White Paper: Piezoelectric Transducers for Ultrasonic Surgery Tools
Materials and System Design Guidelines for Different Applications
Tools based on piezoelectric ultrasonic transducers are increasingly used in medical applications, including minimally invasive surgeries and dentistry. Common instruments used in advanced procedures are ultrasonic scalpels, phaco handpieces, and scalers. These devices leverage acoustic waves to efficiently process both hard and soft tissues. For instance, during oral surgery, ultrasound enhances mechanical actions like drilling, offering additional benefits such as shock or cavitation effects, leading to faster, more selective processing that safeguards surrounding areas, like blood vessels.
When addressing soft tissues like muscles, ultrasonic waves enable scalpel blades to oscillate at high frequencies, creating friction that allows for swift cutting and coagulation. This not only minimizes severe bleeding but also supports quicker hemostasis. The high energy density at the ultrasonic instruments’ contact point simplifies cutting, requiring less force and pressure, thereby making surgical incisions smaller and reducing trauma. Consequently, patients experience less postoperative pain, faster wound healing, and overall better recovery.
Moreover, ultrasonic medical tools can efficiently break down hard formations, such as tartar or kidney stones, through cavitation and acoustic forces, and liquefy soft tissues for minimally invasive removal, as seen in cataract surgeries (phacoemulsification) or wound debridement.
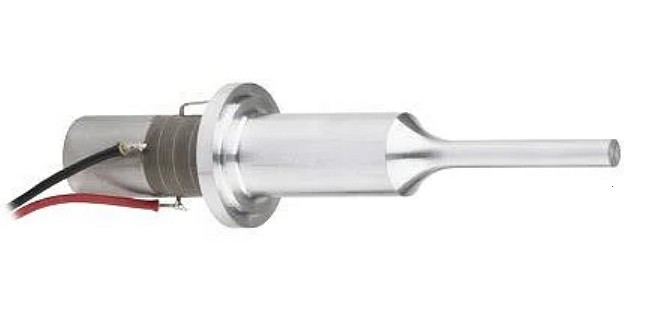
Ultrasonic devices, particularly scalers made from piezoelectric ceramics, are equipped with multi-functional features, including lighting, cooling water, gas, and suction options, enhancing their utility in procedures, such as tissue sealing and vascular surgery. These innovations highlight the significance of ultrasonic technology in advancing medical treatment and patient care.
Typical applications for piezoelectric ultrasonic scalers include:
- Tartar removal
- Intracorporeal stone disruption
- Ultrasonic scalpels and tissue sealing tools, e.g., in vascular surgery for coagulation
- Laparoscopic ultrasonic dissection
- Bone saws and drills, e.g., in orthopedics and maxillofacial surgery
- Ophthalmic phacoemulsification
- Ultrasound-assisted wound debridement
For more information, request the PDF.
Download the White Paper
Designing Piezoelectric Handpieces for Ultrasonic Surgery
How to find the Right Partner for Developing Ultrasonic Surgery Tools?
If you are seeking a piezo design partner for your next ultrasonic surgery instrument project, you want a company with extensive engineering expertise and advanced production machinery. You also want a company set up to take on custom projects with quick prototype delivery.
More Things to Consider
In-house development of piezoelectric materials: A partner with this ability provides consistent quality of all production processes and the flexibility to make custom modifications. Vertical integration with the entire supply chain in one hand guarantees short lead times and consistent high quality across all process steps.
Consulting and Manufacturing Expertise: Customers benefit from this crucial capability because it ensures that during the product development phase, there is a seamless integration of expertise to fine-tune piezo designs and specifications, aligning closely with the customer’s project needs.
Value-Added Designs: Offering more than mere components, the focus on value-added designs signifies a commitment to delivering comprehensive solutions that are ready for immediate integration. This approach saves time and ensures that the piezoelectric elements are optimized for their specific use cases through additional services like soldering, gluing, and assembly, thereby elevating the overall product quality.
Experience with Miniaturized Piezo Designs: The emphasis on miniaturization addresses the growing demand for compact, efficient solutions in microfluidics and other fields. A partner with advanced manufacturing capabilities to produce exceptionally small piezo components facilitates the development of innovative applications that require minimal space, opening new possibilities for device design and functionality.
Seamless Production Scalability: A partner with the ability to scale production seamlessly from prototype to full-scale manufacturing is essential for meeting the dynamic needs of the ultrasonic surgery tool market. This ability ensures quality consistency of piezo components across all batches and the flexibility to respond to fluctuating demand without compromising delivery timelines or product quality.
Cleanroom Manufacturing: A partner with stringent cleanroom standards ensures that all piezo components meet the high-quality requirements necessary for sensitive microfluidics applications. This meticulous approach to manufacturing under controlled conditions is vital for preventing contamination, thereby guaranteeing the reliability and performance of the components in various application environments.
Blog Categories
- Aero-Space
- Air Bearing Stages, Components, Systems
- Astronomy
- Automation, Nano-Automation
- Beamline Instrumentation
- Bio-Medical
- Hexapods
- Imaging & Microscopy
- Laser Machining, Processing
- Linear Actuators
- Linear Motor, Positioning System
- Metrology
- Microscopy
- Motorized Precision Positioners
- Multi-Axis Motion
- Nanopositioning
- Photonics
- Piezo Actuators, Motors
- Piezo Mechanics
- Piezo Transducers / Sensors
- Precision Machining
- Semicon
- Software Tools
- UHV Positioning Stage
- Voice Coil Linear Actuator
- X-Ray Spectroscopy