Steering Light: What is the Difference Between 2-Axis Galvo Scanners and Single Mirror 2-Axis Scanners
And a short look at other light steering methods
When it comes to steering light precisely in two dimensions, optical system designers have several established technologies at their disposal. Examples include galvanometer mirror scanners (galvo scanners) piezoelectric fast steering mirrors, voice coil-driven steering mirrors, kinematic mirror mounts, and gimbal mounts. Each one of these were designed for specific applications and this article will describe a few of their strengths and limitations.
2-Axis Galvo Scanners – 2 Individual Mirrors
These optical scanners consist of two independent, perpendicular rotating planar mirrors, arranged in a way that laser light bouncing off the first mirror (axis 1) will hit the second mirror (axis 2) and from there on, the target.
Galvo scanners are often used in laser material processing, and their large production numbers allow for relatively low cost. Due to the lightweight mirrors, highly dynamic motion in closed-loop operation is feasible, with step response times in the sub-millisecond range. Another advantage of galvo scanners is their large scanning field, typically around 20 degrees for both axes.
The downside of the dual single axis steering mirror design of a galvo scanner lies in the polarization rotation effect of this approach. This can cause issues with applications that rely on a defined state of polarization, such as certain types of interferometry, optical coherence tomography (a method that is gaining traction in dermatology), and in ellipsometry, an optical technique used to determine properties and thickness of films.
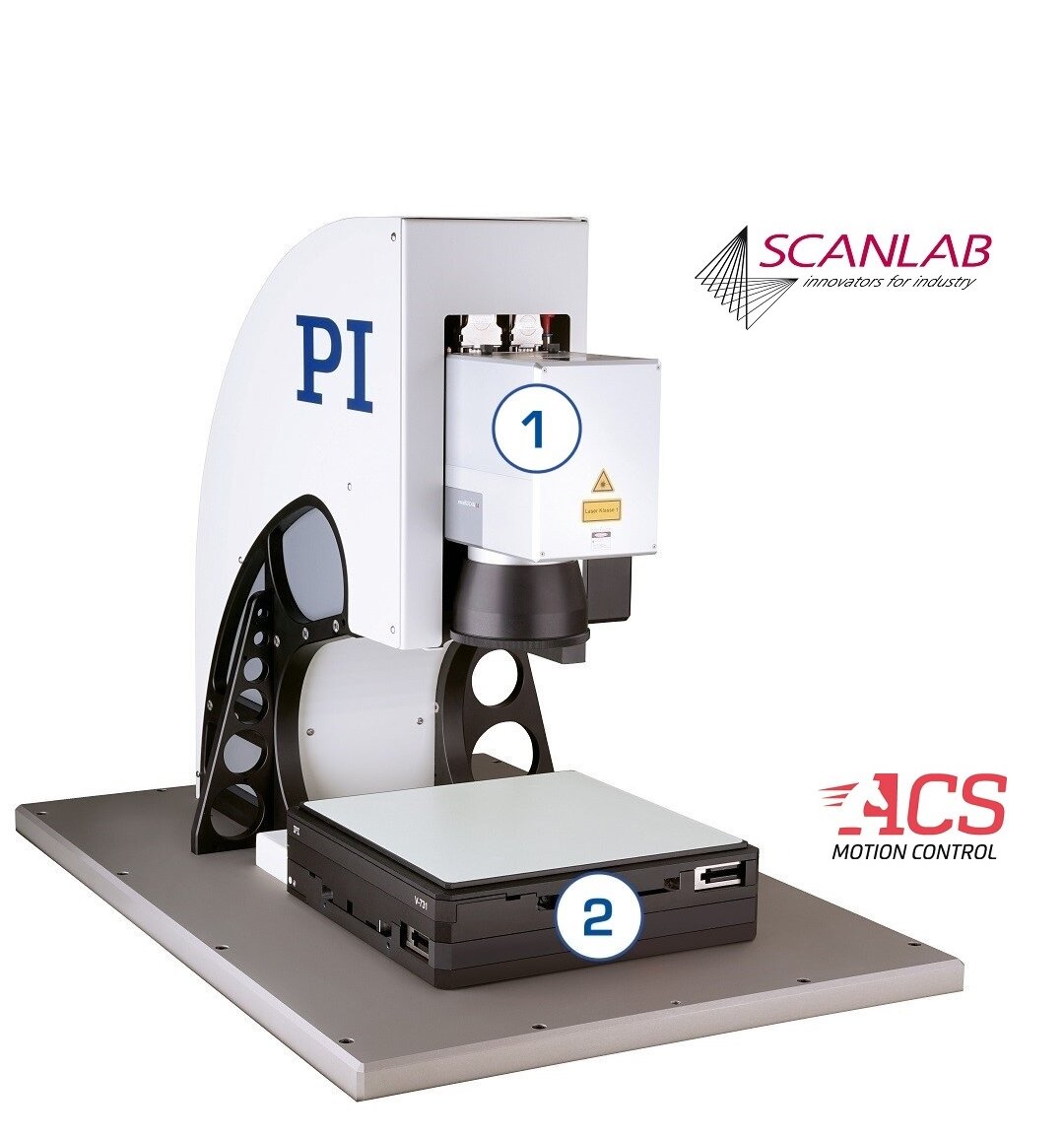
A) Piezoelectric 2-Axis Steering Mirrors
Piezoelectric fast steering mirrors (FSM) can be designed to provide angular deflection in two axes by tilting a single mirror around a fixed, common pivot point. These designs maintain the polarization of light, while also reducing the overall package size and improving robustness.
