in a range of manufacturing and research applications.
If you have any questions about our servo positioner products, please do not hesitate to contact a one of our application engineers.
Blog Categories
- Aero-Space
- Air Bearing Stages, Components, Systems
- Astronomy
- Automation, Nano-Automation
- Beamline Instrumentation
- Bio-Medical
- Hexapods
- Imaging & Microscopy
- Laser Machining, Processing
- Linear Actuators
- Linear Motor, Positioning System
- Metrology
- Microscopy
- Motorized Precision Positioners
- Multi-Axis Motion
- Nanopositioning
- Photonics
- Piezo Actuators, Motors
- Piezo Mechanics
- Piezo Transducers / Sensors
- Precision Machining
- Semicon
- Software Tools
- UHV Positioning Stage
- Voice Coil Linear Actuator
- X-Ray Spectroscopy