The guiding function for the mirror is provided by frictionless flexures which are ideal for the relatively small angles and high accelerations achieved with piezo drives. Flexures don’t require lubricants and are maintenance free; they work in high vacuum environments and over a wide temperature range.
Piezoelectric actuators react rapidly to changes in their operating voltage. Here, the speed of sound in the piezoceramic material is the limiting factor and for small piezoceramic elements, microsecond response times are feasible. While traditionally angular ranges for high-bandwidth, direct-drive piezo mirrors were limited to a few milliradians, novel designs, based on flexure motion amplifiers achieve optical deflection angles to 70mrad (4°).
For high-bandwidth, closed-loop operation and linearization, strain gauges are integrated in the piezo steering mirrors. A differential drive design with two actuator pairs operating in push pull, improves the angular stability across different temperature ranges significantly compared to a single actuator/axis approach.
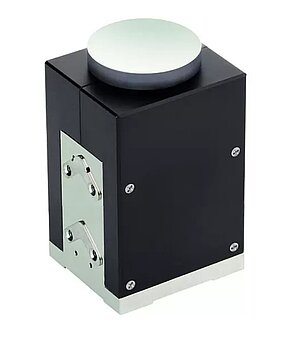
Flexure guided piezo mirror scanners are wear-free and do not require lubricants. They can run in ultra-high-vacuum conditions and can be designed to operate in space.
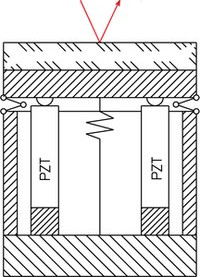
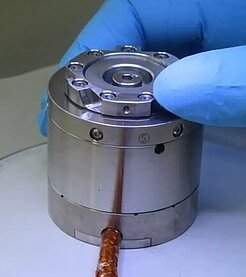
Advantages of piezo-driven steerable mirrors versus galvo scanners:
- Parallel kinematics (coplanar multi-axis motion without polarization rotation)
- The quadra-pod differential drive design (in S-335 and S-330 model families) run two orthogonal axes with a fixed pivot point based on two pairs of actuators operating in push / pull-mode.
- Channels/Axes can be operated simultaneously or independently, due to the paired piezo actuators in the design.
- Piezoelectric solid-state properties provide for fast response (sub-millisecond) and high resolution (down to the nanoradian range).
With no wearing parts, the reliability of piezo flexure guided steering mirrors is very high. Lifetime tests with more than 2 billion cycles were performed without any failures or degradation. The actuators integrated in the steering mirror used were 100 billion cycles life tested by NASA for the Mars mission.
Theta-X, Theta-Y, and Path-Length Modulation
Another parallel-kinematic steering mirror solution is based on a tripod piezo stack design. Here, in addition to Theta-X and Theta-Y rotation, the path length can be modulated as well, with sub-nanometer precision (phase modulation).
B) Voice Coil-Driven, Flexure Guided 2-Axis Steering Mirrors
Another solution for a single-mirror, 2-axis scanner is based on voice-coil motors and flexure guides. Due to the extended travel range of voice-coil motors (compared to piezo actuators), larger angular ranges can be achieved (beam deflection angles close to 10 degrees in Theta-X and Theta-Y). Using a quadra-pod differential drive design, excellent temperature stability is feasible as well.
Differences between a Piezo Drives and Voice Coil Drives
While piezo actuators are inherently stiff and can maintain a position with virtually no energy consumption and heat losses, voice-coils have no inherent holding force when de-energized and need to be powered to hold a position.
2-Axis Motorized Kinematic Mirror Mounts
Designed for Set-and-Forget Optical Alignment Applications with High Stability
Most commercially available kinematic mirror mounts allow active adjustments in two axes – often with micrometers or fine pitch screws. Kinematic mounts are often used in laser systems to adjust the beam path precisely, and then maintain the optimum position with very high stability.
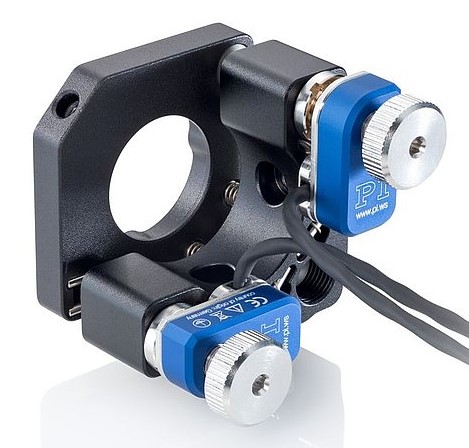
Motorized variants allow remote control, to automatically compensate for variations in system performance, to retune a complex optical system after shipping, etc. Since the axis of rotation of a kinematic optical mirror mount is located behind the mirror, the adjustments of both axes are not completely independent. In addition, a small linear translation of the beam will also occur with every angular adjustment. This shift also causes the axes to deviate from perfect orthogonality to the optical axis. Kinematic mirror mounts typically provide larger angular ranges compared to high-bandwidth piezo and voice coil steering mirrors but, usually less than 20 degrees.
The largest angular deflections are available from gimbal mount designs. Gimbals can provide rotation to 360 degrees in 1, 2 or 3 axes. The axes of a 2-axis optical gimbal mount intersect at the front and center of the attached optic and stay perfectly orthogonal. Gimbals can be designed for large mirror diameters and equipped with direct-drive motors are often used in high precision tracking applications.
Steering Light – What Technology Works Best for Your Application?
If your work involves highly precise or fast manipulation of light, such as image stabilization, laser beam steering, or laser processing, feel free to reach out to our engineering team for advice.
Blog Categories
- Aero-Space
- Air Bearing Stages, Components, Systems
- Astronomy
- Automation, Nano-Automation
- Beamline Instrumentation
- Bio-Medical
- Hexapods
- Imaging & Microscopy
- Laser Machining, Processing
- Linear Actuators
- Linear Motor, Positioning System
- Metrology
- Microscopy
- Motorized Precision Positioners
- Multi-Axis Motion
- Nanopositioning
- Photonics
- Piezo Actuators, Motors
- Piezo Mechanics
- Piezo Transducers / Sensors
- Precision Machining
- Semicon
- Software Tools
- UHV Positioning Stage
- Voice Coil Linear Actuator
- X-Ray Spectroscopy